Understanding Pharma QMS Software for Industry Success
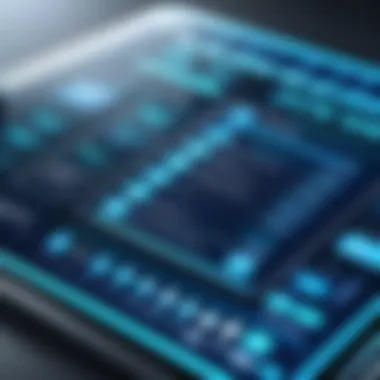
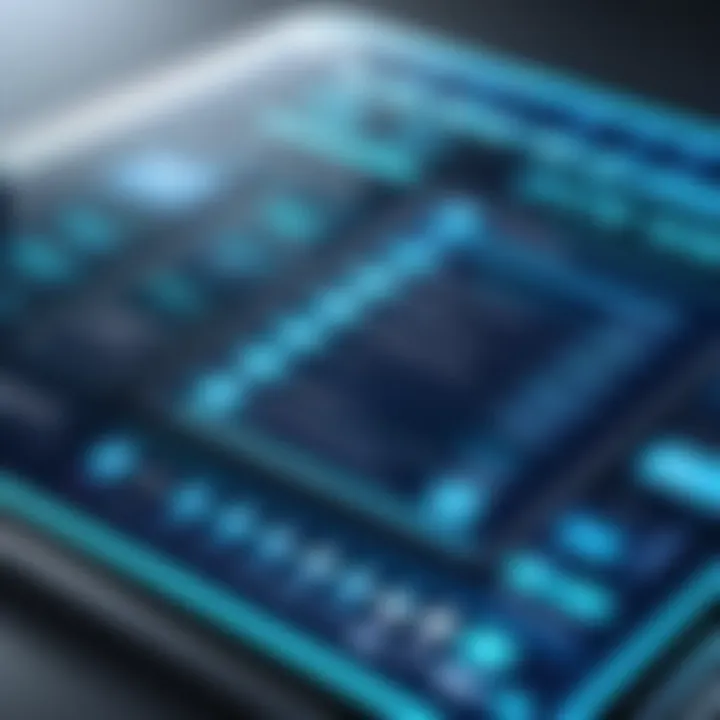
Intro
In the world of pharmaceuticals, a robust Quality Management System (QMS) is not just a luxury, it's a necessity. As organizations gear up to meet stringent regulations and maintain the highest standards of product safety, effective QMS software becomes an essential tool. This guide aims to shed light on the critical aspects of Pharma QMS software, exploring its core features, functionalities, and the diverse benefits it can bring to both small and large enterprises.
Software Overview
Understanding the landscape of Pharma QMS software is crucial for anyone looking to enhance their operational effectiveness. At its core, such software is designed to facilitate compliance with industry regulations and improve overall quality management processes.
Features and functionalities
Pharma QMS software typically includes a variety of functionalities that streamline quality assurance efforts. Some key features include:
- Document management: Helps in maintaining and controlling documents, ensuring the right versions are used.
- Audit management: Facilitates planning, execution, and tracking of audits to ensure compliance.
- CAPA management: Provides tools for Corrective and Preventive Action management, crucial for continuous improvement.
- Training management: Ensures that staff members are well-trained and compliant with necessary regulations.
These features not only help in regulatory compliance but also enhance overall efficiency, allowing pharmaceutical companies to focus on what matters most—their products.
Pricing and licensing options
When it comes to pricing, options can vary significantly based on the vendor and the specific needs of an organization. Generally, companies can expect:
- Subscription-based models: Monthly or yearly fees that are scalable based on user count.
- One-time licensing fees: A single payment that grants perpetual access to the software, often with additional costs for updates and support.
Supported platforms and compatibility
Compatibility is another important aspect to consider. Leading Pharma QMS solutions often support:
- Cloud-based platforms: Allow for remote access and scalability.
- On-premise installations: These may be preferred by larger enterprises concerned about data control.
The best software solutions will easily integrate with existing IT infrastructure, ensuring a seamless user experience.
User Experience
User experience is vital in ensuring that personnel can effectively utilize the software.
Ease of use and interface design
Intuitive design is paramount. Software that boasts a clean interface minimizes the learning curve, allowing users to navigate with ease. A well-structured dashboard that displays relevant metrics can empower teams to make informed decisions swiftly.
Customizability and user settings
Personalization of the software is essential. Customizability can range from interface adjustments to configuring workflows specific to the organization’s needs. This not only enhances usability but also improves system adoption rates among staff.
