Mastering EPDM Product Data Management Strategies
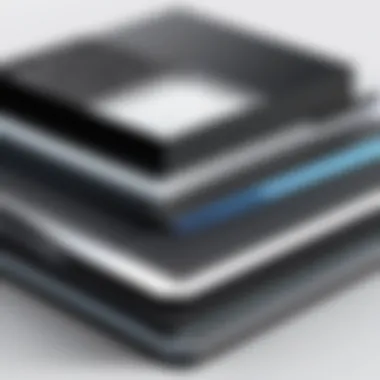

Intro
In todayās fast-paced technological environment, the demand for efficient and reliable product data management systems is becoming ever more critical. Among such systems, EPDMāstanding for Enterprise Product Data Managementāarises as a significant player. This approach helps organizations marshal product data across various stages, from design to production to delivery. More than just keeping records, EPDM plays a crucial role in ensuring product integrity, regulatory compliance, and communication between disparate teams within large manufacturing setups and engineering companies.
As companies cope with increasingly complex projects and stringent timelines, comprehending the underlying mechanics of EPDM becomes essential. With industries spanning sectors such as automotive, aerospace, electronics, and consumer goods, understanding how EPDM can be tailored to fit different organizational needs opens a door for more streamlined operations. This piece aims to shed light on the various dimensions of EPDM, guiding both veterans in the field and those just beginning their journey into product data management.
As we delve deeper, expect insights into the software's features and functionalities, user experiences, a careful evaluation of its strengths and weaknesses, real-world applications showcasing its versatility, and support options available to users. Understanding how EPDM integrates with existing systems and the data governance practices involved will enrich our knowledge base, providing a comprehensive overview of its fundamental role in contemporary software landscapes.
Prolusion to EPDM
In todayās fast-paced digital landscape, understanding EPDM (Enterprise Product Data Management) becomes increasingly crucial for businesses of all sizes. As organizations strive for efficiency and accountability, EPDM serves as a vital framework for managing product data throughout its lifecycle. Without it, countless details can slip through the cracks, leading to inefficiencies and increased costs. The topic of EPDM isnāt just technical jargon; it cuts directly to the core of how products are developed, maintained, and ultimately brought to market.
At the heart of EPDM lies the process of capturing, storing, and managing product-related data in a centralized manner. This centralization allows companies to streamline collaboration between different teamsābe it engineering, manufacturing, or salesāwhile reducing the redundancy that often plagues larger organizations. Understanding EPDM ensures that all employeesāwhether they be engineers creating product drafts, marketers devising launch strategies, or supply chain specialists coordinating logisticsāare singing from the same hymn sheet. This unity can significantly drive productivity.
Key Benefits of EPDM
Some of the clear advantages that EPDM systems offer are:
- Enhanced Collaboration: By providing a single source of truth, EPDM systems reduce miscommunication and promote more robust teamwork.
- Improved Data Accuracy: A centralized platform minimizes the risk of errors that can arise from working in silos or juggling multiple spreadsheets.
- Regulatory Compliance: EPDM helps maintain compliance with industry standards and regulations by keeping all necessary documentation and data readily accessible.
- Faster Time-to-Market: Streamlined workflows within EPDM lead to faster approvals and quicker product development cycles, ultimately getting products into the hands of consumers more rapidly.
As we delve deeper into the intricacies of EPDM, exploring both its past and future, we will begin to uncover why this product data management approach is essential not only for efficiency but also for resiliency within an organization.
Defining EPDM
Understanding EPDM requires us to break down what it signifies. At its core, EPDM encompasses the methods and technologies utilized to manage product-related data. This includes everything from documentation, technical specifications, project files to design changes and market feedback. The information is managed in a systematic way to ensure accuracy and visibility at every stage of the product's lifeāfrom ideation to retirement. The acronym may suggest an overly technical realm, but the reality is more approachable; itās about maintaining control in a constantly evolving environment.
An EPDM solution allows teams to not only access crucial data seamlessly but also to ensure that this data reflects the most current information. Think of it like keeping your garden tidy; when you proactively maintain and organize your tools and plants (data), everything flourishes, and you can focus on cultivating new blooms (innovating new products). This is why defining EPDM is about grasping its essential role in promoting better decision-making, minimizing risk, and driving revenue growth for the business.
Historical Perspective
To understand EPDM as it exists today, it's vital to look back at its evolution. The roots of EPDM can be traced to the early days of product management where companies relied heavily on paper documentation and disconnected databases. These methods were cumbersome and fraught with potential for error.
Fast forward to the late 1990s and early 2000s, with the emergence of the digital age, the demand for more robust data management solutions surged. Companies began adopting software systems that focused exclusively on product data management. The idea was to address the chaos and inflexibility associated with traditional methods. EPDM systems promised a more integrated approach, where product information could be managed consistently across various teams and departments.
