Maximizing Innovation: The Role of Engineering CAD Software in Product Development
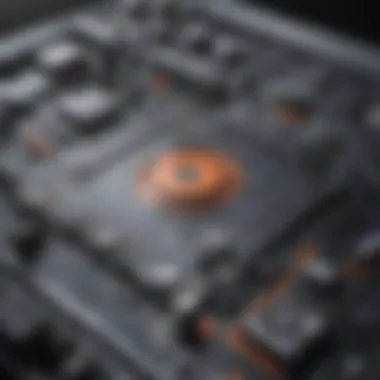
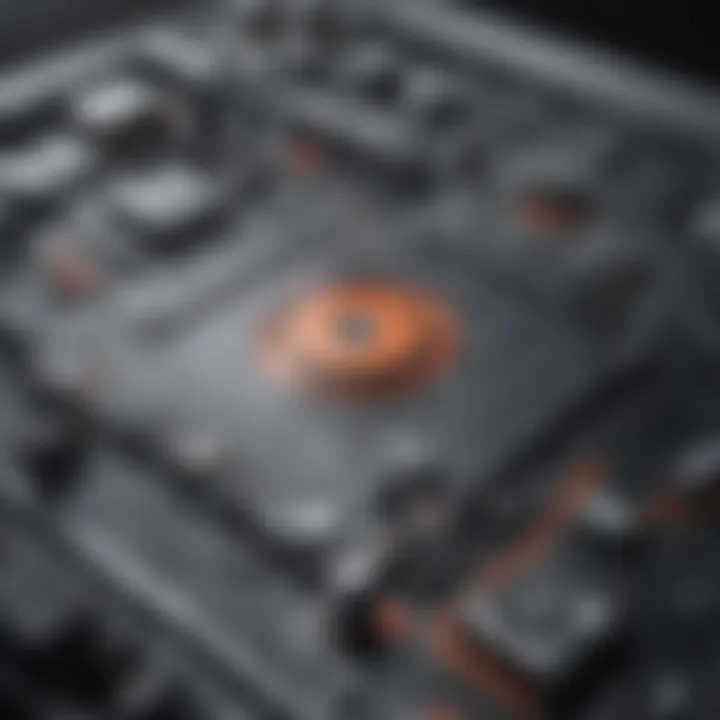
Software Overview
Engineering CAD software stands as a cornerstone in modern engineering processes, leveraging advanced functionalities to streamline design workflows and foster innovation. With a meticulous examination of its features and use cases, this article offers a comprehensive exploration of how CAD software empowers engineers to push boundaries and craft cutting-edge solutions. When it comes to pricing and licensing options, CAD software typically offers varying tiers to cater to diverse needs, ranging from individual freelancers to large enterprises. The software's compatibility across different platforms ensures seamless integration into existing workflows, enhancing collaboration and productivity.
User Experience
The user experience of engineering CAD software plays a pivotal role in its adoption and effectiveness. An intuitive interface design coupled with customizable user settings enhances usability, allowing engineers to tailor the software to their specific needs and preferences. Moreover, the performance and speed of CAD software are paramount, facilitating quick iteration and rendering of complex designs. This section delves into the ease of use, interface design, customizability, and overall performance efficiency of CAD software, offering a nuanced perspective on its user-centric features.
Pros and Cons
Delving into the strengths and advantages of engineering CAD software unveils a myriad of benefits, including enhanced design accuracy, iteration speed, and collaboration capabilities. However, every tool has its limitations, and CAD software is no exception. This section critically examines the drawbacks and limitations of CAD software, providing a balanced assessment of its pros and cons. Moreover, a comparative analysis with similar products sheds light on the distinct advantages and areas for improvement within the realm of CAD software.
Real-world Applications
The real-world applications of engineering CAD software span across various industries, from automotive and aerospace to architecture and consumer goods. Through case studies and success stories, this section showcases how CAD software drives innovation and problem-solving in diverse contexts. By highlighting industry-specific use cases and demonstrating how the software addresses specific challenges, readers gain insights into the practical applications and transformative potential of CAD software.
