Optimizing Warehouse Operations: The Ultimate WMS Guide for 3PL Providers
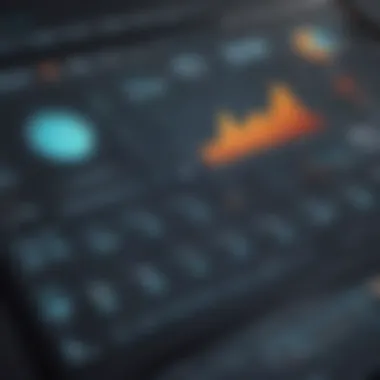
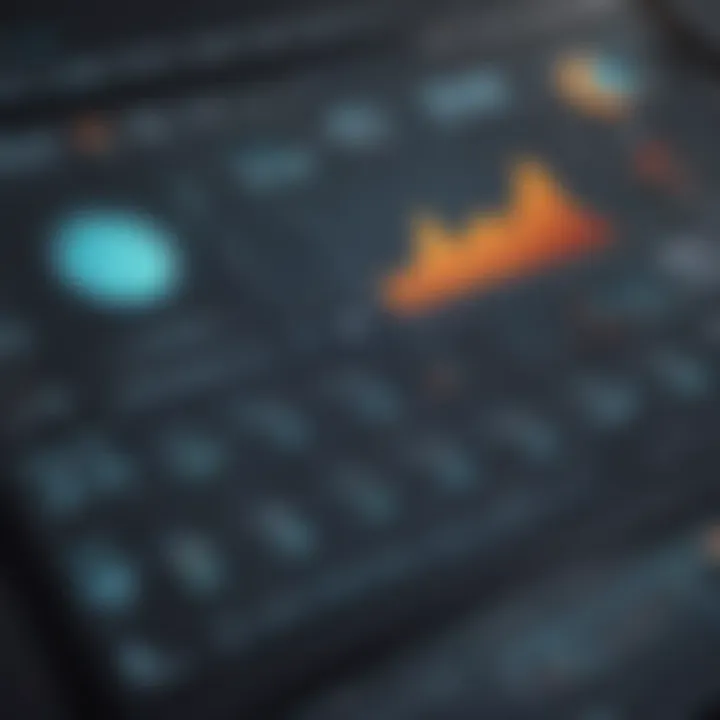
Software Overview
Warehouse Management Systems (WMS) tailored for Third-Party Logistics (3PL) providers are paramount in enhancing operational efficiency. These systems offer a myriad of features and functionalities crucial for 3PL companies to streamline their warehouse operations effectively. From inventory management to order fulfillment, a robust WMS can significantly optimize processes in the logistics chain. Pricing and licensing options vary among providers, with some offering scalable solutions based on the size and needs of the 3PL business. Supported platforms and compatibility are essential considerations to ensure seamless integration with existing systems.
User Experience
The user experience plays a pivotal role in the effectiveness of a WMS for 3PL. An intuitive interface design and ease of use are vital for swift onboarding and minimal training requirements. Customizability and user settings allow 3PL companies to tailor the WMS to their specific workflows and requirements. Performance and speed are critical factors, determining the system's ability to handle large volumes of data and transactions efficiently.
Pros and Cons
Real-world Applications
Updates and Support
Regular software updates are essential to ensure the WMS remains reliable, secure, and up-to-date with industry standards. Customer support options such as live chat, ticketing systems, or dedicated account managers are crucial for addressing any queries or issues promptly. Community forums and user resources provide an invaluable platform for sharing best practices, troubleshooting tips, and fostering a sense of camaraderie among users.
Introduction
Warehouse Management Systems or WMS plays a crucial role in the efficient functioning of Third-Party Logistics or 3PL providers. Within the realm of logistics, the seamless integration and optimization of warehouse operations are pivotal for enhancing overall performance. This section will delve deep into the intricate workings of WMS tailored specifically for 3PL companies, shedding light on key features, benefits, and considerations to facilitate operational excellence.
Understanding 3PL Warehouse Management
Definition of 3PL Services
In the dynamic landscape of logistics, Third-Party Logistics or 3PL services are outsourced operational functionalities that cater to supply chain management needs. The essence of 3PL services lies in their ability to provide specialized expertise and resources, allowing companies to focus on their core competencies. Contextualizing 3PL services within the WMS framework is instrumental in streamlining warehouse operations effectively. Despite some limitations, the flexibility and cost-efficiency of 3PL services make them a strategic choice for businesses seeking to optimize logistics operations.
