Unraveling the Intricacies of the Finite Element Method in Engineering
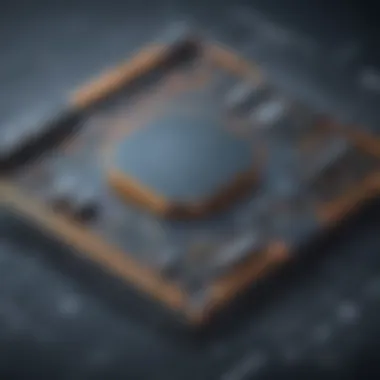
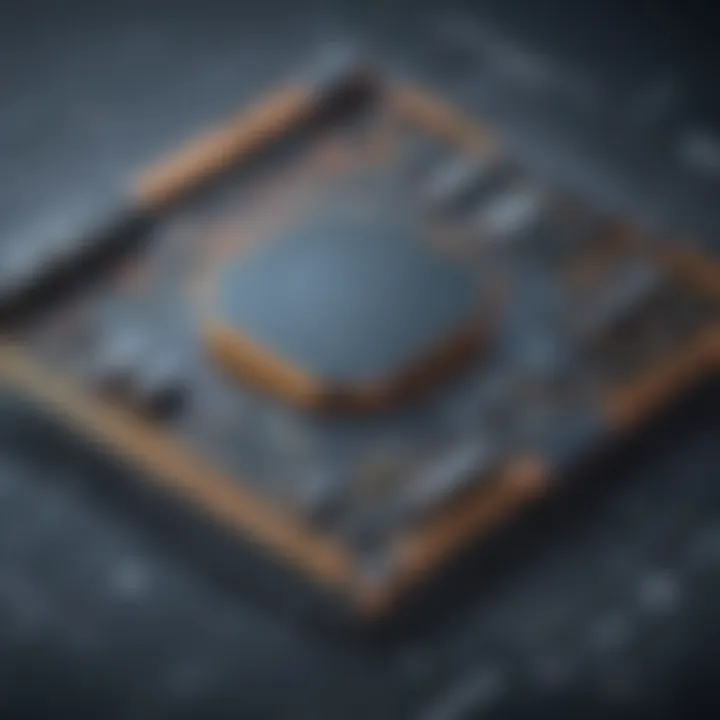
Software Overview
When delving into the Finite Element Method (FEM) in engineering, it is essential to grasp the software landscape that enables its implementation. The software utilized for FEM offers a multitude of features and functionalities that streamline the numerical analysis process. These tools are designed to cater to the intricate demands of engineering simulations, providing a robust platform for engineers and scientists to model complex structures and systems. In terms of pricing and licensing options, this software typically offers various packages tailored to different user needs. From single-user licenses to enterprise solutions, the pricing structure allows for scalability and customization based on the organization's requirements. Moreover, the software is compatible with a wide range of platforms, ensuring accessibility across different operating systems and devices.
User Experience
One of the key factors influencing the adoption of FEM software is the user experience it offers. The ease of use and intuitive interface design are crucial components that enhance productivity and efficiency in engineering workflows. Engineers and software professionals rely on these tools to deliver seamless performance, allowing them to focus on the intricacies of their simulations rather than grappling with complex software functionalities. Customizability and user settings further amplify the user experience, enabling individuals to tailor the software to their specific preferences and requirements. Additionally, the performance and speed of the software are paramount, especially when dealing with large-scale simulations and analysis tasks.
Pros and Cons
Exploring the strengths and advantages of FEM software sheds light on its transformative capabilities in engineering applications. From accurate stress analysis to structural optimization, these tools empower engineers to expedite the design and testing processes with precision and reliability. However, like any software, FEM tools come with certain drawbacks and limitations that users need to consider. Understanding these aspects is critical for making informed decisions regarding software selection and implementation. A comparative analysis with similar products in the market provides valuable insights into the unique selling propositions of different FEM software solutions.
Real-world Applications
The real-world applications of FEM software span various industries, from aerospace and automotive to civil engineering and biomechanics. Through compelling case studies and success stories, professionals can witness the impactful role of FEM in solving complex engineering challenges. These stories exemplify how the software drives innovation, enhances productivity, and supports sustainable design practices across different sectors. By examining industry-specific use cases, users gain a deeper appreciation for the versatility and efficacy of FEM software in addressing diverse engineering requirements.