Updates and Support
The frequency of software updates and the availability of robust customer support are key considerations for businesses relying on engineering CAD software. Regular updates ensure access to the latest features and bug fixes, enhancing overall user experience and performance. Additionally, customer support options and community forums provide channels for users to seek assistance, share insights, and collaborate with peers. This section delves into the importance of software updates, customer support resources, and community engagement, underlining the significance of ongoing support in maximizing the value of CAD software.
Introduction to Engineering CAD Software
Engineering CAD software plays a critical role in driving innovation and enhancing product development processes. It revolutionizes the way engineers design and collaborate, offering a myriad of features to streamline workflows and boost efficiency. Through sophisticated modeling techniques and simulation tools, CAD software empowers engineers to push boundaries and create cutting-edge solutions. The precise nature of CAD tools ensures that design accuracy is paramount, ultimately leading to superior end products. Furthermore, the collaborative nature of CAD integration enables seamless communication among team members, fostering a dynamic work environment that thrives on innovation and effective project execution.
Evolution of CAD Technology
The Origins of CAD Systems
The evolution of CAD technology traces back to its humble beginnings where simple drafting functionalities laid the groundwork for complex design workflows. The Origins of CAD Systems marked a pivotal shift in engineering practices, transitioning from manual drafting to computerized design processes. This transition significantly enhanced design accuracy and speed, setting the stage for more sophisticated CAD solutions.
Technological Advancements in CAD
Over time, Technological Advancements in CAD have propelled the industry forward, introducing advanced features such as 3D modeling, parametric design, and simulation capabilities. These advancements have revolutionized the efficiency and precision of engineering design, allowing for intricate designs and complex analysis to be conducted with ease.
Impact of CAD on Engineering Practices
The Impact of CAD on Engineering Practices cannot be overstated, as it has reshaped how engineers approach design challenges. CAD tools have optimized workflows, leading to faster prototyping and reduced time-to-market for products. Additionally, the integration of CAD software has enabled engineers to iterate swiftly on designs, explore innovative solutions, and drive product innovation with unparalleled speed.
Key Features of Engineering CAD Software
Parametric Modeling
Parametric Modeling is a cornerstone feature of Engineering CAD Software, offering engineers the flexibility to create complex geometric shapes and establish design relationships effortlessly. By defining key parameters and constraints, engineers can explore various design iterations quickly, speeding up the design process and enhancing overall productivity.
Assembly Design
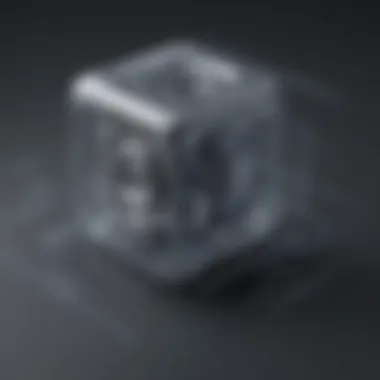
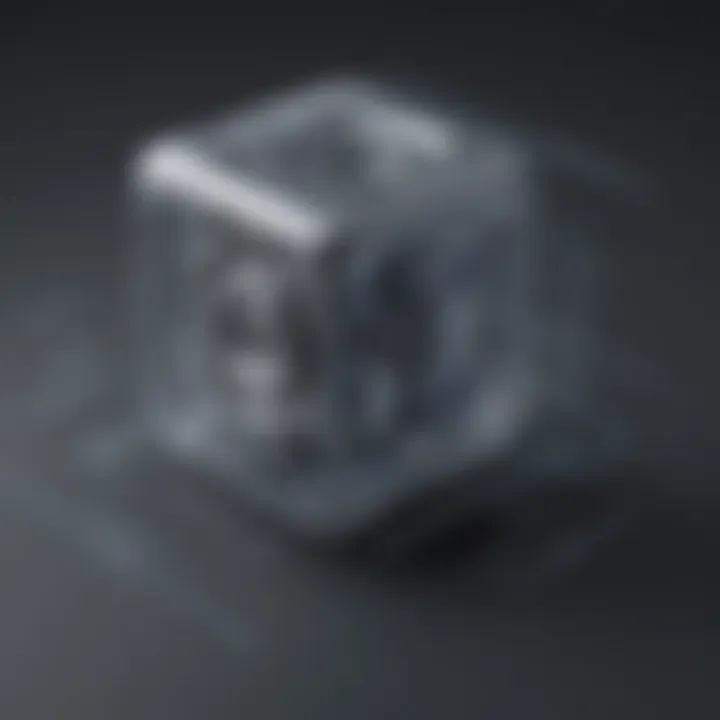
Assembly Design plays a crucial role in simulating how individual components come together to form a cohesive product. This feature enables engineers to visualize the interaction between parts, ensuring design compatibility and functionality before moving to the manufacturing phase.