Role of WMS in 3PL
The Role of WMS in 3PL is paramount, serving as the backbone of efficient warehouse management. WMS enables 3PL providers to orchestrate inbound and outbound logistics activities seamlessly, ensuring inventory accuracy and timely order fulfillment. The integration of WMS in 3PL operations empowers companies to leverage technology for improving inventory visibility, tracking, and overall operational efficiency. While challenges such as implementation costs may arise, the benefits of WMS in enhancing 3PL services outweigh the initial hurdles, making it an indispensable tool for modern logistics providers.
Importance of Choosing the Right WMS for 3PL
Enhanced Efficiency
Enhanced Efficiency is a hallmark of a proficient WMS in the 3PL landscape. An optimal WMS system optimizes warehouse processes, minimizes order processing times, and increases productivity. The ability to automate manual tasks, allocate resources effectively, and integrate with other systems exemplifies the significance of enhanced efficiency in driving operational success for 3PL providers. While the initial investment in a robust WMS system may be substantial, the long-term gains in operational efficiency and customer satisfaction justify the cost.
Improved Inventory Management
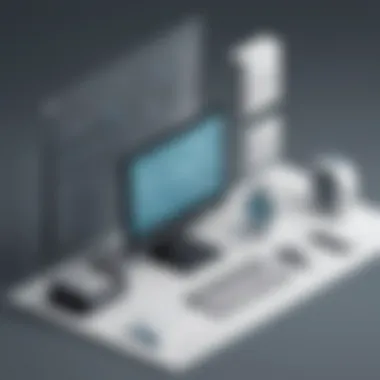
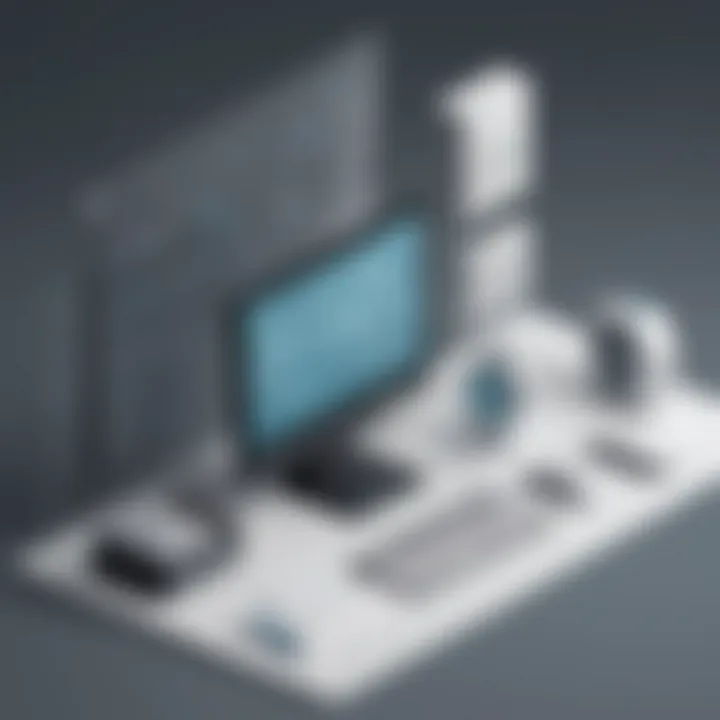
Effective Inventory Management is a critical component of successful 3PL operations, and the right WMS adds unparalleled value in this aspect. The advanced features of WMS, such as real-time inventory tracking, cycle counting, and demand forecasting, aid in maintaining optimal inventory levels and reducing carrying costs. By harnessing the power of technology-driven inventory management, 3PL companies can mitigate stockouts, minimize overstocking, and enhance overall supply chain performance. The seamless integration of WMS with inventory management processes streamlines operations and contributes significantly to business growth.