Performance and speed
Speed matters, particularly in time-sensitive industries like pharmaceuticals. Users expect rapid load times and efficient processing, particularly when dealing with extensive datasets or complex quality metrics.
Pros and Cons
Every software has its strengths and weaknesses. Here’s a look at some pros and cons of Pharma QMS software.
Strengths and advantages of the software
- Improved regulatory compliance, reducing the risk of penalties.
- Enhanced visibility into quality processes, leading to better-informed decisions.
- Greater efficiency in workflows through automation and tracking.
Drawbacks and limitations
- The initial investment can be steep for some smaller organizations.
- Thorough training is often needed to maximize the software’s potential, which can drain resources.
Comparison with similar products
A comparative analysis can help highlight what sets one software apart from another. For instance, comparing features, pricing, and user reviews might reveal that some products are better suited for certain applications.
Real-world Applications
Pharma QMS software is not just beneficial in theory; it finds practical application across a range of scenarios.
Industry-specific uses
The software can be tailored to meet specific needs within various sectors of pharmaceuticals including:
- Manufacturing: Assisting with batch record management and compliance tracking.
- Clinical trials: Ensuring integrity and compliance with trial protocols.
Case studies and success stories
Organizations often provide insights from real-world applications. For instance, a mid-sized manufacturer saw a 30% increase in compliance scores after implementing a specific QMS solution, demonstrating the tangible benefits of technology in quality management.
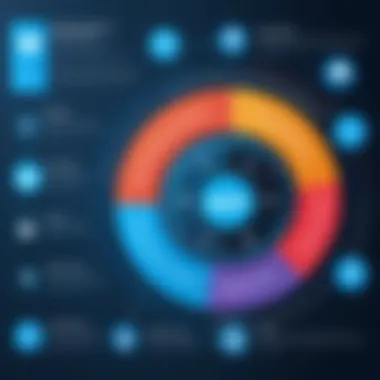
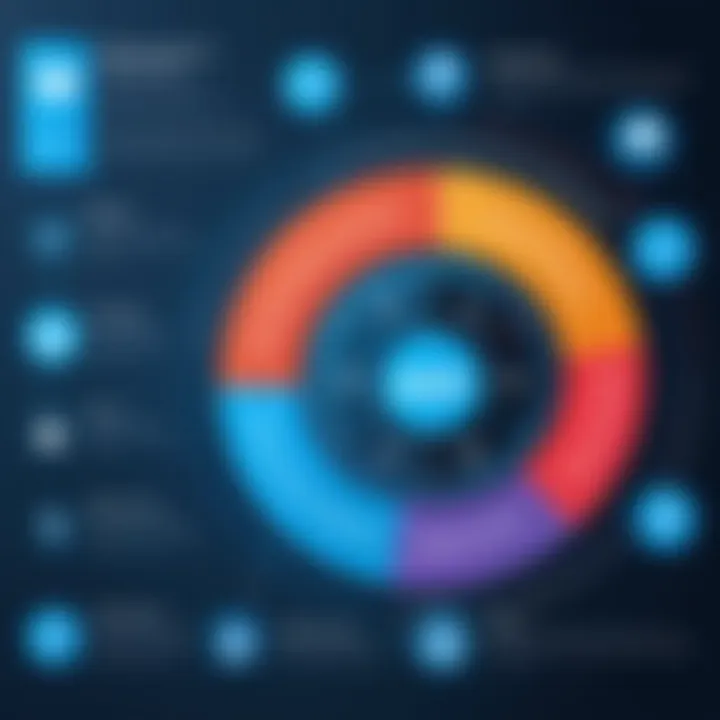
How the software solves specific problems
From managing deviations to facilitating audits, the right QMS software systematically addresses many quality-related issues, leading to smoother operations.
Updates and Support
Software maintenance and customer support play a pivotal role in the efficacy of Pharma QMS software.
Frequency of software updates
Regular updates ensure that the software remains compliant with changing regulations and improvements in technology. Reliable software providers will offer routine updates as part of their services.
Customer support options
Support can vary from basic email assistance to comprehensive service with dedicated account managers. Organizations should prioritize vendors that provide robust support.
Community forums and user resources
A vibrant community or extensive support documentation can also assist users in problem-solving and maximize their use of the software.
"In the realm of pharmaceuticals, where precision is paramount, the right tools truly make all the difference in maintaining quality and compliance."
This guide offers a lens into the multifaceted role of Pharma QMS software, paving the way for informed decision-making in a critical industry.