Finite Element Analysis
Finite Element Analysis is a powerful tool that allows engineers to simulate product performance under various conditions. By subjecting designs to rigorous analysis, engineers can optimize structural integrity, material selection, and overall performance, ensuring that products meet stringent performance criteria.
Generative Design
Generative Design leverages algorithms and artificial intelligence to create innovative design solutions. By exploring myriad design alternatives based on specified inputs and constraints, engineers can uncover novel design approaches that combine efficiency, aesthetics, and functionality in unprecedented ways.
Benefits of CAD Software Integration
Enhanced Design Accuracy
One of the primary benefits of CAD software integration is Enhanced Design Accuracy, ensuring that product designs align precisely with specifications. This feature minimizes errors, reduces rework, and enhances the overall quality of products, fostering a culture of excellence and precision in engineering practices.
Time and Cost Savings
CAD software integration streamlines design processes, leading to significant Time and Cost Savings for engineering projects. By automating manual tasks, optimizing design workflows, and facilitating rapid prototyping, engineers can expedite project timelines, reduce operational costs, and gain a competitive edge in increasingly complex markets.
Improved Collaboration
Improved Collaboration is a key advantage of CAD software integration, as it facilitates seamless communication and teamwork among engineers, designers, and stakeholders. Real-time collaboration tools, version control features, and shared project dashboards enable teams to work cohesively towards common goals, fostering innovation, creativity, and efficient project delivery.
Efficient Prototyping
Efficient Prototyping capabilities offered by CAD software enable engineers to create physical prototypes quickly and accurately. By simulating designs in a virtual environment, engineers can test functionalities, validate performance metrics, and refine designs iteratively, leading to optimized product development cycles and streamlined production processes.
Applications of CAD Software in Engineering
When delving into the realm of engineering CAD software, it becomes evident that its applications play a crucial role in driving innovation and enhancing product development processes. CAD software is not merely a tool for drafting or modeling; it serves as a comprehensive solution that empowers engineers to streamline design workflows, foster collaborative prototyping, and ultimately revolutionize how products are conceptualized and brought to life. By utilizing CAD software, engineers can navigate complex design challenges, iterate more efficiently, and leverage advanced simulation capabilities to push the boundaries of what is possible in engineering. The strategic integration of CAD software into engineering workflows is instrumental in optimizing design accuracy, reducing time-to-market, fostering interdisciplinary collaboration, and enabling rapid prototyping. The profound impact of CAD software in modern engineering practices underscores its significance as a foundational technology shaping the future of innovation and product development.
Mechanical Engineering
Machine Design
Machine design is a pivotal aspect of mechanical engineering that involves the creation of machine components and systems with optimal functionality, efficiency, and reliability. Within the context of CAD software, machine design becomes a dynamic process facilitated by parametric modeling, virtual assembly analysis, and integrated finite element analysis capabilities. These features allow mechanical engineers to visualize, simulate, and optimize machine designs in a digital environment, thereby reducing physical prototyping iterations and enhancing overall design efficiency. The unique advantage of machine design in CAD software lies in its capacity to expedite the design iteration process, predict performance outcomes, and mitigate potential design flaws before physical production. This proactive approach to machine design not only improves product quality but also accelerates time-to-market and fosters innovation by empowering engineers to experiment with novel design concepts and functionalities.
