Strategies for Enhancing Business Inventory Systems for Optimal Efficiency
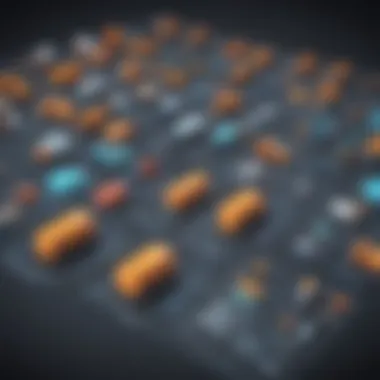

Software Overview
Inventory management software plays a pivotal role in enhancing operational efficiency for businesses. These systems offer a range of features and functionalities, including inventory tracking, demand forecasting, order management, and reporting capabilities. Prices and licensing options for such software vary based on the vendor and the level of customization required. Businesses can choose from a variety of options designed for different scales of operations, ensuring compatibility with various platforms to meet their specific needs.
User Experience
The user experience of inventory management software is a critical component in maximizing its effectiveness. A user-friendly interface design, intuitive navigational tools, and customizable settings contribute to ease of use. Performance and speed are paramount factors, ensuring real-time data accuracy and seamless functionality across different inventory management tasks.
Pros and Cons
Inventory management software comes with distinct strengths and advantages, such as improved inventory control, cost reduction through optimized operations, and enhanced decision-making with real-time insights. However, some drawbacks may include initial training requirements for employees, potential integration complexities with existing systems, and varying levels of technical support. Comparing different software products can help businesses identify the best fit for their specific requirements.
Real-world Applications
The real-world applications of inventory management software span across different industries, including retail, manufacturing, e-commerce, and distribution. Case studies and success stories demonstrate how these software solutions have resolved specific inventory-related challenges, such as minimizing stockouts, improving order accuracy, and streamlining supply chain operations. The customization capabilities of the software enable businesses to tailor solutions to address their unique operational needs.
Updates and Support
Regular software updates ensure that businesses have access to the latest features and security enhancements. Customer support options, including phone, email, and live chat, play a vital role in resolving technical issues and providing training assistance. Community forums and user resources serve as valuable platforms for sharing best practices, troubleshooting common issues, and expanding knowledge on utilizing the software effectively.
Introduction to Business Inventory Systems
In the realm of modern business operations, the efficiency of inventory management systems stands as a pivotal factor in determining success. An Introduction to Business Inventory Systems not only provides a foundational understanding of the processes involved but also offers a strategic roadmap for businesses to navigate the complexities of monitoring and controlling their stock. This section serves as the compass, guiding enterprises towards streamlined operations, cost reductions, and revenue optimization. Whether a company deals with physical goods or digital products, the principles encompassed in Inventory Systems lay the groundwork for sustainable growth and operational excellence.
Importance of Inventory Management
Minimizing Costs
Within the business landscape, the aspect of Minimizing Costs emerges as a cornerstone of effective inventory management. By strategically aligning procurement, storage, and distribution processes, organizations can achieve significant cost savings. The essence of Minimizing Costs lies in its ability to enhance profitability through prudent resource allocation and waste reduction. Embracing cost-efficient practices not only bolsters financial health but also instills a culture of resource consciousness within the organizational fabric. While the advantages of Minimizing Costs are evident in promoting fiscal responsibility, meticulous planning and continuous evaluation are essential to mitigate any potential disadvantages in implementation.
Meeting Customer Demand
Meeting Customer Demand stands as a critical driver in the realm of Inventory Management. Understanding and fulfilling the needs of consumers in a timely and efficient manner are paramount for sustained business success. This aspect accentuates the importance of aligning inventory levels with market trends and consumer preferences. By harmonizing supply chain dynamics with customer demands, organizations can enhance customer satisfaction, brand loyalty, and overall market competitiveness. While the advantages of Meeting Customer Demand are manifest in improved sales volumes and brand reputation, challenges may arise in accurately predicting fluctuating consumer preferences and market demands.
