Unraveling the Intricacies of ANSYS Fluid Dynamics in Software Systems
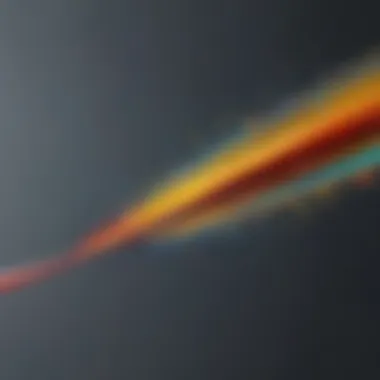
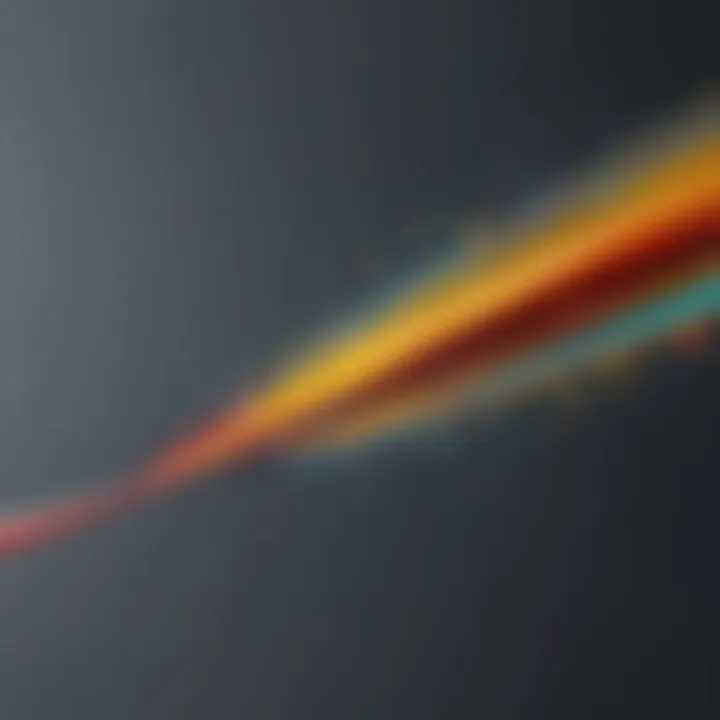
Software Overview
In delving into the dynamics of ANSYS Fluid in software systems, it is imperative to first grasp the underpinnings of this sophisticated tool. ANSYS Fluid boasts a wide array of features and functionalities that cater to the intricate needs of engineering professionals seeking advanced fluid dynamics simulations and fluid-structure interaction modeling. The software's pricing and licensing options provide flexibility to users, offering customizable packages based on specific requirements. Supported across various platforms, ANSYS Fluid ensures compatibility with different operating systems and software environments, enhancing its accessibility and usability.
User Experience
When exploring the user experience of ANSYS Fluid, one is greeted with an interface designed for efficiency and ease of use. The software's intuitive layout and navigation facilitate seamless interaction, allowing users to navigate complex simulations with ease. Customizability is a key aspect of the software, enabling users to adapt settings to their preferences and streamline workflows. Performance and speed are notable strengths of ANSYS Fluid, ensuring quick and reliable results for time-sensitive projects.
Pros and Cons
An in-depth analysis of ANSYS Fluid reveals a myriad of strengths and advantages that set it apart in the realm of engineering software. From high-fidelity simulations to robust fluid-structure interaction capabilities, the software excels in providing accurate and reliable results. However, it is essential to consider its limitations, including potential drawbacks such as steep learning curves for beginners and specific use cases where alternative solutions may be more suitable. A comparison with similar products highlights ANSYS Fluid's unique features and areas for potential improvement.
Real-world Applications
The real-world applications of ANSYS Fluid span across a multitude of industries, demonstrating its versatile utility in solving complex engineering challenges. From automotive engineering to aerospace design, the software finds extensive use in optimizing fluid dynamics and enhancing product performance. Case studies and success stories further underscore the software's efficacy, showcasing how it addresses specific problems and delivers tangible results for businesses and professionals alike.