Prolusion to Pharma QMS Software
In the fast-paced pharmaceutical industry, where precision and compliance take precedence, the role of Quality Management System (QMS) software cannot be overstated. Pharma QMS software serves as the backbone of quality assurance efforts, helping organizations maintain the highest standards in all their processes. Tackling the intricacies of regulatory demands, operational efficiency, and product integrity is no mean feat. This article aims to illuminate the critical role that QMS software plays in achieving those goals.
The Importance of QMS Software in Pharma
- Streamlining Compliance: With ever-changing regulations from bodies like the FDA and EMA, keeping up can feel like trying to catch smoke with your bare hands. Pharma QMS software simplifies compliance by providing a framework that aids organizations in adhering to these regulations effortlessly. By automating documentation and tracking changes systematically, companies save time and reduce the risk of oversight, which can lead to costly penalties.
- Enhancing Product Quality: Quality assurance is not just a checkbox; it’s an ongoing commitment. Companies that implement robust QMS software witness a noticeable improvement in product quality. Integrating data from various sources allows for quicker identification of any issues that may arise in the manufacturing or testing phases.
- Boosting Efficiency: Efficiency is where QMS software shines. It reduces the paperwork that often bogs down teams and instead allows for digital solutions to manage records and workflows. This streamlined approach not only speeds up processes but also fosters a culture of accountability. When roles are well-defined and software facilitates smoother operations, everyone from R&D to production can focus on what really matters—creating effective therapies and medications.
- Facilitating Risk Management: In an industry where risk is rampant, be it from external audits, product recalls, or regulatory fines, risk management mechanisms offered by Pharma QMS software are invaluable. Built-in features that assess and mitigate risks empower organizations to stay ahead of potential issues before they escalate. It’s like having a safety net that catches you before you hit the ground.
However, despite the clear advantages, there's no silver bullet. Implementing QMS software comes with challenges of its own, such as integration complexities and user adaptation. Recognizing these hurdles early can better prepare companies for a smooth transition.
In summary, understanding Pharma QMS software is pivotal for any organization in the pharmaceutical sector. Emphasizing compliance, efficiency, accountability, and product quality is not just operational best practice; it's a necessity. This introduction sets the stage for a deeper dive into the foundational principles and key features of QMS that will follow in this guide.
"A robust QMS is not just essential; it’s the linchpin holding together the pillars of quality in the pharmaceutical industry."
Stay tuned as we explore the core principles that define these systems, shedding light on the regulatory frameworks that shape their implementation.
Defining Quality Management Systems
Quality Management Systems (QMS) serve as the backbone of operations within any organization, particularly in the pharmaceutical industry. When we talk about defining QMS, we delve into the structured framework that helps ensure that products meet specific standards of quality. Essential elements of a QMS encompass policies, procedures, and responsibilities that guide an organization in improving processes, products, and services. Adopting these systems isn't simply a trend; it's pivotal for compliance, efficiency, and accountability.
Understanding a Quality Management System can help organizations avoid costly mistakes and produce higher-quality products. By prioritizing quality at every step, from development to delivery, businesses can foster consumer trust and meet regulatory expectations. The investment in QMS pays off not only in terms of compliance but also in boosting the overall productivity and operational effectiveness.
Core Principles of Quality Management
Core principles lay the groundwork for a successful QMS. These principles serve as a guiding light, ensuring that every process aligns with the organization's goals.
- Customer Focus: This principle emphasizes understanding and fulfilling customer needs. Satisfied customers lead to repeat business, reinforcing the importance of quality from the customer's perspective.
- Leadership: Strong leadership is necessary for establishing unified directions. Leaders must cultivate an environment that promotes engagement and brings staff together towards a common objective.
- Engagement of People: Involve every employee in quality management. A committed workforce can contribute ideas that enhance quality and improve processes.
- Process Approach: Activities should be understood as processes, which promotes iterative improvements over time. This approach helps in identifying inconsistencies and bottlenecks that could hinder quality.
- Continuous Improvement: Organizations are encouraged to adopt a mindset of ongoing improvement. This habit can help them remain competitive and adapt to changes in regulations and market demands.
Regulatory Frameworks Influencing QMS
In an industry as tightly regulated as pharmaceuticals, understanding the frameworks that influence QMS is crucial. Regulatory bodies outline the expectations and standards necessary for maintaining safety and efficacy. Notably, the FDA and ISO provide comprehensive guidelines that pharmaceutical companies must adhere to.
FDA Regulations
FDA regulations are designed to protect public health. They lay out the stringent requirements that pharmaceutical companies need to follow in their operations. One key characteristic is the GMP (Good Manufacturing Practice) which ensures products are produced consistently and controlled according to quality standards. This is vital for trustworthy outcomes.
