Thermal Simulators: A Comprehensive Exploration
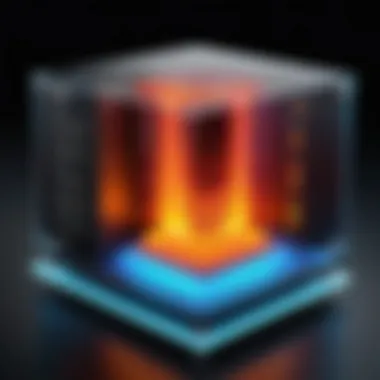
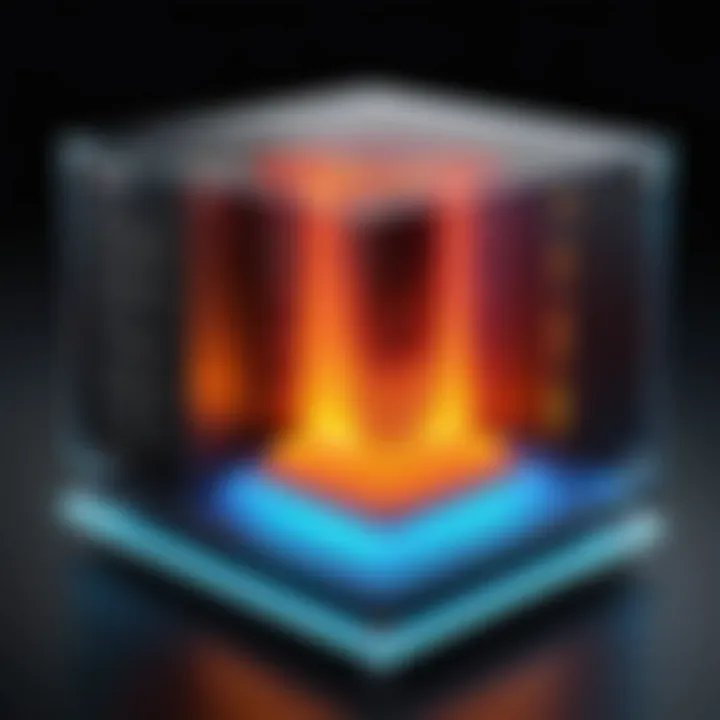
Intro
Thermal simulators have become pivotal in a variety of fields, including engineering, product design, and environmental studies. Their primary function involves simulating heat transfer processes, allowing users to predict thermal behaviors under various conditions. This capability is invaluable as it informs decision-making, optimizes designs, and enhances performance in real-world applications.
Typically, these simulators rely on underlying principles of thermodynamics and fluid dynamics. This article delves specifically into the different types of thermal simulators available, their functionalities, and how they integrate into daily workflows. By understanding both their advantages and potential pitfalls, professionals can leverage these tools to achieve maximized efficiency.
Software Overview
Features and functionalities
Thermal simulators come equipped with a variety of features. Most simulations include the ability to model steady-state and transient heat conduction, convection, and radiation. Sophisticated software can also integrate with three-dimensional modeling tools, enabling precise visualization of thermal distributions.
Users can expect functionalities such as:
- Real-time monitoring of heat transfer events.
- Data logging capabilities to track performance over time.
- Integration with CAD software for better design outcomes.
Pricing and licensing options
Pricing for thermal simulation software can vary significantly based on capabilities and target industries. Subscription models and perpetual licenses are common. For instance, ANSYS offers different tiers to accommodate small businesses as well as large enterprises, ensuring accessibility for diverse users.
Supported platforms and compatibility
Most thermal simulators support various platforms like Windows and Linux. Some newer tools even offer cloud-based solutions that enhance accessibility and collaboration. Cross-compatibility with other design software is also a critical point to consider for many users.
User Experience
Ease of use and interface design
The user interface varies per software. Generally, an intuitive design improves usability. The most effective thermal simulators provide straightforward navigation, allowing users to focus more on analysis rather than software intricacies.
Customizability and user settings
Flexibility in user settings can significantly enhance workflows. Most prominent thermal simulators allow customization options for simulation parameters, enabling users to tailor performances according to specific requirements.
Performance and speed
Performance can be a notable factor, especially when dealing with large-scale simulations. Efficient solvers and robust computational engines enhance speed, making complex calculations faster and more reliable.
Pros and Cons
Strengths and advantages of the software
Thermal simulators contribute substantial strengths like:
- Predictive accuracy in thermal performance.