Thermal Analysis
Thermal analysis stands at the forefront of mechanical engineering, informing the design and optimization of components subjected to thermal loads and environmental conditions. When incorporated into CAD software, thermal analysis tools enable engineers to evaluate the thermal performance of designs, identify potential overheating issues, and optimize cooling strategies to enhance product reliability. The key characteristic of thermal analysis in CAD software is its ability to simulate complex heat transfer phenomena within a design, providing valuable insights into temperature distribution, thermal stresses, and thermal management strategies. By harnessing thermal analysis capabilities, mechanical engineers can validate design decisions, refine material selections, and ensure that products meet stringent thermal performance requirements. Despite its computational intensity, thermal analysis significantly minimizes prototyping costs, enhances product durability, and accelerates the design optimization process in the realm of mechanical engineering.
Kinematic Simulation
Kinematic simulation plays a vital role in mechanical engineering by facilitating the analysis of motion, kinematics, and dynamic behavior within mechanical systems. When integrated into CAD software, kinematic simulation tools empower engineers to visualize and validate the motion of machine components, verify assembly clearances, and optimize mechanisms for intended functionalities. The key characteristic of kinematic simulation in CAD software is its ability to predict system behavior, evaluate inter-component interactions, and identify potential motion constraints or failures early in the design cycle. By leveraging kinematic simulation, mechanical engineers can iteratively refine their designs, improve operational efficiency, and ensure that mechanical systems operate seamlessly in real-world applications. Despite its complexity, kinematic simulation offers unparalleled insights into mechanical system performance, enables iterative design refinement, and ultimately drives innovation in mechanical engineering disciplines.
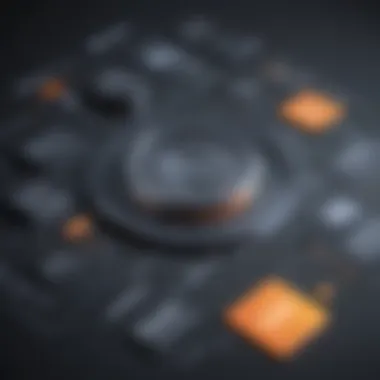
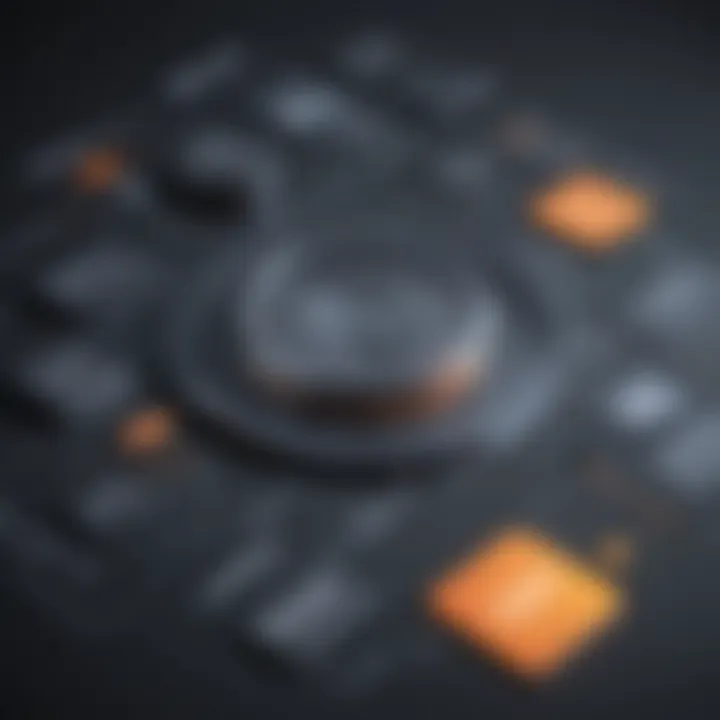
Future Trends in CAD Software Development
In the realm of engineering CAD software, exploring Future Trends in CAD Software Development is crucial. It represents the evolution and advancements that will shape the future of product development and innovation. As technology progresses, engineers need to adapt to new methodologies and tools to stay ahead in the competitive market. Understanding these trends provides a strategic advantage, allowing businesses to leverage the latest tools for improved efficiency and cutting-edge solutions.
Cloud-Based CAD Solutions
Advantages of Cloud Integration:
Cloud Integration offers a pivotal solution for storing and accessing CAD data remotely. It streamlines collaboration by enabling real-time sharing and editing of design files from different locations. The scalability of cloud resources ensures that engineering teams can access the necessary tools and data without being limited by hardware constraints. Additionally, version control and centralized data storage enhance workflow coordination and project management.