Updates and Support
Staying abreast of software updates is crucial for leveraging the latest features and enhancements offered by FEM tools. The frequency of updates varies among different software providers, with some offering regular updates to address user feedback and technological advancements. Customer support options play a vital role in assisting users with technical queries, troubleshooting issues, and maximizing the software's potential. Community forums and user resources serve as valuable knowledge-sharing platforms where professionals can exchange insights, best practices, and tips for optimizing their FEM software experience.
Introduction to Finite Element Method
The Introduction to Finite Element Method within the domain of engineering is an indispensable foundation to grasp the dynamics of this powerful numerical technique. As we embark on this journey, we will delve into the intricacies that define the essence and significance of Finite Element Method in engineering. This pivotal section will elucidate key principles, methodologies, and applications that underpin FEM, offering a profound insight into its transformative impact on the realm of engineering disciplines.
Definition of Finite Element Method
The Concept of Discretization
Exploring the crux of Finite Element Method, the concept of discretization emerges as a fundamental aspect that drives the efficacy of this numerical technique. Discretization entails the process of breaking down complex systems into smaller, more manageable elements, enabling precise numerical analysis. Its precision and efficiency in handling complex geometries make it a preferred choice in engineering simulations. The unique feature of discretization lies in its ability to provide accurate solutions by approximating continuous systems through discrete elements, paving the way for meticulous analysis and design processes within engineering realms.
Element Types in FEM
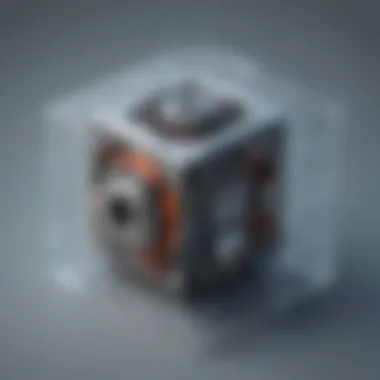
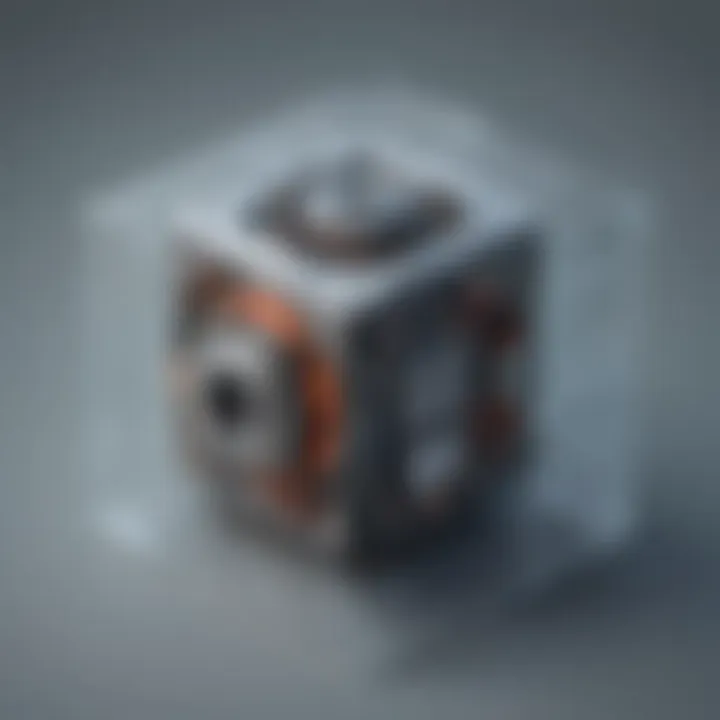
Diving into the realm of Finite Element Method, understanding the diverse element types in FEM is vital for comprehending its versatile applications. Element types in FEM encompass a range of shapes and formulations tailored to specific engineering analyses. Their flexibility and adaptability allow engineers to model various physical phenomena with precision, providing a robust framework for simulations. While each element type offers distinct advantages in specific scenarios, careful consideration of their limitations is crucial to ensure the accuracy and reliability of FEM simulations.