Updates and Support
In the ever-evolving landscape of software development, regular updates and reliable support are essential components of a seamless user experience. ANSYS Fluid offers frequent software updates that enhance performance and introduce new features, keeping users abreast of the latest advancements in fluid dynamics simulation. Customer support options ensure timely assistance and resolution of queries, contributing to overall user satisfaction. Community forums and user resources create a collaborative environment for knowledge-sharing and problem-solving, enriching the user experience and promoting continuous learning within the ANSYS Fluid community.
Introduction to ANSYS Fluid
In the realm of software systems, the introduction to ANSYS Fluid plays a pivotal role. Understanding the basics, historical evolution, and significance of ANSYS Fluid is crucial in grasping its full potential. The dynamics and intricacies of ANSYS Fluid delve deep into fluid dynamics simulations and fluid-structure interaction modeling, making it an indispensable tool in engineering and simulation software.
Understanding the Basics of ANSYS Fluid
Theoretical Foundations
Delving into the theoretical foundations of ANSYS Fluid unveils its core principles and mathematical algorithms that form the basis of fluid dynamics simulations. These foundations provide a theoretical framework for understanding fluid behavior, crucial for accurate engineering analysis. The unique feature of theoretical foundations lies in their ability to simulate complex fluid dynamics scenarios with precision, although they may pose challenges in handling non-linear material behaviors.
Application in Engineering
The application of ANSYS Fluid in engineering revolutionizes the way fluid dynamics problems are solved. By simulating real-world scenarios, engineers can predict fluid behavior, optimize designs, and troubleshoot potential issues before physical prototyping. The key characteristic of application in engineering is its versatility, catering to a wide range of industries from automotive to aerospace. However, constraints in computational resources may limit the complexity of simulations.
Key Features and Capabilities
The key features and capabilities of ANSYS Fluid empower engineers and researchers to push the boundaries of fluid dynamics analysis. From advanced turbulence modeling to multiphase flow analysis, ANSYS Fluid excels in handling complex fluid behaviors. Its unique feature lies in the integration of fluid dynamics with structural mechanics, enabling comprehensive fluid-structure interaction studies. While its capabilities enhance simulation accuracy, they may require extensive computational resources.
Historical Evolution of ANSYS Fluid
Inception and Development
Revisiting the inception and development of ANSYS Fluid sheds light on its evolutionary path from rudimentary fluid simulations to sophisticated modeling techniques. The key characteristic of this evolution is the continuous enhancement of algorithms and solvers to improve simulation accuracy and efficiency. The unique feature of inception and development is the iterative refinement process that adapts to industry demands, yet runtime complexities may challenge simulation scalability.
Technological Advancements
The technological advancements in ANSYS Fluid have revolutionized fluid dynamics research and engineering applications. By integrating cutting-edge technologies, such as parallel computing and artificial intelligence, ANSYS Fluid has kept pace with industry demands for faster and more robust simulations. The key characteristic lies in its adaptability to emerging technologies, although integrating new features may require additional training and expertise.