Security Considerations:
When implementing Cloud-Based CAD Solutions, security becomes a primary concern. Data encryption, secure access controls, and regular audits are essential to prevent unauthorized access or data breaches. Maintaining data integrity and confidentiality is vital to protect intellectual property and sensitive information stored on the cloud. Balancing convenience with robust security measures is key to ensuring a safe and efficient cloud-based CAD environment.
Scalability and Accessibility:
The scalability of cloud services allows engineering teams to adjust their resource usage based on project demands. This flexibility ensures that businesses can efficiently scale up or down their CAD requirements without incurring substantial costs. Accessibility to CAD tools and data from any location with internet connectivity promotes remote work capabilities and enhances cross-functional collaboration. However, ensuring reliable internet connectivity is essential for uninterrupted access to cloud resources.
AI and Machine Learning in CAD
Automated Design Optimization:
AI-powered tools enable Automated Design Optimization, automating the iterative process of refining designs for improved performance and efficiency. By analyzing vast amounts of design data, AI algorithms can suggest optimal solutions, reducing human error and speeding up the design phase. Engineers can explore diverse design options quickly, ultimately leading to more innovative and functional products.
Predictive Analysis:
Leveraging machine learning algorithms, Predictive Analysis forecasts potential design outcomes based on historical data and performance metrics. By predicting potential bottlenecks or issues early in the design phase, engineers can proactively address challenges and optimize their designs for better results. This predictive capability enhances decision-making and risk management throughout the product development lifecycle.
Enhanced Simulation Capabilities:
Integrating AI and machine learning technologies into CAD software enhances Simulation Capabilities, allowing for more accurate and realistic simulations. Advanced algorithms can simulate complex behaviors and interactions within designs, providing valuable insights for improving performance and durability. By leveraging AI-driven simulations, engineers can refine designs efficiently, leading to optimized products and streamlined development processes.
Integration with IoT and Industry
Smart Manufacturing Applications:
Integrating CAD software with IoT technologies enables Smart Manufacturing Applications, optimizing production processes and enhancing product quality. By connecting CAD models with IoT sensors and devices, manufacturers can gather real-time data on equipment performance and product functionality. This data-driven approach enables predictive maintenance, efficient resource utilization, and continuous product improvement.
IoT Data Integration:
IoT Data Integration empowers engineers to incorporate real-time data streams into their CAD designs, enabling dynamic modeling and analysis. By capturing data from IoT devices within the design environment, engineers can simulate real-world scenarios and optimize product performance. This integration ensures that designs are tailored to specific requirements and responsive to changing operational conditions.
Interconnectivity with Cyber-Physical Systems:
CAD software's Interconnectivity with Cyber-Physical Systems bridges the gap between virtual design and physical implementation. By integrating CAD models with IoT devices and control systems, engineers can create cyber-physical prototypes that mirror real-world behavior. This seamless connection facilitates iterative design improvements, predictive maintenance, and optimization of manufacturing processes for Industry 4.0 applications.