Historical Background
Origins and Evolution of FEM
Tracing the origins and evolution of Finite Element Method unveils a rich history marked by groundbreaking developments in numerical analysis. The roots of FEM can be traced back to pioneering efforts in structural mechanics and aerospace engineering, where early formulations laid the groundwork for modern finite element techniques. The evolution of FEM reflects a continuous refinement of computational methodologies, ushering in a new era of simulation-driven engineering practices. Understanding this historical context illuminates the progressive nature of FEM and its enduring impact on contemporary engineering disciplines.
Pioneering Contributions
Exploring the pioneering contributions to Finite Element Method offers insights into the innovative minds that shaped its inception and evolution. Visionary engineers and mathematicians have played a pivotal role in developing theoretical frameworks and computational algorithms that underpin FEM. Their contributions have not only revolutionized engineering analysis but also paved the way for novel applications across diverse industries. By acknowledging these pivotal figures, we gain a deeper appreciation for the intellectual heritage that continues to drive advancements in numerical simulations and design optimization.
Fundamental Principles of FEM
The Fundamental Principles of the Finite Element Method (FEM) serve as the cornerstone of this article, illuminating the essential concepts that underpin this powerful numerical technique. Variational Formulation and Discretization Process emerge as critical aspects within this framework.
Variational Formulation
Principle of Virtual Work
The Principle of Virtual Work plays a pivotal role in FEM, offering a rigorous mathematical foundation for structural analysis. By formulating equilibrium equations based on virtual displacements rather than real displacements, this method simplifies complex structural problems into solvable equations. Its key characteristic lies in its ability to ensure equilibrium for virtual displacements, providing valuable insights into structural behavior. A unique feature of the Principle of Virtual Work is its capacity to handle intricate loading conditions with accuracy. While advantageous in its precision, challenges may arise in complex material models that can affect solution convergence.
Galerkin's Method
Galerkin's Method is another fundamental component of FEM, enhancing the accuracy of numerical solutions through weighted residual principles. By approximating the solution and residual functions using different sets of functions, Galerkin's Method minimizes error while solving differential equations. Its key characteristic lies in the optimal way it balances solution accuracy and computational efficiency. The unique feature of Galerkin's Method is its versatility in handling various boundary conditions efficiently. While advantageous in its robustness, drawbacks may surface in nonlinear analysis scenarios requiring iterative solution strategies.
Discretization Process
Mesh Generation Techniques
Mesh Generation Techniques are instrumental in discretizing continuous structures into finite elements. These techniques, such as Delaunay triangulation and advancing front methods, facilitate the creation of high-quality meshes essential for accurate simulations. Their key characteristic lies in enabling the representation of complex geometries with ease, ensuring reliable numerical outputs. A unique feature of Mesh Generation Techniques is their adaptability to different structures and material properties, providing versatile modeling capabilities. While advantageous in their ability to capture intricate details, challenges may arise in managing large-scale simulations that demand substantial computational resources.