Maximizing Profit Margins
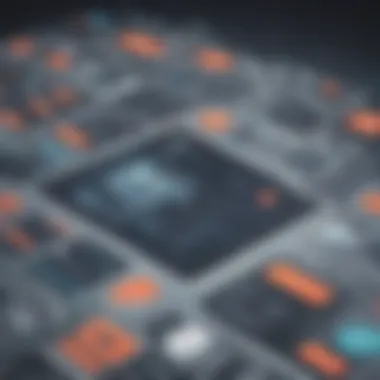

With a sharp focus on profitability, Maximizing Profit Margins emerges as a fundamental objective of inventory optimization. By fine-tuning pricing strategies, controlling inventory carrying costs, and optimizing supply chain efficiency, businesses can elevate their bottom-line performance. The essence of Maximizing Profit Margins lies in leveraging analytical insights and market data to make informed decisions that align with revenue optimization objectives. While the advantages of this approach are clear in enhancing financial returns and competitiveness, careful consideration of market volatility and demand uncertainties is crucial to mitigate potential disadvantages in pursuing aggressive profit maximization strategies.
Core Elements of Inventory Systems
Stock Control
The element of Stock Control is at the core of efficient inventory systems, serving as the fulcrum around which all inventory-related activities revolve. Maintaining optimal stock levels, monitoring inventory turnover rates, and implementing robust stock tracking mechanisms are essential components of effective stock control. The key characteristic of Stock Control lies in its ability to strike a balance between meeting customer demand and minimizing holding costs. By deploying technology-driven stock control solutions, businesses can enhance operational agility, reduce stockouts, and maximize inventory turnover efficiency. While the advantages of Stock Control are clear in promoting inventory accuracy and cost-effectiveness, adherence to best practices and periodic reviews are imperative to address any potential drawbacks.
Tracking and Forecasting
The element of Tracking and Forecasting plays a pivotal role in anticipating market trends, aligning procurement strategies, and optimizing inventory levels. By leveraging data analytics, demand forecasting models, and trend analysis tools, businesses can make informed decisions regarding stocking levels, replenishment cycles, and product launches. The key characteristic of Tracking and Forecasting lies in its predictive capabilities, which enable organizations to proactively respond to changes in customer preferences and market dynamics. Through continuous monitoring and adjustment based on real-time insights, businesses can minimize excess inventory, reduce holding costs, and improve overall supply chain efficiency. While the advantages of Tracking and Forecasting are evident in enhanced demand prediction and inventory optimization, the reliance on historical data and the risk of forecasting errors necessitate a balanced approach towards this core element.
Order Management
Efficient Order Management is crucial for seamless inventory operations, timely order fulfillment, and customer satisfaction. By optimizing order processing workflows, automating order entry systems, and integrating inventory databases with order management platforms, organizations can streamline their supply chain processes and enhance order accuracy. The key characteristic of Order Management lies in its ability to reduce order processing times, minimize errors, and improve inventory visibility. Through the integration of order management software and ERP systems, businesses can achieve real-time order tracking, inventory synchronization, and enhanced customer communication. While the advantages of Order Management are evident in operational efficiency and customer service enhancements, challenges may arise in system integration complexities and the need for continuous process optimization.
Implementing an Efficient Inventory Management System
Implementing an Efficient Inventory Management System is a crucial aspect of optimizing business operations. By focusing on this fundamental step, businesses can enhance productivity, streamline processes, and achieve cost-efficiency. Selecting the right software plays a pivotal role in this implementation process, ensuring seamless operations and effective inventory control. Each element within an inventory management system, from stock control to order management, contributes to the overall efficiency and success of the system.