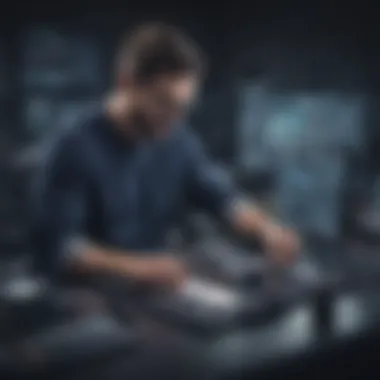
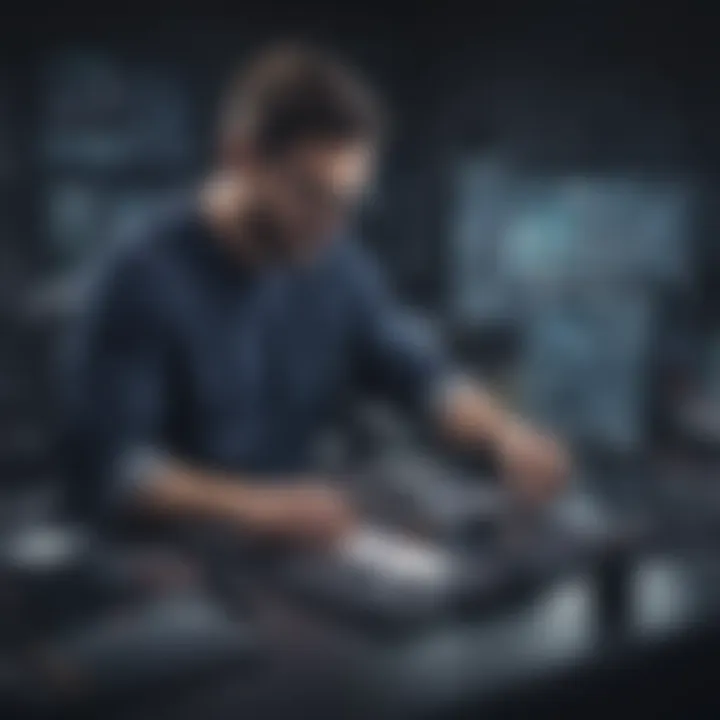
Challenges and Considerations in CAD Implementation
Engineering CAD Software comes with its set of challenges and considerations that are pivotal in understanding its impact on innovation and product development. One of the key elements in CAD Implementation is Training and Skill Development. It is of utmost importance to focus on upskilling the workforce to leverage the full potential of CAD software. Upskilling the Workforce involves enhancing the knowledge and expertise of employees in utilizing CAD tools effectively. By investing in training programs, companies can ensure that their workforce stays updated with the latest advancements in CAD technology, leading to improved productivity and quality in engineering projects.
Continuous Training Programs play a crucial role in maintaining a dynamic workforce proficient in CAD software. These programs offer ongoing education and skill development opportunities to employees, ensuring that they remain competent in using CAD tools efficiently. By providing continuous training, organizations can nurture a culture of learning and innovation, ultimately driving better utilization of CAD software for enhancing product development processes. However, addressing Resistance to Change is also essential when implementing CAD systems. Employees may resist adopting new CAD technologies due to unfamiliarity or fear of change. Thus, organizations need to implement strategies to address this resistance by emphasizing the benefits and providing adequate support during the transition phase.
Training and Skill Development
Upskilling the Workforce
Upskilling the Workforce entails a focused effort on enhancing the technical competencies of employees to effectively use CAD software. This process involves providing training sessions, workshops, and resources aimed at improving employees' proficiency in utilizing CAD tools for design and analysis tasks. The key characteristic of Upskilling the Workforce is its ability to empower employees with the skills needed to leverage CAD software optimally. This approach is a popular choice for organizations looking to enhance their engineering capabilities through a well-trained workforce. The unique feature of Upskilling the Workforce is its capacity to boost innovation and efficiency within teams, resulting in higher-quality engineering outputs.
Continuous Training Programs
Continuous Training Programs involve ongoing educational initiatives that allow employees to continually enhance their CAD skills. These programs focus on providing regular updates on software features, advanced techniques, and industry best practices to keep employees abreast of the latest developments in CAD technology. The key characteristic of Continuous Training Programs is their iterative nature, ensuring that employees receive continuous education to maintain their proficiency in CAD software. This approach is a beneficial choice for organizations seeking sustained growth and innovation in their engineering processes. The unique feature of Continuous Training Programs is their role in fostering a culture of continuous learning and improvement among employees, leading to enhanced productivity and creativity in engineering projects.
Addressing Resistance to Change
Addressing Resistance to Change is crucial in the successful implementation of CAD systems within organizations. Overcoming employee resistance to new CAD technologies requires a staged approach that involves clear communication, training, and support mechanisms. The key characteristic of Addressing Resistance to Change lies in its ability to identify and mitigate the factors that hinder employee acceptance of CAD software. This approach is a beneficial choice as it ensures a smoother transition to new CAD tools, minimizing potential disruptions in engineering workflows. The unique feature of Addressing Resistance to Change is its emphasis on cultivating a positive attitude towards change and innovation, fostering a conducive environment for embracing new technologies and practices.