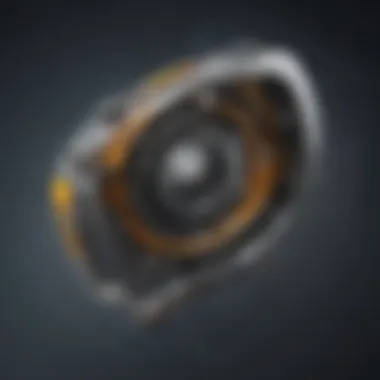
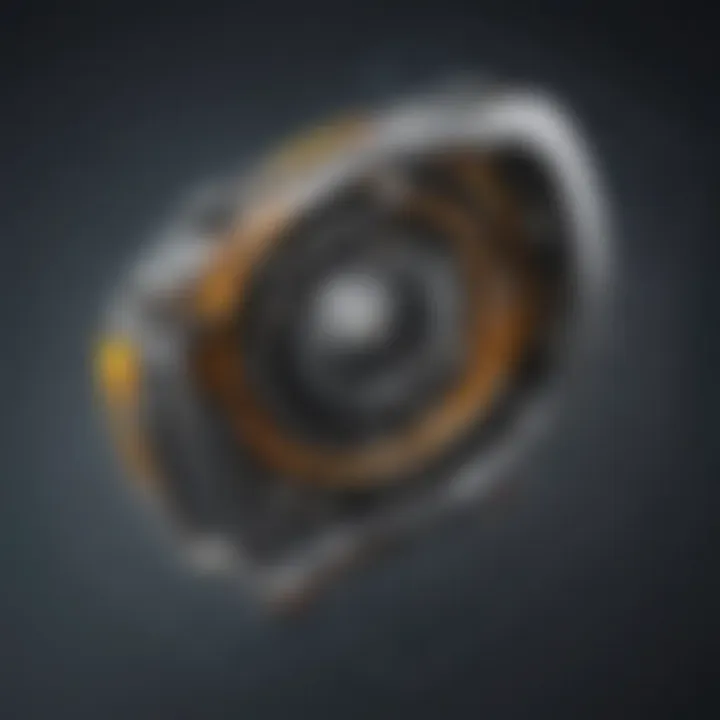
Impact on Fluid Dynamics Research
The impact of ANSYS Fluid on fluid dynamics research is profound, having shaped how engineers and researchers approach complex flow problems. By providing a platform for in-depth analysis and validation, ANSYS Fluid accelerates innovation in various fields. The key characteristic is its ability to bridge theoretical models with practical applications, though interpreting simulation results may demand a thorough understanding of fluid dynamics principles.
Significance in Simulation Software
Integration with ANSYS Suite
The integration of ANSYS Fluid with the broader ANSYS Suite amplifies its capabilities, offering a comprehensive platform for multiphysics simulations. By seamlessly combining fluid dynamics with structural, thermal, and electromagnetic analyses, engineers can capture complete system behaviors. The key characteristic is the synergy achieved through integration, yet mastering diverse simulation modules may require specialized training.
Role in Virtual Testing
ANSYS Fluid plays a crucial role in virtual testing, enabling engineers to conduct virtual experiments and assess product performance without physical prototypes. By simulating various operating conditions, designers can iterate on designs and optimize products efficiently. The key characteristic lies in its ability to simulate real-world scenarios accurately, although validating simulation results against physical tests remains a challenge.
Industry Applications
The industry applications of ANSYS Fluid span across aerospace, automotive, biomedical, and various engineering sectors, where fluid dynamics play a critical role. From optimizing aerodynamics in aircraft to simulating crash scenarios in automotive engineering, ANSYS Fluid addresses diverse industry needs. The key characteristic is its versatility in catering to different sectors, yet customizing simulations for specific applications may require domain expertise and validation against empirical data.
Advanced Features and Functionality
In the realm of ANSYS Fluid in software systems, the focus on Advanced Features and Functionality is paramount. These aspects play a crucial role in enhancing the capabilities and performance of ANSYS Fluid, making it a versatile tool for engineers and software developers alike. By delving into Advanced Features and Functionality, users can harness a myriad of benefits, including increased efficiency, accuracy, and versatility in fluid dynamics simulations. It enables users to tackle complex engineering problems with precision and efficacy, driving innovation and advancements in various industries. Considering the intricate nature of fluid dynamics, having robust Advanced Features and Functionality is instrumental in achieving reliable and insightful simulations.
Fluid Dynamics Simulations
Computational Fluid Dynamics (CFD)
Within the domain of Computational Fluid Dynamics (CFD) lies a profound method of analyzing fluid flow phenomena in engineering systems. Its contribution to ANSYS Fluid is immense, as it offers a comprehensive understanding of fluid behavior and its impact on the overall system performance. The key characteristic of CFD lies in its ability to simulate and visualize complex fluid dynamics, providing engineers with valuable insights into flow patterns, turbulence, and heat transfer processes. CFD is a popular choice for this article due to its effectiveness in simulating real-world fluid scenarios accurately. However, one must be mindful of the computational resources required for high-fidelity simulations and potential limitations in handling extreme conditions.