Selecting the Right Software
Cloud-Based Solutions
Cloud-Based Solutions offer numerous advantages for businesses looking to improve their inventory management systems. One key characteristic of Cloud-Based Solutions is their ability to provide real-time data accessibility from anywhere, facilitating efficient decision-making processes. The scalability of Cloud-Based Solutions allows businesses to adjust their storage needs according to demand, promoting flexibility and cost-effectiveness. Although Cloud-Based Solutions come with inherent cybersecurity risks, the benefits they offer in terms of accessibility and scalability make them a popular choice for modern businesses.
Integration Capabilities
Integration Capabilities are essential for ensuring that different software components seamlessly work together within the inventory management system. The key characteristic of Integration Capabilities is their ability to synchronize data across various platforms, streamlining processes and eliminating data silos. By enabling smooth communication between different software applications, Integration Capabilities enhance operational efficiency and reduce manual errors. While integrating software systems may require initial investment and compatibility checks, the advantage of streamlined processes and enhanced data accuracy makes it a valuable choice for businesses seeking optimized inventory management.
Scalability
Scalability is a critical factor to consider when selecting inventory management software. The key characteristic of Scalability is its capacity to accommodate business growth and fluctuating inventory needs without compromising performance. Scalable software solutions allow businesses to expand their operations seamlessly, adjust inventory levels, and adapt to changing market demands efficiently. The unique feature of Scalability lies in its ability to ensure that the inventory management system can grow alongside the business, without incurring substantial additional costs. While implementing scalable software may require initial customization, the long-term benefits of scalability far outweigh the initial investment, making it a strategic choice for businesses aiming for sustainable growth and operational efficiency.
Automation and Streamlining Processes
Automation and streamlining processes are integral components of an efficient inventory management system. Technologies such as Barcode Scanning play a crucial role in enhancing operational accuracy and inventory tracking. By utilizing Barcode Scanning, businesses can expedite the stock counting process, minimize errors, and improve overall inventory visibility. Real-Time Updates offer businesses instant access to inventory data, enabling timely decision-making and proactive inventory control. Despite the initial setup cost, Real-Time Updates significantly enhance operational efficiency by providing accurate and up-to-date information. Optimized Reordering, on the other hand, automates the replenishment process based on predefined parameters, reducing stockouts and excess inventory levels. The unique feature of Optimized Reordering lies in its ability to optimize inventory levels based on demand patterns, leading to improved cost-efficiency and inventory turnover rates. Implementing automation and streamlining processes not only streamlines operations but also enhances productivity and profitability in the long run.
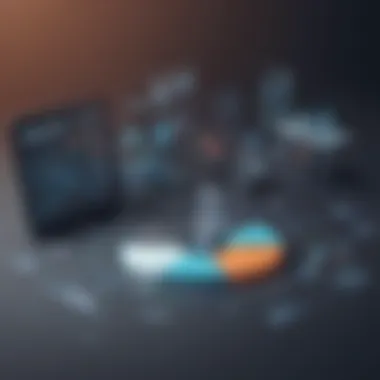

Strategies for Inventory Optimization
ABC Analysis
Categorizing Inventory Items
Categorizing inventory items is a fundamental aspect of the ABC analysis methodology. By categorizing items based on their value and significance to the business, companies can determine the prioritization of resources and efforts. This process involves classifying inventory into categories such as 'A' for high-value items, 'B' for moderate-value items, and 'C' for low-value items. Categorizing inventory items in this manner allows businesses to allocate resources efficiently, ensuring that critical items are given the necessary attention and focus. While categorizing inventory items can enhance decision-making and resource allocation, it may require substantial initial effort to classify items accurately and periodically review categorizations to reflect shifting business dynamics.
Prioritizing Replenishment
In the context of inventory optimization, prioritizing replenishment is essential to maintaining optimal stock levels and meeting customer demand efficiently. By focusing on replenishing high-priority items promptly, businesses can prevent stockouts and streamline their supply chain operations. Prioritizing replenishment involves establishing clear criteria for identifying critical items that require immediate attention, such as fast-moving products or items with limited shelf life. This approach enables businesses to optimize their inventory levels, improve order fulfillment rates, and enhance customer satisfaction. While prioritizing replenishment can boost operational efficiency and profitability, it necessitates continuous monitoring and adjustment based on changing market conditions to ensure optimal outcomes.