- Reduced product development cycles by identifying potential issues early.
- Cost savings through optimization of materials and designs.
Drawbacks and limitations
While beneficial, thermal simulators may present drawbacks:
- High initial costs for advanced tools.
- Steeper learning curve for more complex functionalities.
- Possible limitations in handling unique materials or new technologies.
Comparison with similar products
Among competitors, SolidWorks Thermal and Autodesk CFD are popular alternatives. Each tool offers distinct features, yet choosing the most suitable software often comes down to specific use-case scenarios and user needs.
Real-world Applications
Industry-specific uses
Thermal simulators find applications in multiple industries.
- Aerospace: Optimizing engine thermal efficiency.
- Electronics: Managing heat dissipation in microchips.
- Construction: Analyzing building materials for energy efficiency.
Case studies and success stories
Several companies have reported successes by implementing thermal simulation. For example, an automobile manufacturer improved engine cooling designs, leading to better performance and reduced emissions.
How the software solves specific problems
Thermal simulators address key issues such as overheating, energy inefficiency, and material failure by predicting outcomes before they occur. This proactive approach can save both time and money in the development process.
Updates and Support
Frequency of software updates
Regular updates are essential for ensuring software remains relevant. Companies like COMSOL provide consistent updates to include the latest features and improve performance.
Customer support options
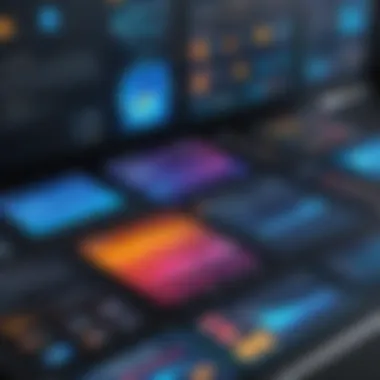
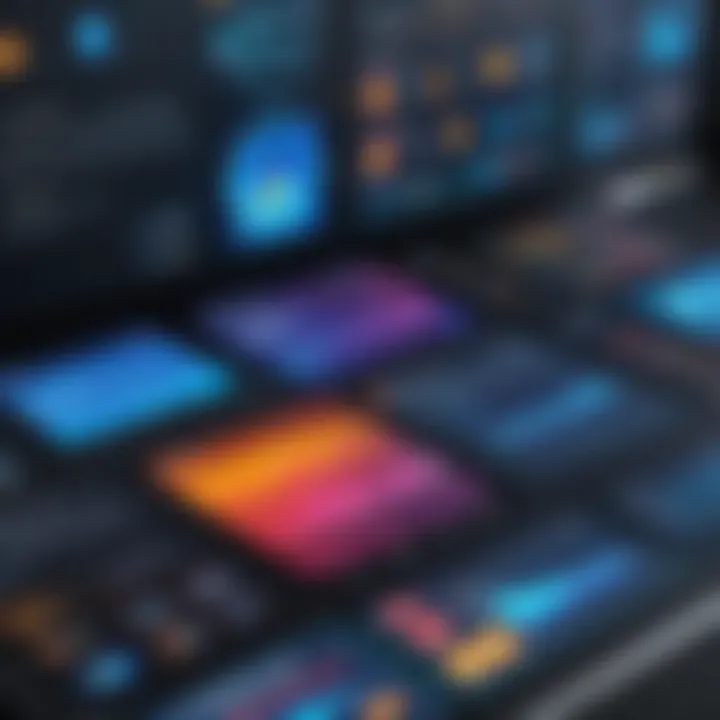
Robust customer support is crucial. Most thermal simulators offer various support channels, including online documentation, chat assistance, and phone support.
Community forums and user resources
Many software solutions foster community engagement through user forums. These platforms allow users to share experiences and solutions, further enhancing the overall user experience.
"Thermal simulators play a crucial role in today’s tech-heavy industries, helping professionals anticipate problems before they arise."
By understanding the functionality, user experience, and applications of thermal simulators, ethe reader can better assess which tools will fit their unique needs. This knowledge lays the foundation for more informed decision-making and effective use of thermal simulation technology.
Prelude to Thermal Simulators
Thermal simulators play a crucial role in various industries where managing heat is essential for product performance and reliability. Understanding how these simulators operate can aid businesses in making informed decisions about design and engineering processes. The importance of thermal simulators cannot be overstated, as they are vital in sectors such as electronics, aerospace, automotive, and renewable energy.