Real-time Visibility
Real-time Visibility is a game-changer for 3PL providers aiming to elevate customer service levels and operational efficiency. A WMS offering real-time visibility empowers companies to track inventory movements, monitor order statuses, and respond promptly to changing demands. The transparency and agility provided by real-time visibility not only enable quick decision-making but also foster trust and collaboration with clients and partners. Despite potential integration complexities, the benefits of real-time visibility in minimizing stock discrepancies and improving order accuracy position it as a key criterion in selecting the right WMS for 3PL operations.
Key Features to Look for ποΈ
Key features play a crucial role in selecting the best Warehouse Management System (WMS) for Third-Party Logistics (3PL) providers. These features serve as the foundation for optimizing warehouse operations and driving efficiency and productivity. When considering a WMS for 3PL, it is essential to prioritize specific elements that align with the unique requirements of 3PL operations.
Scalability and Flexibility π
Ability to Scale Operations
The ability to scale operations is a key aspect that ensures a WMS can grow in tandem with the expanding needs of a 3PL business. By seamlessly accommodating increasing order volumes and warehouse demands, a scalable WMS enables 3PL providers to adapt to fluctuating market conditions efficiently. The flexibility to adjust resources and workflows enhances operational agility, equipping 3PL companies to meet client expectations swiftly and effectively.
Customization Options
Customization options offer tailor-made solutions to address specific workflow challenges and operational nuances within a 3PL setup. A WMS that provides robust customization features empowers 3PL providers to configure workflows, reports, and processes according to their unique business requirements. This flexibility enhances operational adaptability, enabling 3PL companies to optimize efficiency and client satisfaction by aligning the WMS with their distinct service offerings.
Integration Capabilities π€
Compatibility with Existing Systems
Seamless integration with existing systems is imperative for a WMS to function cohesively within a 3PL ecosystem. Compatibility with diverse software applications and hardware components streamlines data exchange and communication, promoting operational synergies. A WMS that seamlessly integrates with other platforms minimizes silos, enhances data visibility, and streamlines operational processes, driving efficiency and accuracy within 3PL operations.
API Integrations
API integrations enable WMS platforms to connect with third-party applications, allowing for enhanced functionality and expanded capabilities. By integrating with APIs, a WMS can access additional features, data sources, and services that augment operational efficiency and automation. The ability to leverage API integrations strengthens the WMS's versatility and empowers 3PL providers to optimize their workflows, expedite processes, and deliver superior services to clients.
Automation and Robotics Support π€
Robotics Process Automation
Robotics process automation leverages robotics technologies to automate repetitive tasks and streamline warehouse operations. By employing robotic systems for tasks such as picking, packing, and sorting, a WMS can significantly enhance operational speed, accuracy, and throughput. The integration of robotics process automation in a WMS enables 3PL providers to boost productivity, reduce turnaround times, and optimize resource allocation, fostering operational excellence and client satisfaction.
Automated Order Fulfillment
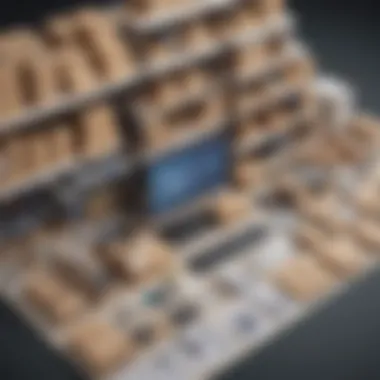
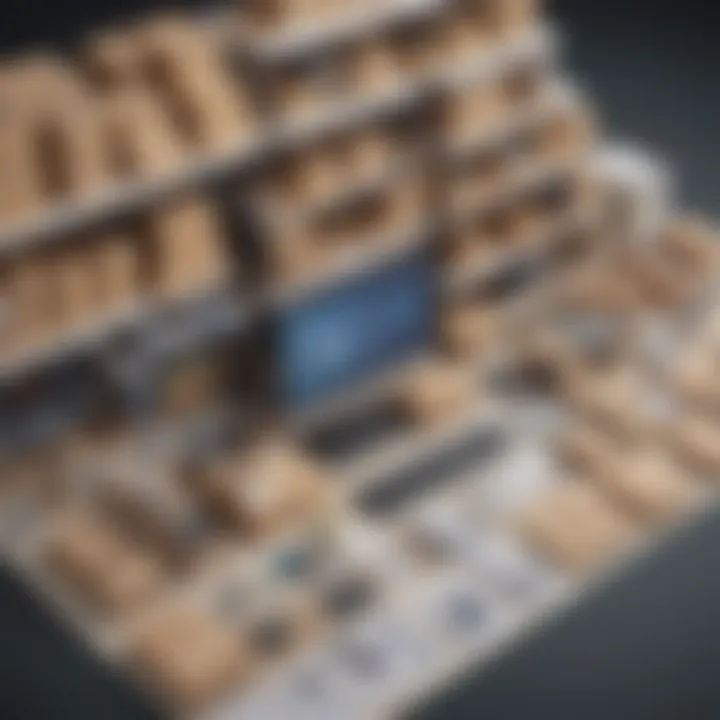
Automated order fulfillment capabilities automate the order processing and fulfillment cycle, optimizing operational efficiency and order accuracy. By automating order picking, sorting, and shipping processes, a WMS can expedite order fulfillment, reduce errors, and enhance order tracking and visibility. Automated order fulfillment features in a WMS empower 3PL providers to streamline order processing, improve customer service levels, and maximize warehouse throughput, driving operational efficiency and client satisfaction.