Interpolation Functions
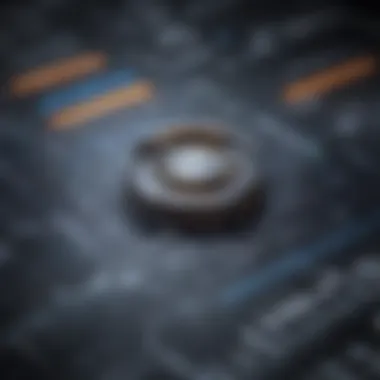
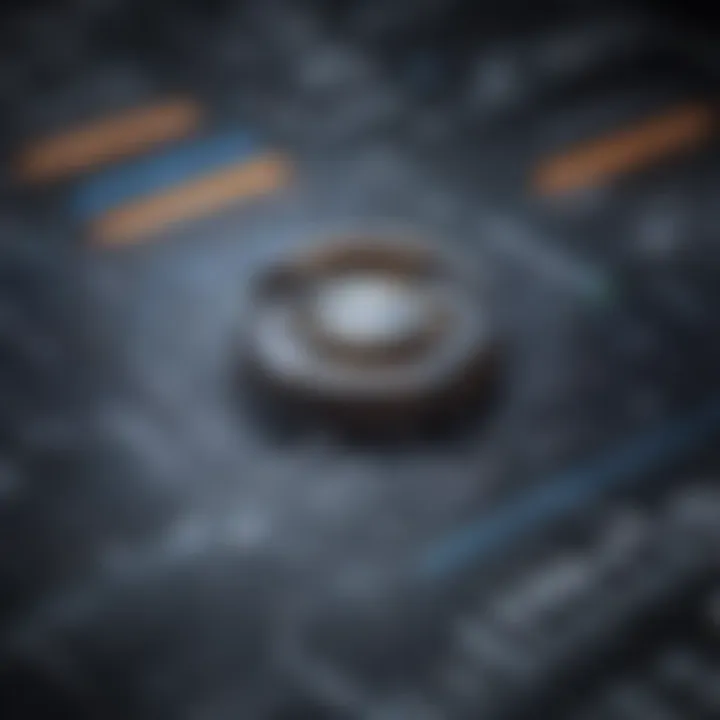
Interpolation Functions play a crucial role in defining the behavior of elements within a mesh. By approximating unknown quantities at specific points using nodal values, interpolation functions enable the transfer of boundary conditions and loads between nodes. Their key characteristic lies in ensuring continuity and differentiability across element boundaries, fostering smooth solutions within the mesh. A unique feature of Interpolation Functions is their capability to handle complex material behavior accurately, enhancing the realism of simulations. While advantageous in maintaining accuracy, limitations may surface in highly nonlinear analyses requiring specialized interpolation strategies.
Applications of Finite Element Method
In the realm of engineering, the applications of the Finite Element Method (FEM) stand as crucial pillars driving innovation and efficiency. FEM plays a pivotal role in facilitating detailed analyses and simulations for a myriad of engineering disciplines, enhancing decision-making processes and design optimization. Understanding the applications of FEM is paramount in comprehending its far-reaching impact on structural integrity, performance evaluation, and system behavior within engineering projects. As we delve deeper into the specific elements and benefits of FEM applications in this article, we will unearth the transformative power and intricate capabilities that FEM brings to the engineering landscape.
Structural Engineering
Stress Analysis
Stress analysis, a fundamental component of structural engineering, embodies a critical aspect of FEM applications. By dissecting the distribution of internal forces and stresses exerted on a structure under varying conditions, stress analysis enables engineers to assess the resilience and integrity of designs accurately. The key characteristic of stress analysis lies in its ability to pinpoint stress concentration areas and potential weak points, thereby aiding in design optimization and risk mitigation. This detailed analysis provides valuable insights into the structural performance, allowing for fine-tuning of materials and geometries to enhance safety and longevity. While stress analysis offers invaluable advantages in predicting failure points and structural behavior, it also presents challenges in accurately modeling complex real-world scenarios, demanding meticulous attention to detail and calibration for reliable outcomes within this article.
Modal Analysis
Conversely, modal analysis within structural engineering serves as a complementary aspect of FEM applications, focusing on determining natural frequencies and mode shapes of structures. By unraveling the dynamic characteristics and vibration modes of a system, modal analysis aids in predicting structural responses to external stimuli and optimizing designs for operational efficiency. The key characteristic of modal analysis lies in its effectiveness in identifying resonant frequencies and potential dynamic instabilities, providing crucial insights for performance enhancement and structural durability. While modal analysis offers significant advantages in predicting structural behavior under dynamic loads and optimizing operational parameters, it necessitates careful consideration of boundary conditions and mode shapes for accurate results within this article.
Fluid Dynamics
Flow Simulations
When considering fluid dynamics applications of FEM, flow simulations emerge as instrumental tools in analyzing fluid behavior and optimizing system performance. By simulating fluid flow patterns and pressure distributions within a given domain, flow simulations enable engineers to evaluate thermal characteristics and fluid interactions with precision. The key characteristic of flow simulations lies in their capacity to model complex fluid phenomena and predict flow behavior under diverse operating conditions, facilitating enhanced design decisions and performance improvements. Despite their benefits in visualizing flow dynamics and optimizing system efficiency, flow simulations require adequate mesh resolution and boundary condition definitions to ensure accuracy and reliability within this article.