Definition and Purpose
Thermal simulators are software tools used to predict and analyze heat transfer within a given system. They simulate the temperature distribution and energy flow based on the principles of thermodynamics. These simulators serve multiple purposes, which include evaluating thermal performance, ensuring safety, and optimizing designs before physical prototypes are created.
For instance, in the electronics industry, overheating can lead to system failures. Thermal simulators allow engineers to identify potential hotspots and mitigate heat-related issues before production, ensuring reliability.
Historical Context
The development of thermal simulation technology has evolved significantly over the decades. In the early stages, engineers relied on analytical methods and simplified models to estimate thermal behavior. However, as technology advanced, the emergence of computer-aided design (CAD) software integrated with thermal simulation capabilities transformed the industry.
Today, we see sophisticated tools that combine various heat transfer principles, providing engineers with the ability to model complex geometries and scenarios. This evolution has enabled faster iteration cycles and significantly improved design accuracy. Thus, understanding the historical context helps appreciate how far the technology has come and its relevance to current practices.
The Science Behind Thermal Simulation
Understanding the science behind thermal simulation is crucial for comprehending how these tools function and their significance in various fields. Thermal simulators allow for the accurate modeling of heat transfer and thermodynamic phenomena, which are fundamental in numerous industries. This section will cover essential principles, mechanisms, and mathematical models that form the backbone of thermal simulation.
Thermodynamics Principles
Thermodynamics is the branch of physics that deals with heat, work, and energy. It is essential for thermal simulation as it provides the foundational laws that govern energy transfer processes. The three primary laws of thermodynamics influence how thermal simulators predict the behavior of materials under varying temperature conditions:
- First Law: This law, also known as the law of energy conservation, states that energy cannot be created or destroyed. It can only change from one form to another. In thermal simulation, this principle helps to account for energy inputs and outputs throughout a system.
- Second Law: This law introduces the concept of entropy, indicating that energy transfer has a direction. Heat naturally flows from hot objects to cold ones. Understanding this law assists engineers in modeling heat flow and optimizing designs.
- Third Law: This law states that as the temperature of a system approaches absolute zero, the entropy approaches a constant minimum. This has implications for materials at very low temperatures and is pertinent in cryogenics applications.
These principles serve as the bedrock upon which thermal simulation algorithms are built, allowing for accurate predictions and analysis.
Heat Transfer Mechanisms
Heat transfer can occur through three primary mechanisms: conduction, convection, and radiation. Each mechanism plays a pivotal role in how heat is transferred in different materials and environments:
- Conduction: This is the transfer of heat within a solid material or between solids that are in direct contact. The effectiveness of conduction depends on the material properties, such as thermal conductivity. For instance, metals like copper exhibit high thermal conductivity.
- Convection: This involves the transfer of heat by the physical movement of fluid. In thermal simulators, convective heat transfer is often modeled in situations involving fluids, such as air or water, where temperature differences cause movement. This is prevalent in cooling systems, where heat must be dissipated efficiently.
- Radiation: Unlike conduction and convection, radiation does not require a medium to transfer heat. It involves the emission of energy in the form of electromagnetic waves. This mechanism becomes significant at high temperatures and is important in applications involving heat exchangers or thermal imaging.
Thermal simulators incorporate these mechanisms to simulate real-world conditions accurately and predict thermal behavior under various scenarios.
Mathematical Models Used
Mathematical modeling is integral to thermal simulation, translating physical principles into equations and algorithms. Several mathematical models are used, each tailored to specific applications or simulation requirements:
- Finite Element Method (FEM): FEM divides complex structures into smaller, manageable elements, allowing for detailed analysis of heat distribution and temperature changes within a system. It is widely used in engineering simulations.
- Computational Fluid Dynamics (CFD): CFD employs numerically solving fluid dynamics equations to analyze heat transfer within fluids. This is particularly useful in cases involving complex flow patterns and heat exchanges.
- Lumped Capacitance Model: This simplification assumes that temperature varies only over time and not within the material. It is suitable for objects with relatively uniform temperature conditions.
Using these models, thermal simulators can provide insights that are often impossible to achieve through physical experiments alone.
"Thermal simulation is not just about predicting temperatures; it's about understanding the dynamics of heat and energy in a practical context."
Categories of Thermal Simulators
Understanding the different categories of thermal simulators is essential for professionals managing thermal management in various engineering fields. Each category serves specific purposes and offers distinct advantages. Recognizing the unique features of these simulators can enhance design processes and lead to more effective solutions for thermal issues.