These regulations make a solid choice for organizations aiming for compliance, but the landscape can be challenging. An important unique feature is the requirement for documentation at every stage of the manufacturing process.
Key Features of Pharma QMS Software
In the realm of pharmaceutical manufacturing and distribution, the importance of Quality Management System (QMS) software cannot be overstated. A robust QMS software solution acts as the backbone for maintaining the integrity and compliance of processes that are critical to product safety and efficacy. Understanding the key features of Pharma QMS software is vital for organizations keen on fortifying their operations, enhancing compliance, and managing risks effectively. Each feature encompasses unique capabilities that address the nuanced needs of the pharmaceutical sector.
Document Management
Effective document management is a cornerstone of any Pharma QMS software. In an industry laden with regulations, it’s imperative that all documents, from standard operating procedures (SOPs) to training manuals, are easily accessible, properly versioned, and under control. This particular feature allows teams to:
- Store Documents Centrally: A centralized repository ensures that all employees have access to the latest documents, reducing the likelihood of working off outdated information.
- Automate Workflows: Automation speeds up the process of document approvals, reviews, and revisions, ensuring that essential documents are consistently up-to-date.
- Maintain Compliance: Audit trails and compliance checklists within the document management system facilitate adherence to regulatory requirements, thereby mitigating risks associated with audits.
In short, managing documents effectively saves time and maintains the consistency needed in the high-stakes environment of pharmaceuticals.
Change Control Management
Change is inevitable in any process, yet managing that change smoothly is critical in the pharma industry. A Pharma QMS software equipped with robust change control management functionalities helps in:
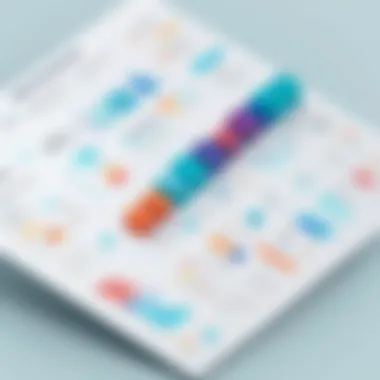
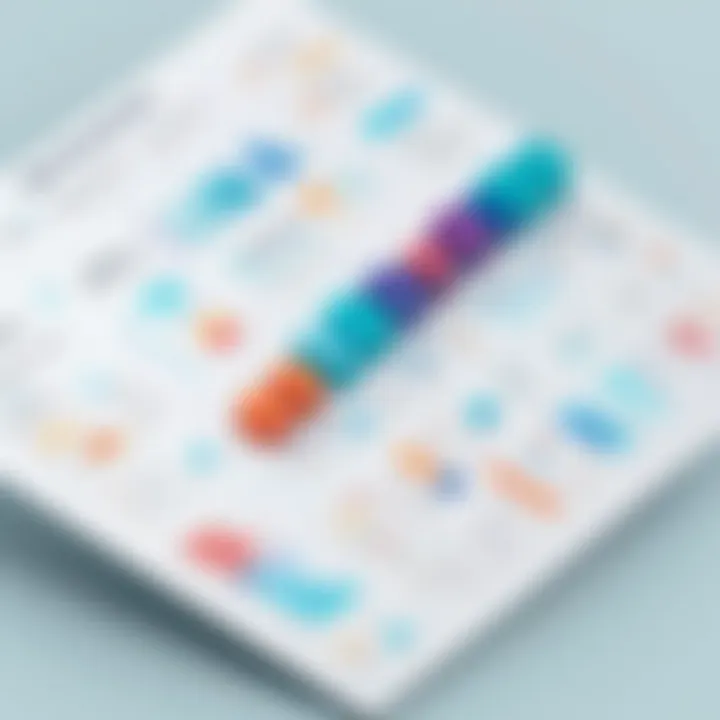
- Tracking Changes: Every alteration, whether in process, materials, or equipment, must be documented and scrutinized. Change control features facilitate documentation that lays down who made changes, when, and why.
- Evaluating Impact: Before implementing changes, it's crucial to assess their implications on compliance and product quality. Good software provides tools to forecast potential impacts and ensure that risks are effectively managed.
- Standardizing Procedures: By creating standardized procedures for approving changes, organizations ensure that modifications do not compromise product integrity or regulatory adherence.
This feature makes adapting to new regulations and practices less stressful and more systematic.
Training Management
The pharmaceutical industry hinges on knowledge and competencies. Training management within QMS software is designed to ensure that all personnel are adequately trained and qualified to perform their tasks. Key aspects include:
- Tracking Training Requirements: This allows organizations to ensure that employees complete mandatory training on time, thus keeping skillsets current.