Heat Transfer Analysis
Conversely, heat transfer analysis plays a vital role in fluid dynamics applications, focusing on quantifying temperature distributions and heat transfer mechanisms within systems. By assessing heat conduction, convection, and radiation effects, heat transfer analysis enables engineers to optimize thermal performance, enhance energy efficiency, and prevent overheating issues. The key characteristic of heat transfer analysis lies in its ability to predict temperature gradients and thermal behavior under varying heat loads, providing essential insights for system optimization and cooling strategies. While heat transfer analysis offers valuable advantages in assessing thermal management and optimizing energy utilization, it demands precise modeling of material properties and heat exchange mechanisms for accurate outcomes within this article.
Advantages of Finite Element Method
The section on 'Advantages of Finite Element Method' serves as a pivotal focus in this insightful article, shedding light on the importance and impact of utilizing FEM in engineering practices. The discussion delves into specific elements that distinguish FEM as a predominant numerical technique in various fields of engineering and science. By highlighting key benefits and considerations regarding Advantages of Finite Element Method, readers will grasp a profound understanding of how FEM revolutionizes conventional analysis and design processes.
Versatility and Accuracy
Ability to handle complex geometries
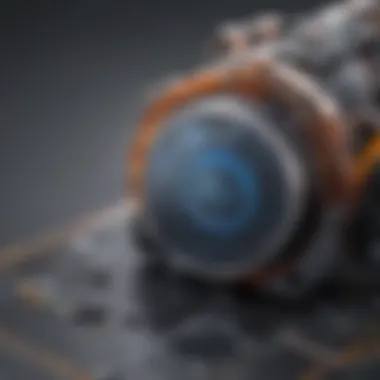
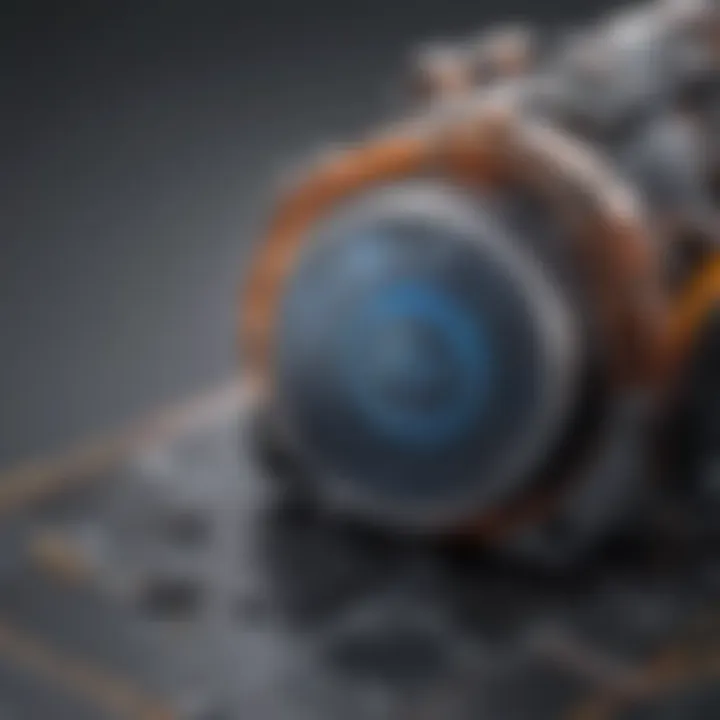
The ability to handle complex geometries stands out as a notable strength of FEM, enabling engineers and scientists to tackle intricate structural and fluid dynamics challenges with precision and efficiency. This key aspect of FEM allows for detailed modeling and analysis of intricate geometrical structures, granting a nuanced insight into their behaviors under varying conditions. The unique feature of FEM, specifically its capacity to tackle complex geometries, enhances the accuracy and reliability of solutions, making it a preferred choice in advanced engineering applications. Despite its benefits, challenges can arise regarding computational complexity, necessitating thorough optimization strategies to ensure efficient simulations and analyses.