3D Thermal Simulators
3D thermal simulators provide a comprehensive understanding of heat transfer in three-dimensional space. These simulators use sophisticated algorithms to evaluate temperature distribution and heat flow in complex geometries. 3D models are crucial in industries where spatial implications of heat are significant, such as in the design of electronics or automotive components.
The ability of 3D simulators to visualize heat diffusion allows engineers to identify hotspots and optimize designs effectively. These simulators enable detailed analysis by incorporating real-world boundaries and materials properties. The simulation process can reveal how changes in design influence thermal behavior, promoting better product development that meets performance expectations without compromising safety.
2D Thermal Simulators
In contrast to their 3D counterparts, 2D thermal simulators simplify the modeling process by focusing on two-dimensional heat flows. While they may lack the full depth of 3D models, 2D simulators are advantageous for specific applications like electronics cooling and HVAC system designs. They are faster and less resource-intensive, making them ideal for initial design stages.
Typically, engineers use 2D simulations to gauge system performances, often later validating findings with more complex 3D models. The balance between speed and sufficient accuracy makes 2D thermal simulators a useful tool in the early phases of product design. They can help establish boundary conditions for complex simulations that may follow.
Finite Element Analysis Tools
Finite Element Analysis (FEA) tools are powerful resources in thermal simulation. These tools apply numerical techniques to solve complex thermal performance issues by breaking down structures into smaller, manageable components. FEA allows the analysis of intricate geometries that would otherwise be challenging to simulate.
This method is valuable for evaluating thermal stresses and understanding the behavior of materials under varying thermal loads. FEA tools can simulate how materials expand or contract due to temperature changes, which is invaluable in sectors such as aerospace and automotive engineering. By providing accurate predictions of performance, FEA contributes to risk reduction in product development.
Computational Fluid Dynamics Applications
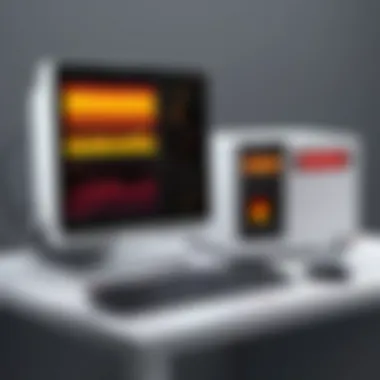
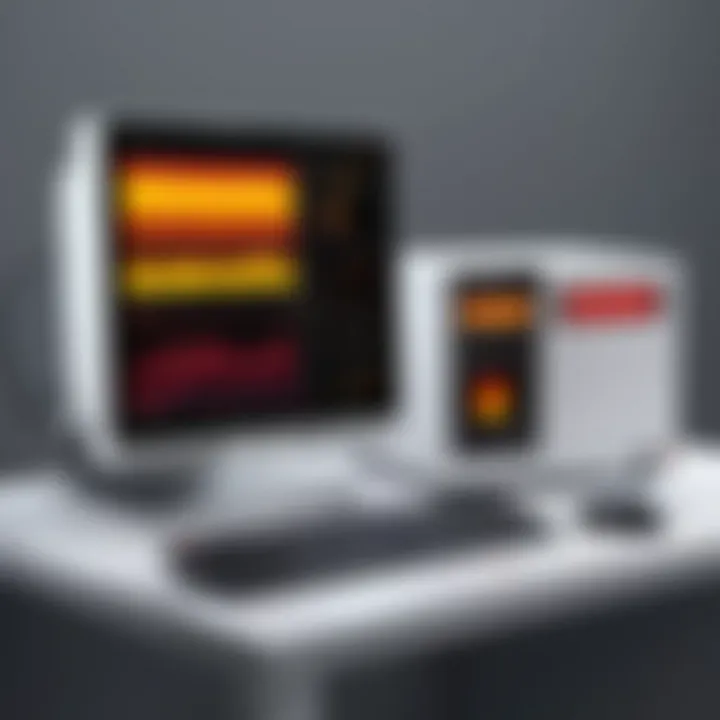
Computational Fluid Dynamics (CFD) applications play a significant role in thermal simulations, especially where fluid flow is coupled with heat transfer. CFD simulates fluid motion and heat transfer to analyze how fluids interact with thermal surfaces. This is essential in industries like renewable energy, where understanding airflow and temperature gradients is crucial for system efficiency.
CFD applications can predict how well a cooling system will perform, assist in the design of heat exchangers, and optimize HVAC systems. The results from these simulations can inform significant design changes that lead to enhanced performance. As technology advances, the integration of CFD with other simulation methods amplifies the insights obtainable from thermal simulations.