With advancements in cloud technology and increasing globalization, EPDM's role has expanded further. Nowadays, the integration of IoT (Internet of Things) and data analytics has also come into play, making EPDM not just a data management tool but a core component of strategic business operations. As we embrace newer technologies, understanding EPDM's history helps define its future trajectory and necessity in modern-day businesses.
"The better your data is managed, the further ahead you stand in todayās competitive marketplace."
In summary, knowing how EPDM began and how it has transformed sets the stage for exploring its significance, challenges, and the methodology behind implementing these systems effectively. The next logical step in this discussion will focus on the significance of product data management within the overall product lifecycle.
Significance of Product Data Management
Product Data Management (PDM) stands as a cornerstone in the development and lifecycle of products, particularly within the context of Engineering Product Data Management (EPDM). At the heart of its importance lies the task of systematically organizing and controlling product information. Effective management of this data enables companies to streamline processes, ensure compliance, and foster innovation.
The significance of PDM is multi-faceted, particularly across industries where time-to-market and resource management are critical. One primary benefit is the facilitation of collaboration across various teamsāfrom design to production. When everyone is on the same page, moving the project forward becomes more straightforward and efficient. The smoother the flow of information, the less likely it is to encounter miscommunications, which can lead to costly delays.
A notable aspect of PDM is its role in the product lifecycle. By implementing robust data management practices right from the initial concept phase through to retirement, companies can enhance not only the quality of the product but also its market adaptability. Efficient product data management ensures that all involved parties have immediate access to up-to-date information, which serves as a critical factor in decision-making processes. It allows organizations to respond to market changes with agility, adapting their strategies based on the most current insights.
Role in Product Lifecycle
The product lifecycle is a constant cycle that includes several phases: conception, design, development, production, distribution, and eventual retirement. Understanding how PDM fits into each of these stages is vital. During the conception stage, PDM helps encapsulate initial ideas, concepts, and requirements that serve as the framework for future development.
As a product transitions to the design and development phases, PDM becomes essential in managing revisions, coordinating files, and ensuring that all team members can access the latest updates. The importance here cannot be overstated. When engineers use outdated designs or specifications, the repercussions can be significant, ranging from rework to financial losses. Additionally, PDM tools track changes systematically, allowing a clear record of decisions made throughout the design process.
Moreover, in the production phase, PDM ensures that the necessary documentation and data are readily available for manufacturing. This accessibility reduces the risks of errors and inefficiencies that could mar the final output. As products reach the distribution stage, PDM systems can improve logistics and inventory management, ensuring the rapid and reliable delivery of products to market.
Overall, PDM functions as the backbone throughout the product lifecycle, offering organizations a clear path to manage complexity.
Impact on Efficiency and Collaboration
Efficiency is the lifeblood of any successful operation. With the integration of a well-structured PDM system, businesses can enjoy a reduction in redundant tasks and optimize their workflows. For instance, a solid EPDM strategy can help cut down on the time spent searching for data or files. Teams can focus their energies where it matters most, rather than getting bogged down in administrative overhead.
Collaboration is another pivotal benefit that emerges from well-handled product data. When various departments have easy access to product information, collaboration flourishes. Projects benefit from diverse perspectives as engineers, marketers, and supply-chain managers share insights and track progress.
"Good communication is as stimulating as black coffee, and just as hard to sleep after." ā Anonymous
In environments where teams are distributedāwhether across cities or even globallyāPDM facilitates real-time collaboration through cloud-based solutions. This immediacy fosters innovation and creativity. Team members can contribute to designs, provide feedback, or flag issues as they arise.
Furthermore, efficiency extends beyond merely keeping teams aligned. It includes minimizing delays caused by miscommunication or lack of information. When everyone has the tools they need, companies gain a competitive edge by delivering products faster, while maintaining high quality.
In summary, the significance of Product Data Management within EPDM is profound. It serves as a linchpin that not only supports the product lifecycle but also boosts efficiency and nurtures collaborative efforts across teams, setting a robust foundation for organizational success.