Data Security and Intellectual Property
In the realm of CAD Implementation, ensuring Data Security and Intellectual Property protection is paramount to safeguarding critical engineering designs and proprietary information. Secure Data Management Practices play a crucial role in mitigating data breaches and unauthorized access to CAD files. By implementing encryption, access controls, and secure storage protocols, organizations can protect their sensitive design data from cyber threats and unauthorized sources. The key characteristic of Secure Data Management Practices is their focus on establishing robust mechanisms for data protection and confidentiality, making them a popular choice for maintaining the integrity of engineering data.
Secure Data Management Practices
Secure Data Management Practices involve the implementation of secure protocols and technologies to protect CAD data from unauthorized access and cyber threats. This includes encryption methods, secure data transfer mechanisms, and data leakage prevention strategies to ensure data integrity and confidentiality. The key characteristic of Secure Data Management Practices is their emphasis on data security and privacy, providing a secure environment for CAD file storage and sharing. This approach is a beneficial choice for organizations handling sensitive design information and intellectual property, as it mitigates the risk of data breaches and compromises.
Confidentiality Protocols
Confidentiality Protocols are essential in safeguarding sensitive CAD information from unauthorized disclosure or tampering. These protocols establish guidelines and procedures for handling confidential design data, ensuring that only authorized personnel have access to crucial engineering information. The key characteristic of Confidentiality Protocols is their role in maintaining data confidentiality and protecting intellectual property rights. This approach is a popular choice for organizations dealing with proprietary design data and confidential project information, as it reduces the risk of data leakage and unauthorized use.
IP Protection Strategies
Protecting Intellectual Property (IP) within CAD systems is vital to preserving the innovation and creativity invested in engineering designs. IP Protection Strategies encompass measures such as patenting design inventions, implementing access restrictions, and monitoring IP usage within CAD software. The key characteristic of IP Protection Strategies is their focus on safeguarding the uniqueness and originality of engineering creations, ensuring that companies retain control and ownership over their innovative designs. This approach is a beneficial choice for organizations seeking to prevent IP theft and unauthorized replication of their design concepts, fostering a secure environment for fostering innovation and competitive advantage.
Compatibility and Integration Challenges
The integration of CAD software into existing engineering workflows poses certain compatibility and integration challenges that need to be addressed for seamless operations. Legacy System Migration involves transitioning from traditional design tools to modern CAD software, necessitating data conversion and process reengineering. By migrating legacy systems to CAD platforms, organizations can leverage the advanced features and capabilities of modern design tools for enhanced productivity and innovation in engineering projects. However, Interoperability Issues may arise when CAD software lacks compatibility with other design or analysis tools used within the organization.
Legacy System Migration
Legacy System Migration involves the process of transitioning from traditional design software to modern CAD systems. This migration often requires data conversion, training, and workflow adjustments to effectively integrate CAD tools into existing engineering processes. The key characteristic of Legacy System Migration is its potential to revamp outdated design practices and streamline workflows through the adoption of advanced CAD features. This approach is a popular choice for organizations looking to modernize their engineering capabilities and align with industry standards. The unique feature of Legacy System Migration is its ability to unlock new design possibilities and efficiencies, ultimately enhancing product development outcomes.
Interoperability Issues
Interoperability Issues can arise when CAD software is incompatible with other engineering tools or platforms utilized in the organization's workflows. These issues may hinder data exchange, collaboration, or integration between CAD systems and other software applications, leading to operational inefficiencies and data discrepancies. The key characteristic of Interoperability Issues is their impact on seamless data flow and communication between different engineering software, raising challenges in achieving integrated and cohesive design processes. This challenge necessitates proactive measures to ensure software compatibility and data interoperability, optimizing engineering workflows and project outcomes.
Software Ecosystem Integration
Software Ecosystem Integration involves the harmonious integration of CAD software with other engineering tools, vendor applications, or third-party platforms to create a cohesive digital environment. By integrating CAD systems within the software ecosystem, organizations can streamline data exchange, software updates, and collaborative efforts across various engineering disciplines. The key characteristic of Software Ecosystem Integration is its ability to establish interconnected workflows and distributed design processes that enhance productivity and innovation. This approach is a beneficial choice for organizations seeking holistic solutions for their engineering needs, as it promotes synergy between different software platforms and maximizes the efficiency of product development workflows.