Applications of Thermal Simulators
Thermal simulators play a crucial role in multiple industries, allowing for comprehensive thermal analysis and design refinement. Their primary importance lies in enhancing the efficiency and effectiveness of various applications, which is vital in the modern technological landscape. By simulating thermal behavior, engineers and designers can predict performance, identify issues early, and optimize solutions before physical prototyping. The following subsections will delve into specific applications across various sectors, showcasing the versatility and significance of thermal simulators.
Electronics Industry
In the electronics industry, thermal management is of paramount importance. Components such as processors and power devices generate significant heat during operation. Identifying and mitigating this heat is critical to ensure reliability and performance. Thermal simulators enable engineers to model heat dissipation in printed circuit boards and integrated circuits accurately.
Through detailed thermal simulations, engineers can assess heat sinks, airflow patterns, and materials' thermal properties. This analysis helps in reducing thermal resistance and optimizing cooling systems. Moreover, the data obtained from simulations can guide the placement of components to minimize heat buildup.
Aerospace Engineering
Aerospace engineering highly demands precision due to the complex environments aircraft and spacecraft operate within. Thermal simulators allow engineers to examine the thermal dynamics experienced by vehicles during ascent, descent, and cruising.
By simulating extreme temperature variations, engineers can ensure materials and components will withstand harsh conditions. Thermal performance prediction helps in designing systems such as avionics, propulsion, and thermal protection systems. Ultimately, the use of thermal simulators can lead to safer and more efficient aerospace designs.
Automotive Sector
In the automotive sector, thermal management has gained increased focus as vehicles become more reliant on electronics and hybrid technologies. Thermal simulators assist manufacturers in understanding heat generation within engines and electrical systems.
For instance, accurate heat distribution modeling can enhance battery efficiency and longevity in electric vehicles. Additionally, automakers can simulate crash scenarios to analyze thermal runaway risk in batteries. Consequently, these simulations contribute to improved vehicle performance, safety, and reliability.
Renewable Energy Solutions
With the rise of renewable energy sources, particularly solar power, thermal simulators have a significant role. In photovoltaic systems, thermal simulations help optimize solar panel placement and cooling arrangements. For solar thermal systems, they aid in assessing thermal storage efficiency and energy outputs based on varying conditions.
The implementation of thermal simulations can lead to cost-effective solutions and improved energy yield. Thus, the integration of thermal modeling in renewable energy contributes not only to individual projects but also to the broader pursuit of sustainable energy solutions.
Key Benefits of Using Thermal Simulators
Thermal simulators serve a vital role in diverse industries by enhancing processes and improving outputs. Understanding the key benefits of using thermal simulators is essential for professionals and businesses that aim to optimize their products and systems. The advantages can lead to better efficiency, cost savings, and improved performance, making them indispensable tools.
Cost-Effectiveness in Prototyping
Thermal simulators can significantly reduce the costs associated with physical prototyping. Traditional methods often require multiple iterations of designs, which are expensive and time-consuming. By using thermal simulators, engineers can model various scenarios and assess the thermal performance of designs without building multiple prototypes. This capability allows companies to allocate resources more efficiently and minimize material waste. The upfront investment in simulation software can quickly pay off through savings on manufacturing and testing processes.
Enhanced Design Precision
Precision in design is a critical factor in engineering. Thermal simulators offer detailed insights into how heat flows through components, enabling designers to create more effective and reliable systems. The computational accuracy of these simulators allows for adjustments and refinements that may not be possible with trial and error in physical models. This precision enhances the overall performance of the final product, preventing failures and ensuring compliance with industry standards and regulations. A well-designed and precise thermal management system can aid in extending the lifespan of equipment.
Time-Saving Advantages
Time efficiency is paramount in today’s fast-paced market. Thermal simulators facilitate quicker decision-making by allowing for rapid testing and iteration of designs. The simulation can quickly process various parameters, meaning engineers can explore many options in a fraction of the time it takes to conduct physical tests. As a result, projects can progress much faster from concept to realization. This reduced turnaround time not only improves project timelines but also allows companies to bring products to market more quickly.
Risk Reduction in Development
Managing risks in product development is crucial, especially in industries such as aerospace and electronics, where failures can have critical consequences. Thermal simulators help in identifying potential thermal issues during the early stages of development. By addressing these issues before physical production, companies can avoid costly recalls or redesigns. The ability to predict thermal behavior enables teams to make informed decisions about materials and designs, minimizing the chance of performance-related failures in the final product. This proactive approach contributes not only to safer products but also to increased customer trust and satisfaction.