Core Components of EPDM Systems
Data Storage Solutions
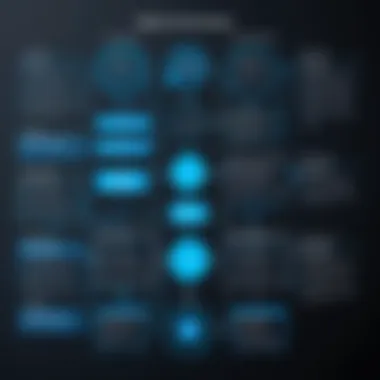
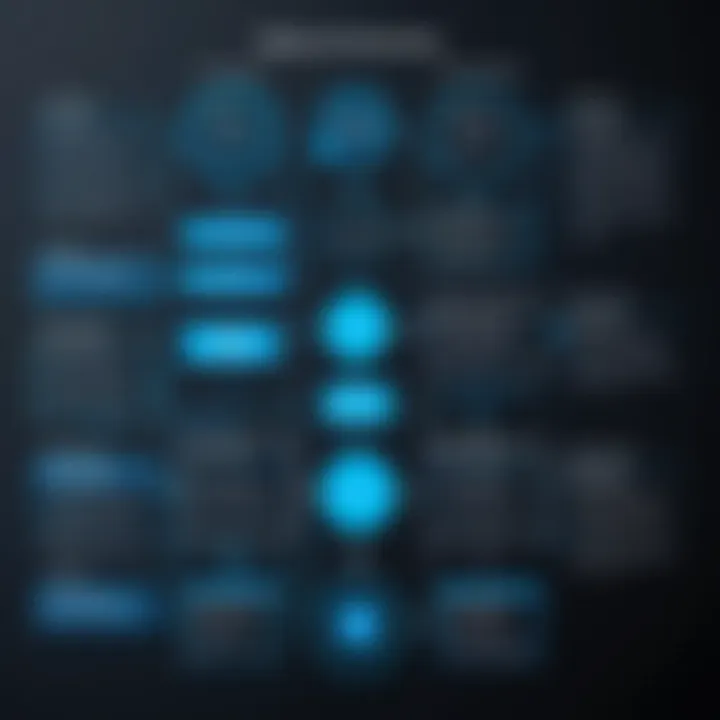
Data storage solutions play a pivotal role in any EPDM system. Efficient storage is not just about keeping data safe; itās about ensuring easy access and retrieval when needed. A well-designed storage system can facilitate faster decision-making by providing stakeholders instantaneous access to accurate information.
To achieve this, organizations typically opt for a combination of on-premises and cloud-based storage solutions. The choice depends on factors such as data security needs, budget constraints, and accessibility requirements. For example, larger enterprises might lean towards private cloud options, whereas smaller companies could benefit from public cloud offerings to save costs.
Considerations include:
- Scalability: As project needs grow, storage needs can change. A flexible storage solution can adapt to these changing demands.
- Accessibility: Stakeholders should have the ability to access data from remote locations. Cloud solutions often provide better access.
- Backup & Recovery: Making sure that data is backed up regularly can save an organization from potential disasters.
Workflow Management Tools
Workflow management tools are essential for orchestrating the various processes that take place in EPDM systems. Without these tools, managing tasks, approvals, and revisions can become a chaotic affair, leading to delays and errors. These tools permit organizations to visualize the flow of work, assign tasks, and track progress in real-time.
For effective management, tools should provide:
- Customizable workflows: Each team has its way of doing things. Allowing customization can enhance user experience.
- Real-time tracking: Monitoring the progress of tasks can help identify bottlenecks and optimize flow.
- Collaboration features: Tools should enable communication among team members to facilitate fast decision-making.
Using platforms like Asana or Trello can make a noticeable difference in maintaining organized workflows and boosting team productivity. Integrating these tools with EPDM systems can yield significant benefits in terms of efficiency and accountability.
Version Control Mechanisms
Version control mechanisms are like the safety net of EPDM product data management. Having a robust version control system ensures that every change is tracked and documented, which helps maintain the integrity of products.
When multiple people work on projects, itās easy for confusion and errors to arise. A solid version control system addresses this by:
- Tracking Changes: Each new version comes with its own details, ensuring that stakeholders know what was changed and why.
- Offering Rollback Options: If a new version causes issues, teams can revert to previous versions quickly without losing any work.
- Facilitating Collaboration: Developers and designers can work together seamlessly, merging different versions without hassle.
With tools such as Git and SVN, teams can manage their code efficiently, ensuring that the right version is always available for use. This not only preserves data integrity but also speeds up project timelines.
"In an age where time is money, having the right tools to manage your data can make all the difference in productivity and quality."
By investing in these core componentsādata storage solutions, workflow management tools, and version control mechanismsāorganizations can set themselves up for success in their EPDM strategies, driving better outcomes across the board.
Methodologies in EPDM Implementation
When diving into EPDM product data management, the choice of methodology plays a crucial role in determining how effectively an organization can implement and leverage these systems. Methodologies guide the entire process from inception to execution, directly impacting efficiency, user acceptance, and overall success. Understanding various methodologies not only helps in making informed decisions but also in adjusting strategies to suit specific business needs. Moreover, different industries may have unique requirements, making the adaptability of these methodologies a significant consideration.
In essence, the right methodology ensures that an EPDM system aligns closely with organizational objectives and integrates seamlessly within existing workflows.