Turbulence Modeling
Turbulence modeling addresses the chaotic nature of fluid flow, which is essential for many engineering applications. ANSYS Fluid leverages turbulence modeling to predict turbulence effects accurately, enabling engineers to optimize designs and improve system performance. The unique feature of turbulence modeling lies in its ability to capture intricate flow behavior, such as eddies and vortices, enhancing the fidelity of simulations. While turbulence modeling enhances the realism of fluid dynamics simulations, it may introduce complexities and computational costs that need to be carefully managed.
Multiphase Flow Analysis
Multiphase flow analysis deals with scenarios where multiple phases coexist within a system, such as gas-liquid flows or solid-liquid interactions. It plays a vital role in understanding complex industrial processes, like oil and gas transport or particle-laden flows. ANSYS Fluid benefits from multiphase flow analysis by offering insights into phase distribution, interface dynamics, and mass transfer phenomena. The unique feature of multiphase flow analysis is its ability to simulate diverse phase interactions accurately, facilitating the design and optimization of multiphase systems. Nonetheless, users must account for the computational demands and model assumptions when conducting multiphase simulations.
Fluid-Structure Interaction Modeling
Structural Mechanics Coupling
The integration of structural mechanics coupling in ANSYS Fluid allows for a comprehensive analysis of interactions between fluid flow and structural responses in engineering systems. This aspect significantly contributes to the article by providing a holistic perspective on how fluid dynamics influence structural behavior and vice versa. The key characteristic of structural mechanics coupling lies in its ability to simulate coupled physics phenomena, aiding in the design of robust and efficient systems. Its unique feature resides in the seamless integration of fluid and structural analyses, enabling engineers to optimize system performance under varying operating conditions. Despite its advantages, structural mechanics coupling may pose challenges in terms of model complexity and computational costs that need to be carefully managed.
Dynamic Fluid-Structure Analysis
Dynamic fluid-structure analysis focuses on studying the transient interactions between fluids and structures under dynamic loading conditions. Within ANSYS Fluid, this analysis offers insights into the dynamic response of systems subjected to fluid-induced forces and vibrations. The key characteristic of dynamic fluid-structure analysis is its ability to predict system behaviors during transient events accurately. This feature is beneficial for applications requiring consideration of time-dependent phenomena, such as seismic events or fluid-structure resonance. However, conducting dynamic fluid-structure analysis may require sophisticated modeling techniques and computational resources to capture complex dynamic responses effectively.
Real-World Applications
The incorporation of real-world applications in ANSYS Fluid provides engineers with practical insights into how fluid-structure interactions manifest in various industries. By showcasing actual use cases and success stories, this aspect enhances the relevance and applicability of fluid-structure interaction modeling discussed in the article. The key characteristic of real-world applications lies in their ability to bridge theoretical concepts with practical implementation, fostering a deeper understanding of fluid-structure interactions in real engineering scenarios. Its unique feature is the demonstration of how ANSYS Fluid can address industry-specific challenges and optimize system performance effectively. While real-world applications offer valuable insights, selecting representative case studies and interpreting results accurately are crucial for deriving meaningful conclusions.