"The proactive use of thermal simulators reduces the risk of product failure and enhances overall design reliability."
Challenges and Limitations
Understanding the challenges and limitations associated with thermal simulators is vital for users aiming to leverage these tools effectively. While thermal simulation technology can aid in design and development, it is not without its hurdles. Identifying these challenges helps mitigate risks and improve decision-making processes. This section delves into three primary concerns: modeling complex geometries, accuracy of simulation results, and computational demands.
Modeling Complex Geometries
One significant challenge in thermal simulation is the modeling of complex geometries. Systems in industries such as aerospace and automotive often involve intricate shapes. These shapes can complicate the simulation process. For instance, when simulating heat distribution in an engine component, the detailed geometry impacts how heat flows throughout the part.
Creating accurate models that capture all necessary features requires sophisticated software. If the complexity is not accurately represented, results can become misleading. This can lead to inadequate designs that fail to meet thermal requirements. The simulation software must balance detail with computational efficiency. Otherwise, lengthy computation times become a concern, pushing back project timelines.
Accuracy of Simulation Results
The accuracy of simulation results is equally critical. Ideal simulation conditions rarely match real-world situations. Factors such as material properties and environmental influences might differ significantly from what is assumed in the simulation. Additionally, user errors, such as incorrect boundary conditions or improper modeling approach, can lead to significant inaccuracies.
To enhance the reliability of the results, validation against experimental data is necessary. This allows users to determine the extent of error in their results. Continuous refinement of models and methods can further improve accuracy, but it also demands time and resources that might not always be available.
Computational Demands
Lastly, substantial computational demands pose a challenge. Thermal simulations often require significant processing power, especially for complex models or large datasets. High-performance computing resources can become essential in such cases. This creates an added cost that must be factored into project budgets. Moreover, limited computational resources can restrict the scope of simulations that professionals can run, influencing the quality of the outcomes.
Efforts to optimize computational efficiency continue to evolve. However, users must remain aware of these demands to avoid bottlenecks that delay projects and inflate costs. Addressing these considerations is crucial for successful thermal simulation projects.
Understanding these challenges and limitations is essential for anyone who works with thermal simulators, as it allows for better preparation and improved outcomes.
Technological Advancements in Thermal Simulation
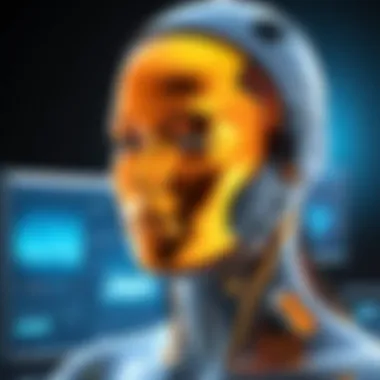
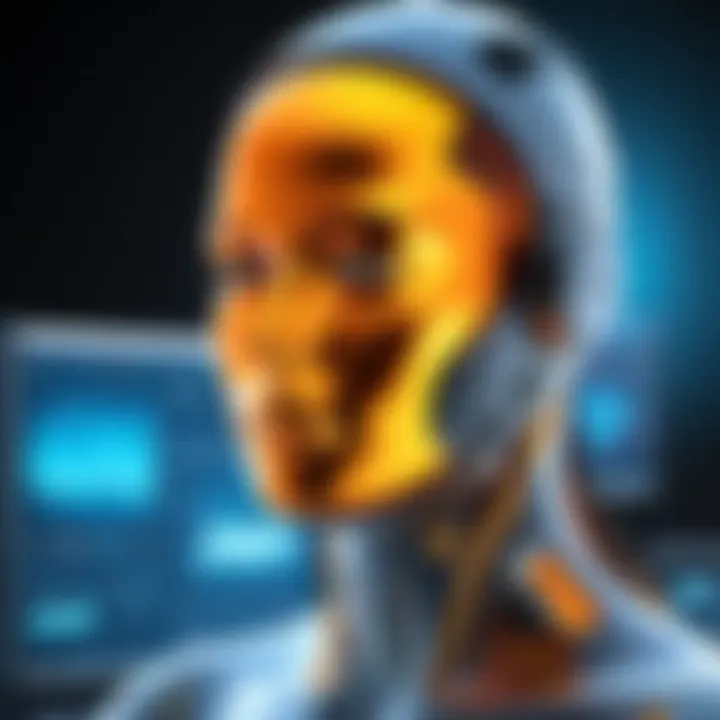
Technological advancements continue to reshape the landscape of thermal simulation tools. As industries demand higher performance and more accurate modeling, these advancements play a crucial role in meeting these needs. Notably, two areas are gaining significant traction: the integration of machine learning and the development of cloud-based simulation solutions. Understanding these elements is vital for professionals who aim to leverage the full potential of thermal simulators.