Optimizing Stock Levels
Optimizing stock levels is a strategic imperative for businesses looking to strike a balance between inventory costs and service levels. By fine-tuning stock levels based on demand forecasting and consumption patterns, organizations can prevent overstocking or stockouts, thus optimizing their working capital utilization. This process involves setting appropriate reorder points, safety stock levels, and replenishment cycles to align inventory levels with customer requirements and market dynamics. Optimizing stock levels empowers businesses to minimize carrying costs, reduce excess inventory, and enhance overall warehouse efficiency. While optimizing stock levels can drive cost savings and operational improvements, it calls for robust data analytics capabilities and ongoing refinement to adapt to changing business conditions.
Utilizing Data Analytics for Inventory Management
Utilizing data analytics in inventory management is a crucial aspect of optimizing business operations. By harnessing the power of data-driven insights, companies can make informed decisions and improve overall efficiency. Data analytics provides a deeper understanding of inventory trends, customer demands, and market fluctuations, enabling organizations to align their supply chain strategies effectively. Leveraging advanced analytics tools empowers businesses to forecast demand accurately, identify emerging trends, and enhance decision-making processes. Investing in robust data analytics solutions can give businesses a competitive edge by optimizing inventory levels and streamlining operations effectively.
Predictive Analytics
Forecasting Demand
Forecasting demand plays a pivotal role in inventory management, allowing businesses to anticipate market needs and adjust their stock levels accordingly. The ability to forecast demand accurately minimizes excess inventory risks and ensures that products are available to meet customer requirements promptly. By analyzing historical data, market trends, and seasonal patterns, businesses can optimize their inventory planning and maintain a lean supply chain. While forecasting demand requires sophisticated algorithms and statistical models, the benefits of accurate predictions include improved inventory turnover rates and enhanced customer satisfaction.
Identifying Trends
Identifying trends through predictive analytics enables organizations to stay ahead of market shifts and consumer preferences. By tracking key indicators and analyzing data patterns, businesses can proactively adjust their inventory strategies to align with changing demands. Recognizing emerging trends allows companies to capitalize on new opportunities, introduce innovative products, and maintain a competitive edge in the market. However, interpreting trends accurately requires advanced data analysis capabilities and a deep understanding of industry dynamics to make informed decisions and drive strategic growth.
Enhancing Decision-Making
Enhancing decision-making with predictive analytics empowers businesses to make data-driven choices that optimize inventory management processes. By utilizing prescriptive analytics and machine learning algorithms, companies can automate decision-making tasks and identify optimization opportunities proactively. Enhanced decision-making leads to increased operational efficiency, reduced lead times, and improved resource allocation. Furthermore, leveraging predictive analytics for decision-making enhances strategic planning, risk management, and performance optimization, positioning businesses for long-term success in a competitive business landscape.
Performance Monitoring Tools
KPI Tracking
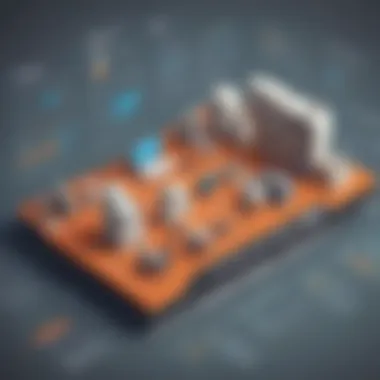

Key Performance Indicator (KPI) tracking is essential for evaluating inventory management performance and measuring success against predefined metrics. By monitoring critical KPIs such as stock turnover rates, order cycle times, and inventory accuracy, businesses can identify areas for improvement and streamline their operations effectively. KPI tracking provides actionable insights that drive continuous performance enhancement and enable informed decision-making to drive operational excellence.