Agile Implementation Practices
Agile methodology is like a breath of fresh air in a world often bogged down by rigid processes. It emphasizes iterative progress, flexibility, and collaborative effort, which can be a game changer when deploying EPDM systems. In contrast to traditional methods that follow a strict sequence, Agile invites teams to engage in short cycles, fostering quicker adaptation based on feedback and changing conditions.
By working in sprints, teams can deliver functional components early and refine them through continuous feedback. This approach encourages involvement from different stakeholders, ensuring that their insights shape the evolution of the system. Some key characteristics of Agile practices in EPDM include:
- Adaptability: Teams can easily make adjustments based on user feedback or shifts in project requirements.
- Collaborative Environment: Agile emphasizes teamwork, which can enhance communication between departments and improve overall morale.
- Early Value Delivery: Functional components that are deployed early allow organizations to start reaping the benefits much sooner.
"Using Agile in EPDM fosters a sense of ownership among users, turning them from passive recipients to active contributors."
However, Agile does require a culture that embraces change. Resistance to altering long-standing workflows can present challenges, necessitating the involvement of change champions within the organization to facilitate a smoother transition.
Waterfall Models in EPDM
On the flip side of the Agile approach lies the Waterfall model, which adheres to a sequential design process. This method is often likened to a well-planned journey, where each phase must be completed before moving on to the next. This structured methodology can be advantageous when the requirements are clear and unlikely to evolve significantly during the implementation phase.
Waterfall models can lend themselves well to EPDM where strict compliance, documentation, and a predictable outcome are required. Here are several aspects to consider:
- Clarity: Each step in the Waterfall model provides a clear framework, making it easier to define project scope and timelines.
- Documentation: Comprehensive documentation at every stage can prevent miscommunication and ensure that all stakeholders are on the same page.
- Reduced Complexity: With the focus on sequential phases, it minimizes the chaos that sometimes accompanies more fluid methodologies.
However, one of the downfalls of this approach is that it can be less adaptable to changes. If a requirement shifts late in the process, it can lead to significant delays or additional costs. Hence, organizations often weigh the predictability of Waterfall against the flexibility of Agile, contemplating which methodology aligns best with their operational philosophy and business needs.
Challenges in EPDM Strategy
Navigating the world of EPDM product data management is no walk in the park. The complexities involved can present numerous obstacles, and identifying them is crucial for both small companies and large enterprises. Addressing these challenges not only boosts efficiency but also enhances the effectiveness of the overall product data management strategy.
Two primary challenges often surface in this realm: data integrity issues and user adoption resistance. Tackling these elements head-on can make a world of difference for organizations striving to implement EPDM systems successfully.
Data Integrity Issues
Data integrity is the backbone of any EPDM system. It embodies the accuracy and consistency of data throughout its lifecycle. Unfortunately, maintaining this integrity can often be likened to herding cats; numerous factors can disrupt it. Miscommunication between departments, manual data entry errors, and obsolete data may all contribute to an unreliable data environment.
Several factors can exacerbate data integrity issues:
- Manual Input Errors: When team members enter data by hand, the potential for mistakes increases significantly.
- Incompatible Systems: Different software systems might not communicate well, leading toformat discrepancies.
- Lack of Standard Procedures: Without clear guidelines or procedures, it becomes easy for data inconsistencies to go unaddressed.
If organizations arenāt vigilant, the consequences can be dire. Poor data integrity skews reports, leads to faulty decision-making, and can diminish trust in the data from users. Companies need a solid strategy in place to ensure that data is accurate, secured, and accessible without complication. For instance, investing in automated data validation tools can go a long way in preserving integrity.
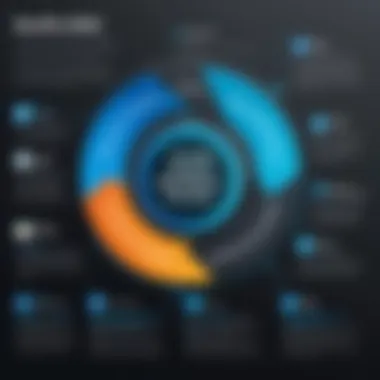
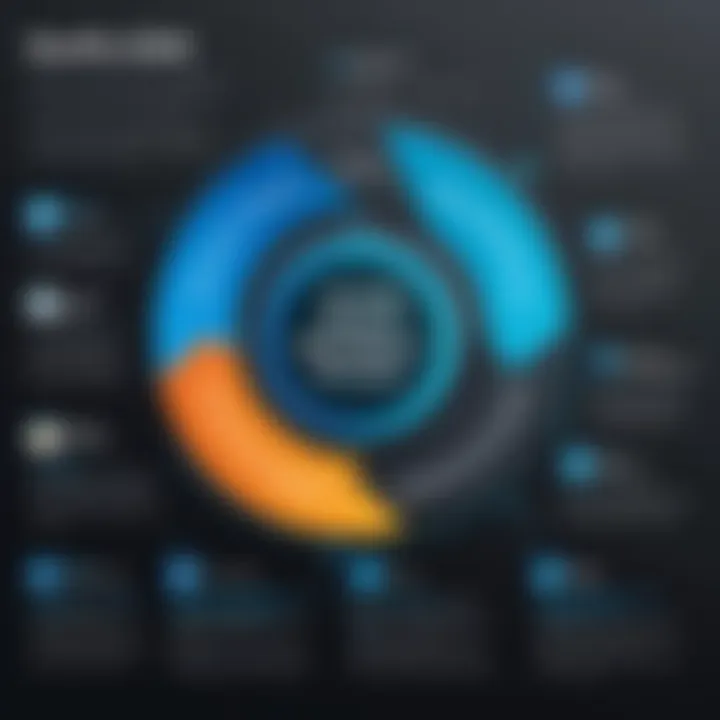
"Good data management is not just about technology; itās about creating a culture of data reliability."