Integration with Machine Learning
The incorporation of machine learning into thermal simulation offers significant benefits, especially in the fields of predictive modeling and optimization. By using algorithms that learn from data, thermal simulators can analyze vast amounts of information more effectively than traditional methods. This ability enhances prediction accuracy and speeds up the simulation process.
Developers can now create models that not only simulate thermal behavior but also adapt based on real-world scenarios. For instance, a machine learning-enhanced simulator could predict failure points in a product’s design before it is even manufactured. This predictive capability allows engineers to make informed decisions early in the design process, ultimately resulting in a reduction of time and costs.
Some of the key advantages brought by this integration include:
- Improved accuracy of temperature predictions through data-driven insights.
- Faster convergence of simulations, significantly reducing computational resources.
- Ability to handle complex datasets, leading to better material selection and design optimization.
Cloud-Based Simulation Solutions
Cloud-based simulation solutions represent another significant leap forward in the field of thermal simulators. These solutions allow users to access powerful simulation tools via the internet, eliminating the need for high-end local hardware. This capability democratizes access to advanced thermal simulation features, making them available to small and large businesses alike.
Key benefits of cloud-based solutions include:
- Scalability: Users can scale resources according to their needs, only paying for what they use.
- Collaboration: Teams can collaborate in real time, regardless of geographic location, enhancing productivity.
- Data Storage and Management: Centralized cloud storage simplifies data management, allowing for easier sharing and archiving of simulation results.
The shift to cloud solutions means less overhead on physical infrastructure, enabling companies to invest more in innovation and technology upgrades rather than maintaining equipment.
"The push towards cloud solutions not only offers operational flexibility but also fosters a culture of innovation and continual improvement within organizations."
Comparative Analysis of Leading Thermal Simulation Software
Thermal simulation software plays a crucial role in various industries by offering insights into the thermal behavior of products and systems. A comparative analysis of such software helps organizations make informed decisions about which tools best meet their specific needs. Understanding the diverse options available can lead to better outcomes in design, efficiency, and risk management.
User Interface and Usability
A software's user interface (UI) significantly affects how efficiently users can interact with it. An intuitive UI allows engineers and designers to focus more on simulation results rather than grappling with confusing controls. This leads to increased productivity and faster learning curves for new users.
Many leading thermal simulators provide customizable layouts and shortcuts to enhance usability. For instance, users often appreciate features like drag-and-drop functionalities or preconfigured templates that streamline the modeling process. In addition to standard functionalities, real-time visualizations can greatly aid comprehension, allowing users to view changes dynamically as parameters are altered. Tools that prioritize user experience tend to reduce errors and improve the accuracy of simulation runs.
Pricing Models
When selecting thermal simulation software, potential users need to consider the pricing model. Various options exist, including subscription-based models, perpetual licenses, or one-time purchases. Subscription models often lower the initial cost but may incur ongoing expenses. Users must weigh these costs against their budget and usage frequency. For example, the annual subscription model may be ideal for companies needing software for a short-term project.
Conversely, a perpetual license can be more economical in the long term for frequent users, as there are no recurring fees. Discounts for educational institutions or package deals can also reduce overall expenses. It's essential for businesses to fully understand the implications of each pricing structure, including support and upgrade options.
Customer Support Options
Reliable customer support is a vital consideration when choosing thermal simulation software. Users may encounter technical issues that require immediate assistance. Therefore, evaluating the support services offered by each vendor is essential.
Many companies provide various customer support channels, including email, phone, and live chat. Additionally, some offer extensive online documentation, tutorials, or forums where users can find solutions to common problems. Comprehensive onboarding resources and training programs can further facilitate the transition to new software.
"Great customer support is not just about fixing issues; it's about empowering users to maximize the software's potential."
Selecting a software with robust support can significantly enhance the user experience and ensure that organizations can address challenges promptly.
By analyzing user interface, pricing models, and customer support options, companies can make informed decisions and choose the optimal thermal simulation software that aligns with their unique requirements.