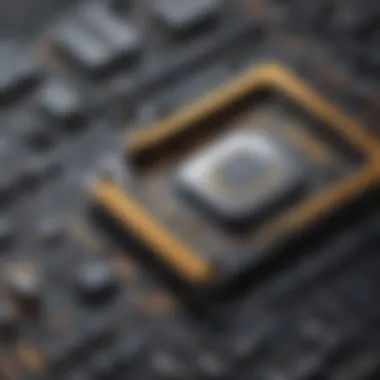
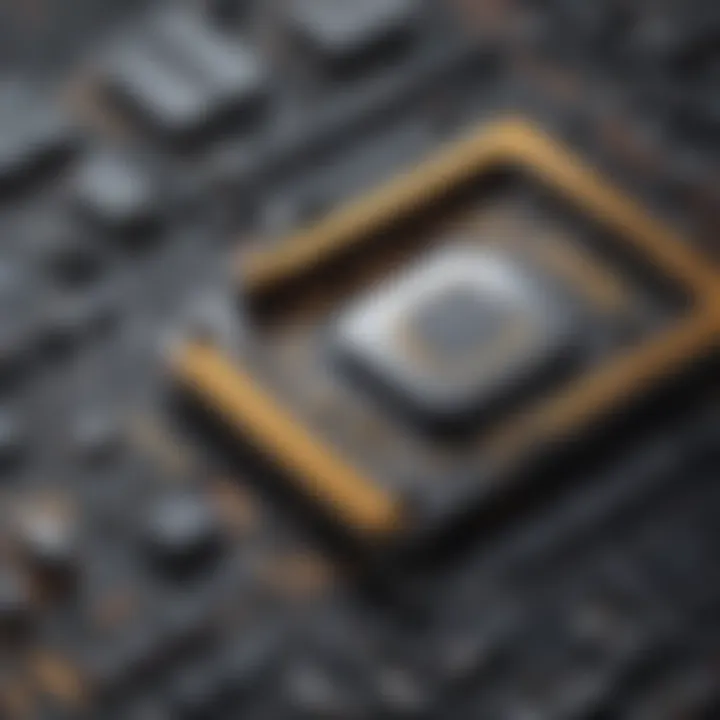
Optimization and Performance Enhancement
Design Exploration
Design exploration within ANSYS Fluid enables engineers to navigate the vast design space efficiently and identify optimal solutions that meet specified constraints and performance criteria. This aspect contributes significantly to the article by emphasizing the iterative and systematic approach to design optimization using ANSYS Fluid. The key characteristic of design exploration lies in its ability to automate the design optimization process, speeding up the identification of innovative solutions and enhancing productivity. Its unique feature resides in the integration of advanced algorithms and optimization techniques, allowing users to explore design alternatives effectively and make data-driven decisions. However, users should consider the trade-offs between computational efficiency and solution accuracy when employing design exploration techniques.
Parametric Optimization
Parametric optimization enables engineers to explore the influence of design parameters on system performance and make informed design decisions within ANSYS Fluid. This optimization technique plays a crucial role in fine-tuning designs, improving efficiency, and meeting design objectives. The key characteristic of parametric optimization is its ability to systematically evaluate design variations and their impact on performance metrics, facilitating the identification of robust design solutions. Its unique feature lies in the parametric sensitivity analysis, which highlights critical design factors affecting system behavior and performance outcomes. While parametric optimization streamlines the design process, users need to ensure the validity of optimization models and interpret results accurately to make informed design choices.
Efficiency Improvements
Efficiency improvements in ANSYS Fluid aim to optimize computational workflows, enhance solution accuracy, and reduce simulation times for engineering analyses. This aspect is crucial for maximizing productivity and streamlining simulation processes within the software. The key characteristic of efficiency improvements lies in their capacity to streamline pre-processing, solver settings, and post-processing tasks, simplifying the overall simulation workflow. Their unique feature is the integration of advanced algorithms and parallel computing technologies to expedite solution convergence and improve computational efficiency. While efficiency improvements enhance user experience and computational performance, implementing complex optimization strategies may require a balance between computational resources and simulation accuracy.
Industrial Applications and Case Studies
Industrial applications and case studies play a crucial role in our exploration of ANSYS Fluid within software systems. These real-world examples provide invaluable insights into the practical implementation and impact of ANSYS Fluid in various industries and disciplines. By delving into aerospace and aeronautics, automotive engineering, and biomedical engineering, we can uncover the diverse applications of ANSYS Fluid and how it revolutionizes simulation software in complex environments.
Aerospace and Aeronautics
Aerodynamic Analysis
Aerodynamic analysis forms the cornerstone of aeronautical design and engineering. By simulating airflow over aircraft surfaces, ANSYS Fluid enables engineers to optimize aerodynamics, reduce drag, and enhance overall flight performance. The precision and accuracy of aerodynamic analysis using ANSYS Fluid make it a go-to choice for aeronautical engineers worldwide. One standout feature of aerodynamic analysis is its ability to predict airflow behavior under various conditions, aiding in the design of efficient and high-performance aircraft. While its advantages are abundant, challenges may arise in areas requiring extensive computational resources for complex simulations, impacting overall efficiency.