User Adoption Resistance
Even the most superbly designed EPDM system can flop if end-users are not on board. User adoption resistance is a pervasive issue that can thwart implementation efforts. People are naturally inclined to stick to familiar processes, even if they are inefficient. Therefore, organizations must tread lightly when introducing a new EPDM platform.
Common reasons for user adoption resistance include:
- Fear of Change: Employees may feel daunted by new processes and workflows, often leading to apprehension.
- Insufficient Training: Without proper training, users may feel lost, which inevitably leads to frustration and abandonment.
- Inadequate Feedback Channels: If users canāt voice concerns or suggestions, they'll likely disengage.
To combat these challenges, clear communication and extensive training programs are crucial. Engaging team members in the transition, including them in discussions about process changes, can foster a more positive attitude. Providing resources and ongoing support can also help ease the transition. A fine-tuned approach to managing user involvement will lead to a smoother adoption and improve system effectiveness.
In summary, taking the time to understand these challenges, from data integrity to user adoption, is essential in crafting a robust EPDM strategy. Organizations that prioritize these aspects are setting themselves up for success in a complex landscape.
Governance in Data Management
Effective governance is the rudder that steers any data management initiative in the right direction, particularly when discussing EPDM (Enterprise Product Data Management) systems. Establishing robust governance ensures that data remains accurate, accessible, and secure. This governance framework plays a vital role in setting standards, policies, and procedures that govern how data is created, stored, accessed, and managed throughout its lifecycle.
The importance of governance in data management extends beyond just compliance or risk avoidance. It fundamentally impacts business performance. When governance frameworks are in place, organizations can reduce redundancy, enhance data quality, and promote data-driven decision-making. Ultimately, the goal is to create a culture that values information as a vital asset. This isn't just about having policies; it's about instilling a mindset where everyone in the organization understands the significance of their role in preserving data integrity.
Benefits of Strong Data Governance:
- Improved Data Quality: Clear standards lead to consistent data across the organization.
- Risk Mitigation: Proper governance minimizes risks related to non-compliance and data breaches.
- Enhanced Decision-Making: Reliable data supports strategic decisions, aligning with business themes.
- Increased Efficiency: Streamlined processes reduce the time employees spend managing data.
In the realm of EPDM, governance also affects collaboration among teams. When rules are clear and roles well-defined, it fosters a more collaborative environment, allowing teams to share and utilize data efficiently.
"Good governance enhances trust among stakeholders by ensuring they have confidence in the data handled by the organization."
In the coming sections, we will explore how to create effective governance frameworks and delve into vital aspects, such as risk management considerations that accompany these practices.
Establishing Governance Frameworks
To build a robust governance framework for EPDM, it starts with defining who is responsible for what. It's all about laying down the groundwork so that everyone knows their part in the grand data management symphony. Often referred to as a RACI matrix (Responsible, Accountable, Consulted, and Informed), this tool helps to clarify roles and align expectations across the organization.
Once you establish the roles, policies must be drafted. These should include:
- Data Classification Policies: Categorizing data based on sensitivity and importance helps tailor the governing rules accordingly.
- Access Control Measures: Implementing role-based access keeps sensitive data secure while allowing necessary sharing across teams.
- Data Quality Standards: Setting benchmarks for data entry, updates, and reviews ensures data remains credible.
Implementing such a framework isn't just about compliance; it adds a layer of accountability and encourages employees to adhere to practices that may seem mundane but are critical in the long run. The governance approach also requires tailoring to the specific needs of your organization, adapting to the existing corporate culture and IT infrastructure.
Risk Management Considerations
In any governance strategy, risk management is paramount. Why? Well, without assessing potential risks, organizations may find themselves in murky waters. In the context of EPDM, risks could range from incomplete data leading to faulty product designs to malicious attacks targeting critical data assets.