- Documenting Competencies: Maintaining records of training helps in adhering to regulatory requirements and in preparing for audits, reflecting that the workforce is qualified.
- Facilitating Upskilling: As processes evolve, continual learning is key. Training management helps identify areas for upskilling, ensuring that employees stay ahead of industry trends and regulations.
In essence, effective training management within QMS software bridges the gap between compliance and operational efficiency.
Risk Management
Navigating risks is a part and parcel of the pharmaceutical industry. A competent Pharma QMS software integrates risk management features that allow companies to identify, analyze, and mitigate risks throughout the product lifecycle. Important elements include:
- Risk Assessment Tools: Tools embedded within the software help in visualizing potential risks, allowing for a preemptive approach to quality issues before they escalate into major problems.
- Implementation of Mitigation Strategies: Once risks are identified, the software helps implement corrective actions and monitor their effectiveness, ensuring that the intended outcomes are met.
- Continuous monitoring: Risk management is not a one-and-done task; ongoing monitoring of processes ensures that emerging risks are flagged and dealt with swiftly.
By focusing on risk management, pharmaceutical companies can enhance their resilience in a market fraught with uncertainties.
In summary, the key features of Pharma QMS software lay the foundation for maintaining compliance, enhancing efficiency, and promoting a culture of quality within organizations. Knowing how to leverage these features effectively can lead to significant improvements in operational outcomes and regulatory standing.
Benefits of Implementing Pharma QMS Software
In an industry as strictly regulated as pharmaceuticals, Quality Management System (QMS) software plays a crucial role. Organizations that implement these systems see an array of benefits that impact compliance, efficiency, and accountability across their operations.
The adoption of QMS software is not merely a trend; it’s a strategic move that can lead to improved product quality and reduced risks. Below, we delve into the three most significant advantages of using pharma QMS software.
Enhanced Compliance
Compliance with regulations is non-negotiable in the pharmaceutical sector. QMS software provides organizations with a structured approach to adhere to industry regulations such as those set forth by the FDA or EMA.
- Real-time monitoring: The software enables continuous monitoring of processes, ensuring any deviations from compliance are detected early.
- Document control: A robust QMS system allows for effective management of critical documents and records. It ensures that all necessary documentation is up-to-date and easily accessible, right when inspectors come calling.
- Audit trails: With automated tracking features, companies can maintain comprehensive audit trails. This not only proves compliance during inspections but also highlights areas needing improvement, creating a cycle of ongoing refinement.
"A strong QMS is not just about following rules; it’s about fostering a culture of quality."
Improved Efficiency
In the fast-paced world of pharmaceuticals, efficiency is king. Pharmas don’t have the luxury of dragging their feet. QMS software can significantly streamline operations and promote a more agile work environment.
- Automation of routine tasks: With manual processes eliminated, staff can focus on higher-value tasks, from R&D to sales.
- Centralized information repository: A single platform where all quality-related information resides enhances communication among teams. No more searching for that email or document buried deep in the archives.
- Faster response times: In the event of quality issues, a QMS allows organizations to react swiftly, thereby minimizing potential losses and safeguarding reputation.
Increased Accountability
Creating a culture of accountability within an organization can make or break operational success. Pharma QMS software enhances accountability in multiple dimensions.
- Defined roles and responsibilities: The software typically includes functionalities that clarify who is answerable for various aspects of quality. This prevents any finger-pointing that can occur during issues.
- Performance metrics: QMS software tracks performance levels against key performance indicators (KPIs). Regularly reviewing these metrics holds teams accountable for their contributions to quality initiatives.
- Feedback loops: Facilitated by the software, immediate feedback mechanisms ensure that personnel know the implications of their actions on quality, fostering a sense of ownership.
In essence, implementing pharma QMS software is not merely a box-ticking exercise. It is about carving out a pathway to enhanced compliance, improved efficiency, and increased accountability across the pharmaceutical landscape. As organizations weigh the risks and rewards of adopting these solutions, five-star results are certainly achievable.
Challenges in Adopting QMS Software
Adopting Quality Management System (QMS) software in the pharmaceutical sector comes with its own set of challenges. The pressures of regulatory compliance and the need for efficiency compel organizations to leverage technology, but integrating it often requires a calculated approach. When diving into the challenges, we start to see how integral effective implementation is for any organization. It's not just about having software; it's about ensuring that it works seamlessly within an existing ecosystem while empowering users to engage with it fully.