Structural Integrity Testing
Structural integrity testing is paramount in ensuring the safety and reliability of aerospace components and systems. ANSYS Fluid facilitates comprehensive structural analysis by simulating stress, strain, and deformation in aircraft structures under different loads and environmental conditions. The versatility and in-depth analysis capabilities of structural integrity testing make it essential for validating the structural robustness of aerospace systems. An inherent strength lies in its ability to predict potential failure points and optimize design parameters for enhanced performance. However, the intricate nature of structural simulations can lead to longer computational times and model complexities, requiring careful consideration for accurate results.
Flight Simulation
Flight simulation using ANSYS Fluid enables realistic and immersive virtual environments for evaluating aircraft performance and handling characteristics. By replicating actual flight scenarios, engineers can assess aerodynamic behaviors, control responses, and emergency situations with high fidelity. The realism and accuracy offered by flight simulation serve as a crucial tool in training pilots, testing aircraft designs, and exploring innovative flight concepts. The interactive nature of flight simulations enhances user engagement but may pose challenges in terms of hardware requirements and data integration, necessitating efficient system configurations for optimal performance.
Automotive Engineering
Vehicle Performance Optimization
Within automotive engineering, vehicle performance optimization using ANSYS Fluid focuses on enhancing speed, fuel efficiency, and overall driving dynamics. By leveraging advanced CFD simulations, engineers can fine-tune vehicle aerodynamics, reduce drag, and improve handling characteristics. The versatility and adaptability of performance optimization tools make them instrumental in achieving superior automotive designs. A notable aspect of vehicle performance optimization lies in its ability to generate actionable insights for refining vehicle components and systems, leading to superior on-road performance. However, the intricate nature of these simulations requires expertise and computational resources, posing challenges in certain scenarios.
Crash Simulation
Crash simulation is a critical aspect of automotive safety and design, ensuring vehicles meet stringent regulatory requirements and uphold passenger safety standards. ANSYS Fluid enables engineers to simulate and analyze crash scenarios, assess impact dynamics, and optimize vehicle structures for enhanced crashworthiness. The accuracy and reliability of crash simulations make them indispensable in predicting vehicle behavior during collisions and improving occupant protection measures. A unique feature of crash simulation is its ability to simulate complex crash events in a controlled environment, providing valuable insights for designing robust vehicle safety systems. Despite its benefits, crash simulations demand substantial computational resources and thorough model calibration for accurate results.
Aerodynamics Testing
Aerodynamics testing using ANSYS Fluid is pivotal in evaluating vehicle performance, fuel efficiency, and stability under different airflow conditions. By conducting CFD simulations, engineers can identify aerodynamic inefficiencies, optimize vehicle shapes, and reduce drag for improved overall efficiency. The detailed insights provided by aerodynamics testing contribute to enhancing vehicle aerodynamics and minimizing energy losses during operation. One significant advantage of aerodynamics testing is its ability to unify design and performance considerations, fostering aerodynamic optimization throughout the vehicle development process. However, complexities in model setup and post-processing tasks may pose challenges, necessitating continuous refinement for optimal results.