Precision in solution
Precision in solution represents a fundamental aspect of FEM that underpins its efficacy in providing accurate engineering solutions. This characteristic ensures that computational models generated through FEM align closely with real-world behaviors, offering reliable predictions and insights into complex engineering phenomena. The precision in solution attained through FEM contributes significantly to the overall goal of enhancing engineering design processes and optimizing structural performance. However, maintaining high precision within computational models may demand considerable computational resources, necessitating a balance between accuracy and computational efficiency for optimal results.
Cost-Effectiveness
Reduction in physical prototyping
The reduction in physical prototyping facilitated by FEM streamlines the design and testing phases of engineering projects, resulting in significant cost savings and time efficiencies. By leveraging virtual simulations and analyses offered by FEM, engineers can minimize the need for expensive physical prototypes, thus accelerating the development timeline and reducing overall project costs. The unique feature of FEM lies in its ability to simulate real-world scenarios accurately, minimizing the reliance on time-consuming and costly physical prototyping processes. Nevertheless, transitioning to a fully virtual prototyping approach may pose challenges in terms of validating simulation results and ensuring comprehensive design assessments.
Time-saving benefits
FEM's time-saving benefits play a crucial role in enhancing efficiency and productivity within engineering endeavors, enabling rapid iterations and optimizations in design processes. The swift computational capabilities of FEM allow engineers to expedite analysis procedures, iterate on design variations, and explore alternative solutions within compressed timeframes. The key characteristic of time-saving benefits in FEM highlights its value in accelerating decision-making processes and fostering quicker project delivery. Despite its advantages, optimizing time-saving benefits in FEM implementations necessitates robust computational infrastructure and algorithmic efficiencies to maximize time-to-market strategies and operational cost-effectiveness.
Challenges and Limitations
In the realm of engineering, understanding the Challenges and Limitations associated with the Finite Element Method (FEM) holds paramount importance. These challenges serve as crucial checkpoints in the design and analysis processes, ensuring the reliability and accuracy of FEM applications. By delving into the complexities of mesh sensitivity and computational resources, engineers can fine-tune their models to achieve optimal results. Handling these challenges adeptly distinguishes seasoned professionals from novices, showcasing a deep understanding of the intricacies of FEM.
Mesh Sensitivity
Impact of element size
The Impact of element's size plays a pivotal role in the accuracy and computational efficiency of FEM models. Element size directly influences the level of detail captured in the analysis, with smaller elements providing higher resolution but demanding more computational resources. Engineers must strike a delicate balance between element size and model complexity to ensure precise results without compromising computational speed. Understanding the nuances of element sizing empowers engineers to tailor their simulations to meet specific requirements, optimizing performance and outcomes.
Convergence issues
Convergence issues represent a common challenge in FEM, where models fail to reach a stable solution as iterations progress. These issues often stem from improper meshing, material properties, or boundary conditions, requiring meticulous troubleshooting to rectify. Addressing convergence problems involves adjusting solver settings, refining mesh quality, and validating assumptions to align the model with physical reality. By navigating through convergence challenges effectively, engineers enhance the robustness and accuracy of their simulations, paving the way for reliable engineering analyses.
Computational Resources
Hardware requirements
A critical aspect of employing FEM is understanding the hardware requirements necessary for running complex simulations. High-fidelity analyses demand substantial computational power and memory capacity to execute efficiently. Engineers need to assess their hardware configurations to ensure compatibility with the software and the complexity of the models. Investing in robust hardware setups enhances the speed and accuracy of simulations, enabling engineers to tackle intricate engineering problems with confidence.
Solver complexity
Solver complexity delves into the intricate algorithms and methodologies used to solve FEM equations iteratively. As models become more sophisticated, the computational burden on solvers increases, necessitating efficient and scalable solver strategies. Balancing solver complexity with solution accuracy is crucial, as overly complex solvers may lead to excessive computation times without significant gains in precision. By leveraging appropriate solver techniques and algorithms, engineers can expedite simulations while maintaining high levels of accuracy in their analyses.