Integration with Existing Systems
The most notable hurdle is integration with existing systems. Many pharmaceutical companies already utilize various information systems for managing data, quality control, and compliance. Therefore, introducing a new QMS software can create a friction point. A common scenario involves legacy systems that may not easily communicate with contemporary QMS solutions. For instance, if a firm is still relying on outdated document management methods—such as paper records or standalone digital solutions—this can lead to discrepancies in data, causing confusion and potentially impacting compliance.
- Compatibility Issues: Not all QMS solutions are designed to be compatible with every other system. This compatibility gap can lead to wasted time and resources during integration.
- Data Migration Challenges: Moving data from legacy systems to a new QMS can be precarious. There’s always the fear of losing vital data or introducing errors during transition, which can have dire consequences in a regulated industry.
- Time-Consuming Implementation: Integrating a new QMS software often does not happen overnight. It involves a systematic approach that can take weeks or even months, during which normal operations can feel like they are on hold.
In light of these factors, organizations must consider conducting comprehensive audits of their existing systems before selecting a QMS solution. This step not only mitigates future integration headaches but also helps in choosing a software that complements and enhances existing processes.
User Resistance and Training Needs
Another significant challenge stems from user resistance and training needs. Change is often met with reluctance, particularly in organizations where employees are accustomed to their current workflows. The introduction of new software can evoke a sense of unease, leading to pushback from staff.
- Cultural Barriers: One great impediment can be organizational culture. Often, teams may feel a lack of ownership over the new system, especially if they weren't part of the selection process. This disconnect can lead to a poor adoption rate.
- Need for Comprehensive Training: Just because the software is state-of-the-art doesn’t mean that employees can use it effectively. Organizations will face additional challenges if they don't provide comprehensive training. Without proper training, staff may struggle with the software's functionalities, leading to mistakes, which can result in compliance issues.
- Support Structures are Crucial: When transitioning to QMS software, companies should have dedicated support for users. This includes help desks for questions and troubleshooting as well as ongoing training sessions. The more support employees receive, the more likely they are to embrace the new tools at their disposal.
Employers have to actively work to support their teams in this transition. Clear communication about the benefits of using the new QMS can help ease fears, while targeted training sessions can empower employees to take advantage of the software's features.
A successful QMS software adoption hinges on addressing resistance through openness and sufficient support, creating ambassadors for the new system within the organization.
Choosing the Right Pharma QMS Software
Choosing the right Pharma QMS software is a fundamental turning point for organizations in the pharmaceutical industry. With regulatory demands on the rise and an ever-changing landscape of compliance requirements, the right software solution can make or break operational success. A poorly chosen system may lead to wasted resources, ineffective processes, and compliance pitfalls—none of which bode well for any business looking to thrive in this sector. Therefore, it's important to grasp not just the features offered but also the vendors behind those features and how they align with your company’s needs and objectives.
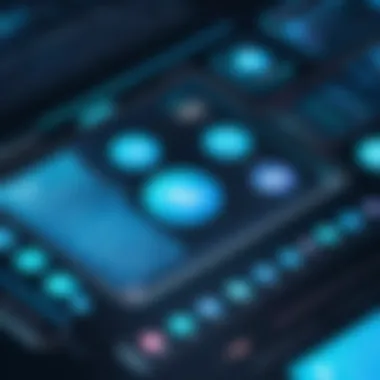
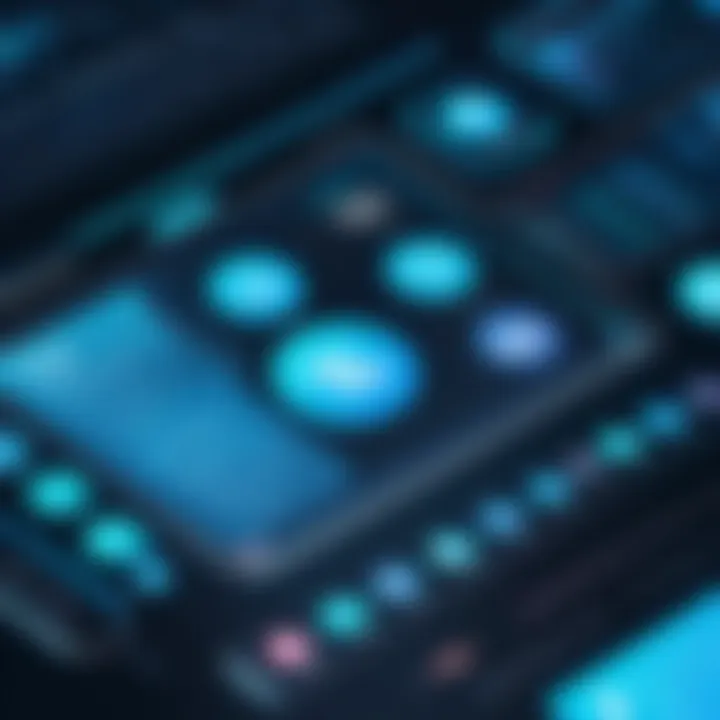
When considering how to navigate this selection process, various factors come into play that should guide your decision-making. Here, we break it down into three essential components.