Biomedical Engineering
Blood Flow Modeling
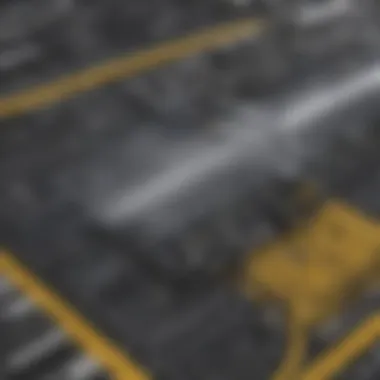
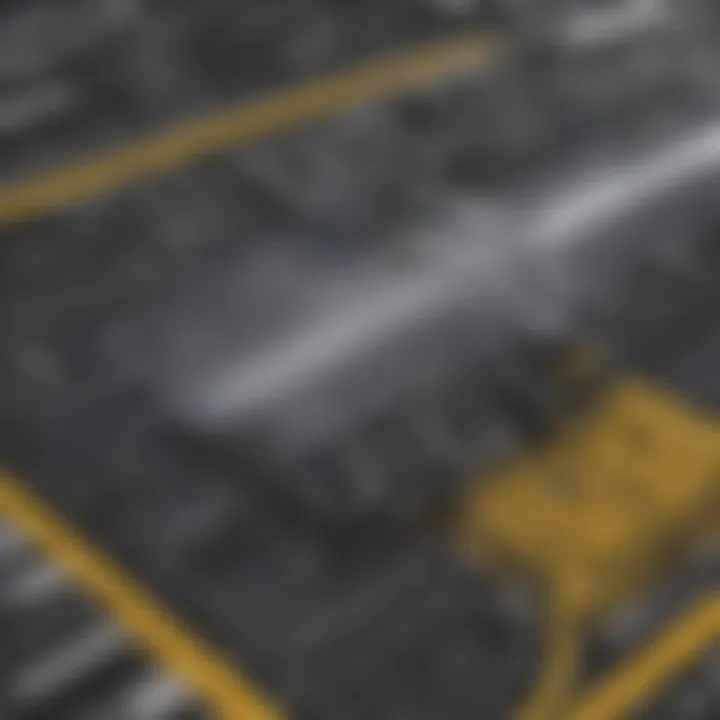
Blood flow modeling using ANSYS Fluid plays a pivotal role in biomedical engineering, aiding in the analysis of cardiovascular diseases, medical device designs, and physiological interactions. By simulating blood flow patterns and pressure distributions, engineers can assess vessel health, evaluate treatment strategies, and refine medical interventions. The accuracy and intricacy of blood flow modeling make it a fundamental tool in understanding vascular dynamics and pathology progression. A noteworthy feature of blood flow modeling is its capacity to simulate patient-specific scenarios for personalized medical assessments and interventions. Despite its advantages, complexities in blood flow simulations, including model calibration and validation, may pose challenges in achieving clinically meaningful results.
Medical Device Design
Medical device design with ANSYS Fluid focuses on optimizing device functionalities, material selections, and performance parameters for enhanced patient outcomes. By simulating device interactions within biological systems, engineers can refine device designs, assess compatibility, and improve therapeutic efficacy. The versatility and precision offered by medical device design simulations make them instrumental in developing innovative healthcare solutions. An inherent strength lies in their ability to predict device behavior under diverse conditions, facilitating design iterations and regulatory compliance. Nonetheless, the intricate nature of medical device simulations may entail intricate model validations and close collaboration with medical experts to ensure optimal design outcomes.
Biomechanics Analysis
Biomechanics analysis using ANSYS Fluid explores the interactions between biological systems and external stimuli to enhance treatment strategies, rehabilitative techniques, and sports performance evaluations. By simulating biomechanical responses and tissue behavior, engineers can gain insights into injury mechanisms, ergonomic designs, and physiological adaptations. The detailed analysis and predictive capabilities of biomechanics simulations are integral in optimizing treatment protocols and preventive measures in healthcare settings. A unique feature of biomechanics analysis is its ability to uncover intricate biomechanical phenomena and offer tailored interventions for diverse patient populations. Despite its advantages, challenges may emerge in model complexities and human variability considerations, necessitating continuous refinement for accurate biomechanical assessments.
Future Perspectives and Innovations
In delving into the future perspectives and innovations within the realm of ANSYS Fluid, it becomes evident that staying ahead of emerging technologies is paramount for software systems. As industries evolve, the integration of artificial intelligence (AI) stands out as a game-changer in enhancing fluid dynamics simulations. AI's ability to analyze extensive data sets and optimize complex processes caters to the needs of engineers and researchers. Moreover, machine learning applications offer adaptive solutions and predictive capabilities, making them indispensable in navigating fluid dynamics challenges. Cloud-based simulation emerges as a cost-effective and scalable option, enabling seamless collaboration and resource optimization.
Emerging Technologies in ANSYS Fluid
Artificial Intelligence Integration
The integration of artificial intelligence (AI) heralds a new era in fluid dynamics simulations by automating processes and enhancing accuracy through predictive algorithms. AI's capacity to learn from data patterns revolutionizes simulation outcomes, reducing manual intervention and time-consuming tasks. Its unique feature lies in its adaptability to evolving data trends, empowering engineers to make informed decisions swiftly. However, challenges such as data privacy and model interpretability need addressing to maximize the benefits of AI in ANSYS Fluid.