Inventory Turnover Ratios
Inventory turnover ratios gauge the efficiency of inventory management practices by measuring how quickly stock is sold and replaced within a specific period. High inventory turnover ratios indicate effective inventory handling, minimal holding costs, and timely product turnover. By analyzing turnover ratios, businesses can optimize stocking levels, identify slow-moving inventory, and prevent overstocking or stockouts. Maintaining optimal inventory turnover ratios facilitates smoother operations, maximizes cash flow, and improves profitability in the long run.
Service Level Metrics
Service level metrics evaluate the ability of a business to meet customer demands promptly and efficiently. By measuring order fulfillment rates, lead times, and product availability, organizations can assess their service quality and customer satisfaction levels. High service level metrics indicate superior inventory management practices, streamlined order processing, and enhanced customer experiences. Tracking service level metrics allows businesses to identify areas for improvement, implement corrective actions, and enhance overall service reliability and responsiveness.
Ensuring Inventory Security and Compliance
In the realm of business inventory management, ensuring inventory security and compliance is a paramount consideration that contributes significantly to operational efficiency and risk mitigation. With the increasing reliance on digital systems for inventory tracking and management, safeguarding assets and data integrity is crucial to avoid potential losses and disruptions. Security measures such as access controls, encryption protocols, and regular audits help minimize vulnerabilities and ensure compliance with industry standards and regulations.
Risk Management Strategies
Asset Protection
Asset protection plays a vital role in safeguarding a company's valuable resources from various internal and external threats. By implementing robust asset protection strategies, businesses can secure their physical inventory, intellectual property, and financial assets against theft, fraud, and damage. This aspect of risk management focuses on identifying critical assets, determining their worth, and implementing security measures to prevent unauthorized access or misuse.
Fraud Prevention
Fraud prevention measures are essential components of risk management to counter fraudulent activities that could compromise inventory accuracy and financial stability. By implementing fraud detection tools, monitoring transactions, and conducting employee training programs, organizations can mitigate the risks associated with inventory fraud. Preventing fraudulent practices not only safeguards assets but also enhances the overall integrity of inventory data and financial records.
Disaster Recovery Plans
Disaster recovery plans are integral to risk management in business inventory systems as they ensure continuity of operations in the event of unforeseen incidents such as natural disasters, cyber-attacks, or system failures. By developing comprehensive recovery strategies, including data backup procedures, emergency response protocols, and post-incident evaluation processes, companies can minimize downtime and mitigate the impact of disruptions on inventory availability and customer service.
Regulatory Compliance Measures
Regulatory compliance measures are critical for businesses to adhere to industry regulations, standards, and legal requirements in managing inventory operations. Maintaining compliance with inventory audits, data security protocols, and documentation standards is essential for ensuring transparency, accountability, and trust in business practices. By following regulatory guidelines, businesses can mitigate risks associated with non-compliance, legal penalties, and reputational damage.
Inventory Audits
Inventory audits involve systematic inspections and reconciliations of physical inventory with recorded data to verify accuracy, identify discrepancies, and prevent inventory shrinkage or mismanagement. Conducting regular audits helps businesses maintain control over their inventory levels, identify potential risks of stockouts or overstocking, and ensure compliance with accounting practices and regulatory standards.
Data Security Protocols
Data security protocols establish guidelines and procedures for protecting sensitive inventory data from unauthorized access, tampering, or loss. By implementing encryption technologies, access controls, and data backup systems, organizations can safeguard valuable information, maintain data confidentiality, and prevent data breaches or cyber-attacks. Data security protocols are essential for ensuring the integrity and privacy of inventory records and customer information.
Documentation Standards
Documentation standards set forth guidelines for maintaining accurate and comprehensive records of inventory transactions, adjustments, and valuations. Adherence to documentation protocols ensures transparency in inventory management practices, aids in traceability and audit trail capabilities, and facilitates decision-making processes based on real-time insights. Consistent documentation practices help businesses comply with regulatory requirements, facilitate accountability, and enhance operational efficiency.