Evaluating Software Vendors
Vendor evaluation is central to the decision-making process. Not all software is created equal, and hence, each vendor brings a different mix of benefits and drawbacks. Here are several factors to keep in mind:
- Reputation and Experience: Check the vendor's track record in the pharmaceutical industry. A vendor that has spent years serving pharma companies understands unique challenges and regulatory constraints.
- Support Services: What’s their post-purchase support like? You want a vendor who offers continuous support, training, and resources—think about long-term success, not just the initial procurement.
- Customization Capabilities: Every business is unique. A one-size-fits-all solution might not do the trick. Ensure the vendor can customize their offering to fit your specific requirements.
Consider reaching out to current users of the software to gauge their experiences with the vendor. Sometimes, firsthand accounts can reveal strengths or weaknesses you might not find in a product brochure.
Cost Considerations
While cost should never be the sole factor when choosing QMS software, it’s certainly essential. When budgeting for software, consider these points:
- Upfront Costs vs. Long-Term Value: Look beyond the initial price tag. Consider maintenance fees, upgrade costs, and other recurring expenses that can creep up over time. Is the software scalable? Will it continue to add value as your business grows?
- Training Expenses: Don’t forget to factor in the costs associated with user training. A complex system may require more in-depth training, which can add additional expenses.
- ROI Calculations: Assess how the software can improve efficiency and compliance. For instance, if implementing the QMS software ultimately reduces compliance errors and improves product quality, those benefits can outweigh the initial costs.
User Feedback and Reviews
User feedback can be a game changer in your decision-making process. Seek out reviews and ratings from platforms like Reddit or even industry-specific forums. Here’s why user feedback matters:
- Real-World Insights: Users provide perspectives and opinions that marketing materials simply can't capture. Hearing what others have experienced will help you understand the pros and cons better.
- Common Issues: The software may have outstanding features, but it’s critical to know about any recurring issues users have faced.
- Community Engagement: Some vendors cultivate a community among users. Engaging in such a community can offer ongoing value, from updates to shared insights regarding QMS best practices.
"In the landscape of pharma QMS software, knowledge is just as important as the software itself. Your choice today shapes your operational future."
The right Pharma QMS software isn’t just a tool; it’s an integral part of your strategy for success in the pharmaceutical industry. Keeping these factors in mind strengthens your approach to choosing a solution that genuinely aligns with your operational goals.
Future Trends in Pharma QMS Software
As the pharmaceutical landscape evolves, the significance of Quality Management System (QMS) software becomes ever more paramount. Keeping pace with advancements in technology ensures that organizations not only meet but also exceed the stringent requirements set forth by regulatory bodies. This section delves into the emerging trends shaping the future of Pharma QMS software, spotlighting two major areas: the integration of AI and automation, and the shift toward cloud-based solutions.
Integration of AI and Automation
Integrating AI into Pharma QMS software is not just a fleeting trend; it's becoming a foundational element driving enhanced efficiency. Artificial intelligence enables predictive analytics, which can foresee compliance risks and operational bottlenecks before they escalate into larger issues.
- Real-time Monitoring: AI tools can continuously assess processes and can flag any deviations immediately. This is like having a watchful eye that never blinks, ensuring quality standards are maintained without fail.
- Process Optimization: With machine learning algorithms at work, organizations can analyze historical data to identify inefficiencies. The result? Streamlined processes that reduce waste and improve outcome predictability.
- Automated Documentation: The tedious task of compliance documentation can be transformed through automation. Instead of individuals scrambling to prepare reports during audits, software can generate these documents in real-time, relieving staff to focus on their core responsibilities. Organizations stand to save not only time but also money by reducing manual errors and mitigating the risks associated with documentation lapses.
"Implementing AI in quality management allows for a proactive rather than reactive approach to compliance."
Cloud-Based Solutions
The trend toward cloud-based QMS solutions is gaining traction, as it offers substantial benefits over traditional on-premise systems. These solutions allow for greater accessibility and flexibility, critical attributes in today’s fast-paced environment.