Consider having regular audits as part of your risk management strategy. Whether through third-party assessments or internal reviews, audits provide insights into potential vulnerabilities and compliance lapses. Some risks to keep an eye on include:
- Data Breaches: Organizations must remain vigilant against hackers or insider threats.
- Compliance Failures: Regulations are ever-evolving; keeping up to date is essential to avoid hefty fines.
- Inaccurate Data: A lack of clear data quality measures could lead to significant operational issues.
Organizations can mitigate these risks by implementing a risk assessment framework that regularly evaluates threats. Staff training on data privacy and cybersecurity practices can also fortify your defenses.
In summary, having effective governance frameworks and risk management protocols adds layers of protection and support for your EPDM systems. Not only do they help underline the significance of data integrity, but they also enhance overall organizational resilience.
Together, these strategies allow businesses to navigate the complexities of data management gracefully and effectively.
Integration with Existing Systems
Integration with existing systems is a cornerstone for successful EPDM product data management. In a rapidly changing landscape, companies often find themselves juggling various software applications that have been acquired over time, each serving its own purpose. Failure to integrate these systems not only leads to inefficiencies but hampers data accessibility and productivity. Therefore, establishing a cohesive connection between EPDM systems and other software tools is paramount.
Interoperability Challenges
One of the most significant hurdles in achieving seamless integration is interoperability. This term refers to the ability of different systems or software applications to work together without encountering barriers. When disparate systems fail to communicate properly, it often results in data silos. Consequently, data that resides in one application may be inaccessible or underutilized in another.
Key challenges include:
- Data Format Diversions: Each system tends to use its own data format. When attempting to transfer information between systems, conversion becomes necessary, which can introduce errors.
- Legacy Systems: Older systems might lack modern APIs, making it hard to integrate with new software solutions. Upgrading these systems can be cost-prohibitive, leading companies to stick with dated technology out of necessity.
- Vendor Lock-in: Often, businesses find themselves locked into a particular vendor, which limits their flexibility to include other systems or technologies.
Overcoming these challenges requires a thorough understanding of both the existing technologies and the desired EPDM functionalities. Companies may need to invest in middleware solutions or adopt open standards that facilitate smoother communication between platforms.
APIs and Data Exchange Protocols
Application Programming Interfaces (APIs) play a crucial role in uniting various systems. They serve as bridges that allow different platforms to communicate effectively, enabling data exchange and process automation. This is especially relevant in any EPDM strategy, as accessing product data in real-time has become a necessity.
When considering APIs and data exchange protocols, several factors come into play:
- Standard APIs: Utilization of standardized APIs ensures a level of consistency in how data is accessed and shared. This reduces the friction that often accompanies data interchange between systems.
- REST and SOAP: Different types of APIs, such as REST (Representational State Transfer) or SOAP (Simple Object Access Protocol), cater to various integration requirements. Each has its strengths and use cases, and understanding how and when to employ them is essential for effective implementation.
- Security Protocols: As integration occurs, it's vital to consider the security implications. Proper authentication and data encryption should be utilized to mitigate the risks of data breaches.
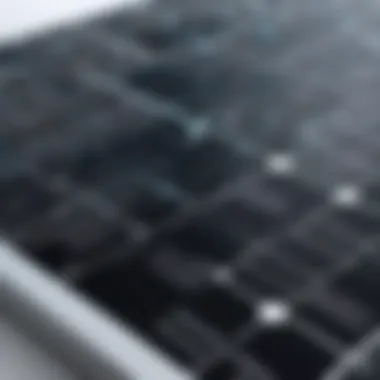
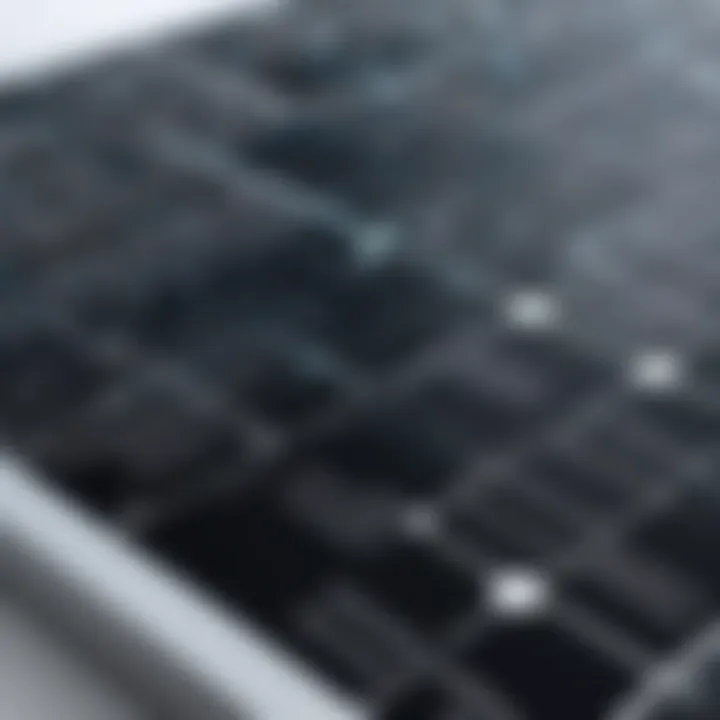
By harnessing the power of APIs and robust data exchange protocols, organizations can create a more connected ecosystem, enhancing the overall effectiveness of their EPDM efforts. Ultimately, successful integration translates not just into efficiency, but also into a competitive advantage in the market.