Benefits of Implementing a Suitable WMS
Implementing a suitable Warehouse Management System (WMS) in a Third-Party Logistics (3PL) setting is crucial for enhancing operational efficiency and optimizing warehouse management processes. By integrating a WMS tailored for 3PL providers, companies can streamline workflows, reduce error rates, and achieve real-time visibility into inventory operations. The benefits of implementing a suitable WMS extend beyond improving efficiency to positively impact customer satisfaction, cost savings, and return on investment.
Improved Operational Efficiency
Streamlined Workflows
Streamlined workflows play a pivotal role in optimizing warehouse operations by automating repetitive tasks, reducing manual handling, and enhancing overall efficiency. The key characteristic of streamlined workflows is the seamless flow of activities from receiving to shipping, ensuring minimal delays and maximizing productivity. This streamlined approach significantly reduces operational bottlenecks, improves order fulfillment speed, and boosts overall warehouse performance. While the unique feature of streamlined workflows may vary based on the WMS solution chosen, the advantages include increased productivity, decreased order processing times, and enhanced order accuracy.
Reduced Error Rates
Reducing error rates is essential in maintaining order accuracy, customer satisfaction, and operational consistency within a 3PL warehouse environment. The key characteristic of mitigating errors lies in implementing quality control measures, barcode scanning technologies, and automated data capture techniques to minimize human errors. By leveraging a WMS that focuses on error reduction, companies can lower return rates, improve inventory accuracy, and build a reputation for reliable order fulfillment. The unique feature of systems targeting reduced error rates is their ability to provide real-time error notifications, implement validation checks, and offer error prevention strategies to enhance operational reliability.
Enhanced Customer Satisfaction
Faster Order Processing
Faster order processing directly impacts customer satisfaction by ensuring quick order fulfillment, timely delivery, and responsiveness to customer demands. The key characteristic of expedited order processing is the ability to prioritize orders, optimize picking routes, and streamline packing processes to meet tight deadlines efficiently. This accelerates order cycle times, improves order accuracy, and strengthens customer loyalty through prompt service. The unique feature of rapid order processing systems is their integration with advanced order management modules, automated order sorting algorithms, and order prioritization functionalities to expedite the fulfillment process further.
Accurate Shipments
Providing accurate shipments is vital for generating trust, repeat business, and positive reviews from customers. The key characteristic of shipping accuracy lies in maintaining precise inventory records, utilizing order verification steps, and employing quality control checks throughout the packaging and shipping stages. By implementing a WMS that prioritizes accurate shipments, businesses can reduce shipping errors, minimize returns due to incorrect orders, and enhance overall customer experience. The unique feature of systems focusing on accurate shipments includes automated weighing systems, packing verification protocols, and real-time shipment tracking to ensure orders are delivered correctly and on time.
Cost Savings and ROI
Optimized Inventory
Optimizing inventory levels is crucial for minimizing carrying costs, reducing stockouts, and maximizing capital utilization within a 3PL warehouse facility. The key characteristic of inventory optimization is maintaining an optimal balance between demand forecasts, reorder points, and safety stock levels to prevent overstocking or understocking scenarios. By implementing a WMS that offers robust inventory management capabilities, businesses can improve inventory turnover rates, prevent excess inventory build-up, and prolong the shelf life of goods stored. The unique feature of inventory optimization tools includes demand forecasting algorithms, inventory level alerts, and inventory cycle counting functionalities to enhance visibility and control over stock levels.