- Accessibility: Cloud software enables teams across various locations to access critical quality management tools anytime, anywhere. Imagine a team in Boston collaborating with colleagues in Beijing in real-time—cloud technology makes this possible.
- Scalability: As companies grow, so do their needs. Cloud solutions often allow easy scalability, meaning businesses can expand functionalities without significant lags in implementation. It's like planting a tree—you can choose to prune or expand its branches as it grows.
- Cost Efficiency: Cloud solutions typically involve lower upfront costs than installing massive servers on-premise. Subscription-based models help organizations plan budgets with greater accuracy, resulting in less financial strain on resources.
Case Studies and Real-World Applications
The practical implications of Quality Management System (QMS) software in the pharmaceutical industry cannot be overestimated. By examining case studies and identifying real-world applications, we can gain insights into how these systems are being adopted and the tangible benefits they provide to organizations. A deep dive into this area helps illustrate the software's functionality, effectiveness, and strategic importance in improving regulatory compliance and operational efficiencies.
Case studies offer a window into the unique challenges faced by various organizations and how tailored solutions can address these issues. They often highlight specific instances where improvement was not just a goal but a necessity, particularly in an industry where compliance violations can lead to severe consequences. By reviewing these success stories, companies can understand the measurable benefits that QMS software brings to their operations.
The benefits of learning from these case studies include:
- Understanding diverse applications: Different companies may approach QMS software implementation with unique objectives and strategies, showcasing the software's versatility.
- Gauging risk versus reward: Businesses can better weigh the pros and cons of various QMS tools, helping in their decision-making processes.
- Inspiring innovation: Observing others' successes often spurs creativity, leading organizations to adapt or enhance their own practices.
Success Stories
One notable success story comes from a midsize pharmaceutical company that faced obstacles with managing its extensive documentation processes. After implementing a robust QMS software solution, they experienced a significant reduction in document retrieval times and compliance-related discrepancies. Not only did they save time, but employees also reported an increase in job satisfaction due to the streamlined processes. This successful transition demonstrated how effective document management can lead to greater operational efficiency.
Another impressive example comes from a major biopharmaceutical firm known for developing life-saving drugs. They struggled with tracking training requirements for their staff, leading to lapses in compliance and unsettling audits. By adopting a training management feature in their QMS solution, they not only revamped the training process but also ensured consistent follow-through. This initiative measurably improved compliance scores during FDA inspections, illustrating the software’s impact on regulatory adherence.
Lessons Learned
From these success stories, several valuable lessons emerge regarding the implementation of Pharma QMS software:
- Start with a clear vision: Having a defined understanding of what one hopes to achieve with QMS software is crucial. Whether it’s addressing compliance issues or improving efficiency, clarity should be the backbone of all decisions.
- Involve stakeholders early: Gaining buy-in from different departments ensures that all needs and concerns are addressed. This approach not only minimizes resistance to change but also enhances the software's effectiveness.
- Invest in training: Even the most sophisticated software can fall flat if users do not know how to utilize it properly. Organizations should prioritize comprehensive training sessions to ensure users can maximize the tool's potential.
"Understanding where others have succeeded can provide both caution and inspiration, guiding new implementations in the right direction."
Finale
In wrapping up the conversation on Pharma QMS software, it's worth emphasizing just how critical these systems are within the pharmaceutical landscape. As the healthcare industry increasingly evolves, the necessity for stringent quality control escalates. This is where Quality Management Systems play a pivotal role.
Pharma QMS software not only ensures compliance with regulations, but it also contributes to significant improvements in operational efficiency. For example, instead of relying on outdated methods like spreadsheets or paper-based processes, organizations can harness advanced tools that streamline documentation and enhance collaboration among team members. In this way, the software becomes more than just a requirement; it shifts to a strategic asset.
Benefits include:
- Enhanced data integrity: Automation of quality processes dramatically reduces human errors.
- Real-time tracking: Easier monitoring of compliance status and potential risks.
- Informed decision-making: Comprehensive reporting facilitates deeper insights.
However, it’s essential to consider potential challenges that may arise. Effective implementation of such systems requires robust strategies for integration with existing workflows and necessary training for the users. Indeed, investing time to nurture a culture that embraces new technologies pays dividends in enhancing overall quality.
"A small investment in a Pharma QMS could save significant costs later, ensuring that quality and compliance are never just box-ticking exercises."
As companies continue to adapt to new regulations and expectations from stakeholders, Pharma QMS software will remain at the forefront of facilitating better practices. In our ever-competitive world, the stakes are high—not just for the organizations but also for the patients who depend on safe and effective medications. A well-chosen quality management system could very well be the difference between a thriving business and a compliance nightmare.