"Successful integration is not simply a technical challenge; it is a strategic imperative that impacts collaboration, efficiency, and innovation across the organization."
In summary, integration with existing systems is critical for effective EPDM management. Addressing interoperability challenges and leveraging APIs can significantly improve the user experience and optimize workflows, ultimately leading to more informed decision-making and better product outcomes.
Emerging Trends in EPDM
In the fast-paced world of software and product data management, keeping up with emerging trends is crucial for any organization reliant on EPDM (Enterprise Product Data Management). This area is evolving rapidly, influenced by technological advancements and changing business needs. Failing to adapt can mean missing out on significant efficiencies, innovations, and competitive advantages. It is essential to remain agile and consider new methodologies that promise to enhance productivity and collaboration.
Artificial Intelligence and Machine Learning Applications
AI and machine learning are set to revolutionize how EPDM systems operate. Organizations are beginning to integrate these technologies into their product data management processes to extract valuable insights from data automatically. Through these applications, tasks that once required substantial manual input can be streamlined or even fully automated.
- Predictive Analytics: AI algorithms can analyze past data patterns to forecast future product performance. This predictive capability assists teams in making informed decisions about design alterations or product lifecycle management.
- Enhanced Data Quality: Machine learning algorithms help in identifying anomalies and inconsistencies in data sets. This can prevent errors from propagating through the system, ensuring that product data remains reliable.
- Intelligent Workflows: AI can optimize workflows by prioritizing tasks based on urgency or significance. This improves response time and allows team members to focus on high-impact activities.
Moreover, as AI continues to mature, we might see an increase in fully autonomous decision-making processes within EPDM systems, enabling them to not only store and manage data but also to make critical operational decisions without human intervention. The integration of such technologies could lead to more streamlined operations and possibly lower overhead costs.
Cloud-Based Solutions
The shift towards cloud-based solutions encompasses a broad movement favoring flexibility and scalability in EPDM. Many organizations are moving away from on-premises systems to cloud environments to enjoy benefits that traditional setups cannot offer.
- Scalability and Flexibility: Cloud solutions allow companies to scale their data management resources up or down based on demand. This means you only pay for what you need, helping businesses align costs with their actual usage.
- Accessibility: With cloud-based EPDM systems, team members can access critical data from anywhere. This remote access is not just convenient; it supports collaboration among distributed teams.
- Automatic Updates and Maintenance: Providers often manage updates and maintenance, which mitigates the headache of handling software version control and minimizes disruption during upgrades.
- Enhanced Data Security: Many cloud solutions come with robust security features, ensuring data is encrypted and stored in secure environments, thus reducing the risk of data breaches that can arise from local storage.
Integrating cloud-based EPDM systems can drive innovation in products and ultimately help organizations remain competitive in their industries.
"Embracing the cloud is no longer a question of if but when for modern enterprises dedicated to adapting and thriving in a dynamic marketplace."
Case Studies
In the realm of EPDM product data management, understanding real-world applications is paramount. Case studies serve not just as dry accounts of what has occurred in various organizations but as rich narratives illustrating the nuances, strategies, and outcomes related to EPDM implementations. Analyzing these examples allows professionals to glean insights into best practices, potential pitfalls, and the overall effectiveness of different methodologies. They marry theory with practice, often elucidating complex concepts in a digestible way.
Successful EPDM Implementations
Successful implementations of EPDM often reflect a careful alignment between the technology and the specific needs of the business. Take, for instance, a leading automotive manufacturer that adopted EPDM to streamline their design processes. By leveraging an integrated EPDM system, the company could centralize product data and reduce duplication errors. This not only saved time but significantly enhanced collaboration among design, engineering, and manufacturing teams.
Key elements observed in successful cases include:
- Pre-Implementation Analysis: Thoroughly understanding the existing workflows before adopting EPDM provides clarity on what changes should be made.
- Stakeholder Engagement: Involving all relevant parties early in the process fosters buy-in and helps cater the system to the end-users' needs.