Reduced Labor Costs
Reducing labor costs is a critical component of achieving operational efficiency, cost-effectiveness, and financial sustainability in a 3PL warehouse setting. The key characteristic of labor cost reduction involves optimizing labor allocation, automating manual tasks, and implementing labor tracking mechanisms to maximize workforce productivity. By adopting a WMS that focuses on labor cost reduction, companies can streamline labor-intensive processes, minimize labor redundancies, and allocate human resources more effectively. The unique feature of labor cost reduction systems includes labor performance analytics, workflow automation tools, and labor scheduling functionalities to optimize labor utilization and reduce overall labor expenses.
Factors to Consider Before Selection
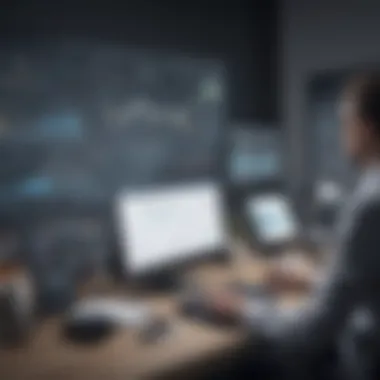
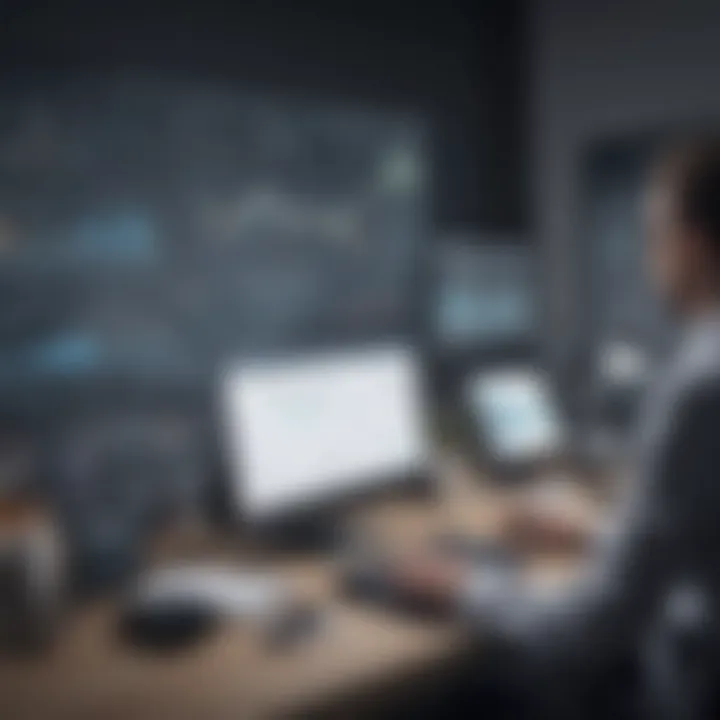
When diving into the world of Warehouse Management Systems (WMS), it becomes crucial to assess various factors before making a selection. The decision-making process in selecting the right WMS for your Third-Party Logistics (3PL) business is a pivotal step that can significantly impact your warehouse operations' efficiency and overall success. Understanding the nitty-gritty details of each factor is imperative to ensure a seamless integration and optimal performance in your logistics processes.
Budget and Affordability
Total Cost of Ownership
One of the primary considerations in choosing a WMS for your 3PL operations is the Total Cost of Ownership. This encompasses not only the initial investment required to implement the system but also factors in long-term costs such as maintenance, upgrades, and training. Calculating the total cost over the system's lifespan is essential to avoid unexpected financial burdens and ensure that the chosen WMS aligns with your budgetary constraints and financial goals. Evaluating the Total Cost of Ownership allows you to make an informed decision that not only fits your current financial capacity but also assures sustainability and profitability in the long run.