Machine Learning Applications
Machine learning applications offer dynamic insights by analyzing vast datasets and identifying patterns that streamline simulation processes in ANSYS Fluid. With its emphasis on predictive analytics, machine learning optimizes design iterations and accelerates problem-solving. Its distinctive feature lies in its adaptive learning capabilities that refine predictions and enhance simulation accuracy over time. Nonetheless, ensuring data quality and model scalability are essential considerations for implementing machine learning in ANSYS Fluid.
Cloud-Based Simulation
Cloud-based simulation emerges as a flexible and cost-efficient solution in conducting fluid dynamics analyses using ANSYS Fluid. Its key characteristic lies in enabling collaborative work environments and on-demand access to computing resources. The scalability and remote accessibility of cloud-based simulation offer significant advantages in optimizing workflow efficiency and reducing infrastructure costs. However, maintaining data security and addressing network dependencies are crucial for seamless integration of cloud-based simulation in ANSYS Fluid.
Industry Trends and Forecasts
Digital Twin Technology
Digital twin technology revolutionizes the way industries leverage ANSYS Fluid by creating virtual replicas of physical systems to optimize performance and predict maintenance needs. Its key characteristic of real-time monitoring provides invaluable insights into system behavior and performance metrics. The popularity of digital twin technology stems from its ability to enhance predictive maintenance, reducing downtime and optimizing operational efficiency. However, challenges such as data integration and fidelity maintenance require meticulous attention to harness the full potential of digital twin technology.
IoT in Simulation
The Internet of Things (IoT) integration in simulation bolsters ANSYS Fluid by capturing real-time data from interconnected devices to enhance predictive modeling and analysis accuracy. IoT's key characteristic involves data aggregation from various sensors to create a comprehensive overview of system dynamics. Its beneficial nature lies in its ability to optimize resource allocation and refine simulation outcomes through continuous data feedback. Mitigating security risks and ensuring interoperability are critical factors in successfully implementing IoT in simulation for ANSYS Fluid.
Sustainability Focus
The emphasis on sustainability within ANSYS Fluid leads to eco-conscious design principles and efficient resource management in fluid dynamics simulations. Sustainability's key characteristic lies in balancing environmental impact with performance optimization, promoting eco-friendly solutions in engineering practices. Its popularity stems from the growing demand for environmentally responsible technologies that drive innovation and social impact. However, achieving sustainable outcomes while maintaining performance standards requires a holistic approach to design and simulation methodologies.
Research and Development Initiatives
Collaborative Projects
Collaborative projects propel ANSYS Fluid into new frontiers by fostering interdisciplinary partnerships and innovation in fluid dynamics research. The key characteristic of collaborative projects lies in combining diverse expertise to tackle complex challenges and drive exceptional outcomes. The beneficial nature of collaboration stems from shared knowledge and resources, accelerating innovation cycles and expanding research horizons. However, aligning goals and priorities among collaborators and managing communication flow are essential for realizing the full potential of collaborative projects in ANSYS Fluid.
Innovation Partnerships
Innovation partnerships play a crucial role in enhancing ANSYS Fluid by fostering alliances with industry leaders and technology experts to drive technological advancements. The key characteristic of innovation partnerships involves leveraging complementary strengths to co-create solutions that push the boundaries of simulation capabilities. The advantageous aspect of collaboration lies in pooling resources and expertise to pioneer breakthrough innovations and address industry-specific challenges. Nonetheless, maintaining alignment in strategic goals and fostering a culture of innovation are pivotal for the success of innovation partnerships in advancing ANSYS Fluid.
Academic Collaborations
Academic collaborations contribute significantly to ANSYS Fluid by bridging the gap between theoretical research and practical applications in fluid dynamics simulations. The distinct feature of academic collaborations lies in their focus on fundamental research that underpins technological advancements in the software system. The advantageous nature of collaboration stems from the integration of academic insights and industry needs, driving innovation and skills development. However, aligning academic research goals with industry trends and fostering continuous knowledge exchange are imperative for sustained success in academic collaborations within ANSYS Fluid.