Future Trends in Thermal Simulation
As industries evolve, the need for advanced thermal management solutions becomes more pressing. This need shapes the future trends in thermal simulation. Staying current means not only understanding the existing tools but also anticipating the next wave of developments. In this context, professionals and businesses alike must evaluate how these trends can bring enhancements in efficiency and sustainability. Moreover, factors like the demand for innovation and the changing market landscape dictate how these simulators advance.
Sustainability Considerations
Sustainability is not just a trend; it is an imperative. As environmental issues take center stage, thermal simulators are adapting to prioritize energy efficiency and resource conservation. By utilizing thermal simulation in the design phase, engineers can identify and mitigate energy losses, leading to more sustainable products. For example, optimizing thermodynamics in electronic devices can help reduce excess heat, thus lowering energy consumption and improving longevity.
This trend dovetails with the global push towards reducing carbon footprints across all sectors. Companies committed to sustainability leverage thermal simulators to meet compliance regulations and consumer expectations. Benefits include lower operational costs and enhanced brand reputation among eco-conscious clientele. The integration of sustainability metrics within simulation outcomes becomes crucial.
Key considerations in this area include:
- Reduction of waste through better design choices
- Improved energy efficiencies leading to lower greenhouse gas emissions
- Enhanced product life cycles
"By integrating sustainability into thermal simulation processes, companies can not only minimize environmental impacts but also create a competitive edge."
Innovations in User Accessibility
User accessibility is another pivotal trend. In the past, intricate thermal simulation software was often accessible only to specialized engineering teams. Now, advancements in software user interface design and functionality allow a broader audience to engage with thermal simulation tools. Innovative features reduce complexity and enhance usability, enabling not just experts but also designers and managers to make informed decisions based on simulation results.
Cloud computing plays a significant role in this change. Cloud-based thermal simulation platforms facilitate collaboration, allowing various stakeholders to access data and insights from anywhere. This decentralization of information promotes unified decision-making processes, central to modern development strategies.
From mobile-friendly applications to intuitive dashboards, the landscape of user interaction in thermal simulation tools is transforming. This evolution is critical, as it fosters an environment where holistic and cooperative development takes place.
In summary,
- Accessibility enhancements lead to increased collaboration
- Cloud integrations promote flexibility and real-time data access
- User-friendly interfaces democratize thermal simulation, enabling broader application
Understanding these trends equips IT and software professionals with the knowledge to leverage emerging technologies effectively. As a result, their organizations can innovate while maintaining efficiency and sustainability.
Finale
In this article, we have explored the essential facets of thermal simulators, highlighting their functionality, diverse applications, and the critical role they play in various sectors. The discussion of thermal simulators is fundamentally important, as they serve as indispensable tools for engineers and designers seeking to optimize thermal management in products and systems. Their ability to replicate real-world conditions leads to improved design outcomes and enhanced innovation across industries. Understanding their workings allows professionals to harness their full potential.
Recap of Key Points
The exploration of thermal simulators in this article included several significant points:
- Definition and Purpose: Thermal simulators are used to predict thermal behavior and are crucial in countless applications.
- The Science Behind Them: Principles of thermodynamics and heat transfer mechanisms form their foundation, underpinning the accuracy of simulations.
- Categories: We examined different types of simulators, including 3D and 2D thermal simulators, as well as finite element analysis tools and computational fluid dynamics applications.
- Applications: Their use spans multiple sectors, including electronics, aerospace, automotive, and renewable energy.
- Benefits: Key benefits were outlined, such as cost-effectiveness, precision in design, time savings, and risk reduction.
- Challenges: We acknowledged challenges associated with modeling complex geometries, achieving accuracy, and meeting computational demands.
- Technological Advancements: Integration with machine learning and cloud-based solutions marks a significant trend in the field.
- Comparative Software Analysis: Further insights into user interface, pricing, and customer support were provided to aid decision-making.
- Future Trends: Sustainability considerations and innovations for better accessibility were discussed.
Final Thoughts on Thermal Simulators
Thermal simulators represent a transformative technology in the engineering landscape. They not only improve efficiency in design processes but also foster responsible innovation by enabling designers and engineers to anticipate issues early in the development cycle. It is vital for IT professionals, software developers, and businesses to understand these tools, considering how they impact decisions related to product design and implementation. By leveraging thermal simulators effectively, organizations can enhance their competitive edge in an increasingly demanding market. In sum, mastering thermal simulation technology is not merely beneficial; it is imperative for future success in technology-driven industries.