Scalability versus Initial Investment
Another critical aspect to weigh when selecting a WMS is the balance between scalability and initial investment. While considering the scalability potential of a system is vital for accommodating future growth and expansion, it is equally important to evaluate the initial investment required. Striking a balance between scalability and initial investment ensures that you choose a WMS that can grow with your business without imposing exorbitant upfront costs. Finding a solution that offers scalability without compromising your financial stability is key in selecting the most suitable WMS for your 3PL operations.
User-Friendliness and Training
Ease of Use
In the realm of WMS selection, the ease of use plays a significant role in determining the system's effectiveness within your logistics environment. An intuitive and user-friendly interface simplifies system navigation, streamlines processes, and enhances user adoption rates among your warehouse staff. Opting for a WMS with a user-centric design not only accelerates the implementation process but also minimizes training overheads and ensures seamless integration into your existing operations. Prioritizing ease of use empowers your team to leverage the system's full potential, driving efficiency and productivity within your 3PL warehouse.
Training and Support Options
Incorporating comprehensive training and support options into your WMS selection criteria is paramount to guarantee a smooth transition and efficient utilization of the system. Robust training programs tailored to your specific operational needs equip your staff with the necessary skills and knowledge to leverage the WMS effectively. Additionally, prompt and responsive support services ensure quick issue resolution and uninterrupted workflow, minimizing downtime and maximizing operational efficiency. Prioritizing vendors that offer extensive training and support enhances your team's proficiency with the WMS, fostering continuous improvement and operational excellence within your 3PL setup.
Vendor Reputation and Support
Customer Reviews
Delving into customer reviews provides valuable insights into the performance, reliability, and user experience of a WMS from a practical standpoint. Analyzing feedback from current users and industry peers offers a holistic perspective on the system's strengths, limitations, and overall utility within 3PL environments. Leveraging customer reviews empowers you to make an informed decision based on real-world experiences and ensures that the chosen WMS aligns with your operational requirements and expectations. Validating vendor claims through authentic customer feedback is instrumental in selecting a WMS that not only meets but exceeds your 3PL warehouse management needs.
Service Level Agreements
The inclusion of robust Service Level Agreements (SLAs) in your selection criteria establishes clear expectations regarding vendor support, system performance, and issue resolution protocols. SLAs outline the vendor's commitments to service quality, response times, and ongoing maintenance, providing a contractual framework for accountability and performance guarantees. Prioritizing vendors with well-defined SLAs safeguards your interests, mitigates risks, and fosters a transparent and mutually beneficial relationship with your chosen WMS provider. Aligning on clear SLAs ensures that your 3PL operations run smoothly, with minimal disruptions and maximum operational efficiency.
Conclusion
Warehouse Management Systems (WMS) play a pivotal role in the optimization of operations for Third-Party Logistics (3PL) providers. In this article, we have delved into the significance of selecting the right WMS for 3PL companies. By understanding the importance of factors such as scalability, integration, and automation in choosing the best WMS, businesses can streamline their workflows, reduce errors, and enhance customer satisfaction. Consideration of budget, user-friendliness, and vendor support are vital in making informed decisions. Implementing a suitable WMS can lead to improved operational efficiency, increased customer satisfaction, and substantial cost savings. Ensuring that the chosen WMS aligns with the specific needs of a 3PL company is crucial for long-term success.
Final Thoughts on WMS for 3PL
Emphasizing Business Needs
Emphasizing the unique requirements and objectives of a 3PL business is paramount in selecting the best WMS. Tailoring the WMS to align with the distinct processes and challenges faced by 3PL providers can lead to enhanced operational performance and customer service. The ability of a WMS to adapt to dynamic business needs, accommodate growth, and maintain flexibility is indispensable for the success of a 3PL operation. Emphasizing business needs ensures that the chosen WMS not only meets current demands but also has the scalability to evolve with the business over time, staying relevant and effective.
Continuous Improvement
Continuous improvement is a core principle that drives efficiency and innovation in the realm of 3PL warehouse management. Opting for a WMS that prioritizes continual enhancement of features, capabilities, and integrations enables 3PL companies to stay ahead of the curve in a competitive market. The iterative development and refinement processes embedded in WMS solutions focused on continuous improvement ensure that businesses benefit from the latest technologies and industry best practices. By embracing this approach, 3PL providers can consistently optimize their warehouse operations, fine-tune processes, and adapt to changing market demands with agility and precision.