- Iterative Testing and Feedback: Successful projects often implement a robust feedback mechanism. Regular iterations based on user input can weed out issues early on.
For instance, another company within the electronics sector noted a dramatic improvement in their product release timelines. By automating data workflows with EPDM, they achieved a significant reduction in time spent on product development. The success primarily stemmed from a commitment to continual training and open communication among all teams involved.
Lessons from EPDM Failures
Not all EPDM initiatives hit the ground running; learning from failures can be as enlightening as celebrating successes. A case involving a large consumer goods provider highlights the risks of neglecting cultural adaptation alongside technological changes. The company implemented an EPDM system without adequately preparing its workforce, resulting in user resistance and eventual abandonment of the system. Despite the investment made, the lack of training left employees feeling overwhelmed and alienated.
Key takeaways from failed implementations include:
- Inadequate User Training: Failure to invest in sufficient training often leads to poor adoption rates. Users may resist new systems if they perceive them as complex or unnecessary.
- Lack of Clear Objectives: Not defining what success looks like can sink an EPDM effort. Set measurable goals that give direction throughout the implementation process.
- Overcomplicating Processes: Sometimes, EPDM tools are capable of much more than necessary. Overloading a system with features can distract from its core benefits. Focus on essential tools that drive productivity effectively.
A technology startup attempted to integrate EPDM into its workflow but faced challenges due to competing priorities within teams. Departments did not collaborate effectively, leading to significant inefficiencies and ultimately, the abandonment of the EPDM system. Reflecting on this experience led them to adopt a more cross-functional approach in future projects.
"Case studies not only spotlight asset management triumphs but also illuminate the missteps to steer clear of in future endeavors."
By delving into both the successes and failings of EPDM implementations, industry professionals can draw valuable lessonsāa realistic view of the landscape that celebrates achievements while remaining mindful of pitfalls. Understanding these narratives can assist in crafting customized strategies that enhance productivity and cooperation across teams.
Future Directions for EPDM
The landscape of EPDM is shifting and evolving, bringing with it a multitude of opportunities and challenges. As businesses strive to stay competitive, the focus on future directions in EPDM becomes not just relevant, but essential. This section delves into the innovations that are on the horizon, along with predicted market trends that could reshape how organizations manage product data. A clear grasp of these elements contributes not only to strategic planning but also to the overall growth in capabilities that EPDM offers.
Innovations on the Horizon
Innovation in EPDM is likely to center around increased automation and integration of advanced technologies. In particular, Artificial Intelligence (AI) and Machine Learning (ML) tools are expected to revolutionize how data is processed and analyzed, providing insights that were previously unattainable. Imagine having an EPDM system that can predict potential data inconsistencies before they become problematic, or one that can suggest optimizations based on historical usage trends.
Another exciting area is the development of cloud-native EPDM solutions. These platforms promise enhanced scalability and flexibility, allowing businesses of all sizes to adapt to changing needs. Being able to access product data in real-time can improve decision-making processes significantly. Moreover, with improved data security measures in cloud computing, organizations can trust that their vital information is well protected.
- Ubiquity of Cloud Solutions: Businesses will find that more EPDM vendors will adopt cloud technologies.
- AI Integration: Enhanced predictive analytics will provide better insights into product development and management.
This constant evolution paves the way for tools that not only enhance efficiency but also support collaboration across different teams and functions. Ultimately, the innovations being developed in EPDM are set to yield substantial benefits.
Predicted Market Trends
As we look ahead, the EPDM market is poised to experience notable shifts. One major trend anticipated is the increased demand for user-friendly interfaces. With software becoming more complex, users are seeking solutions that present information in intuitive ways. This aligns with broader trends in software development where user experience (UX) plays a crucial role in product adoption.
Moreover, a growing emphasis on sustainability and eco-friendliness in product data management is on the radar. Companies are not only expected to streamline processes but also demonstrate social responsibility. As such, EPDM solutions that incorporate sustainability metrics will likely gain traction, offering organizations a way to align their product management capabilities with their corporate values.
"Future advancements in EPDM will not just enhance efficiency; they will redefine the way teams collaborate and make decisions."
An additional predicted trend is the rise of mobile platforms for EPDM access. As remote work continues to be a norm, professionals will need solutions that enable them to manage product data from anywhere, at any time.
- User-Centric Design: EPDM software is shifting towards providing intuitive, ease-of-use interfaces.
- Sustainability Metrics: Expect a growing demand for tools that help track environmental responsibility.
- Mobile Accessibility: Solutions that cater to mobile platforms will likely be in greater demand.
In summary, the future directions for EPDM are painted with possibilities that extend beyond current limitations. By keeping an eye on these innovations and trends, businesses can position themselves favorably to harness the full potential of product data management.